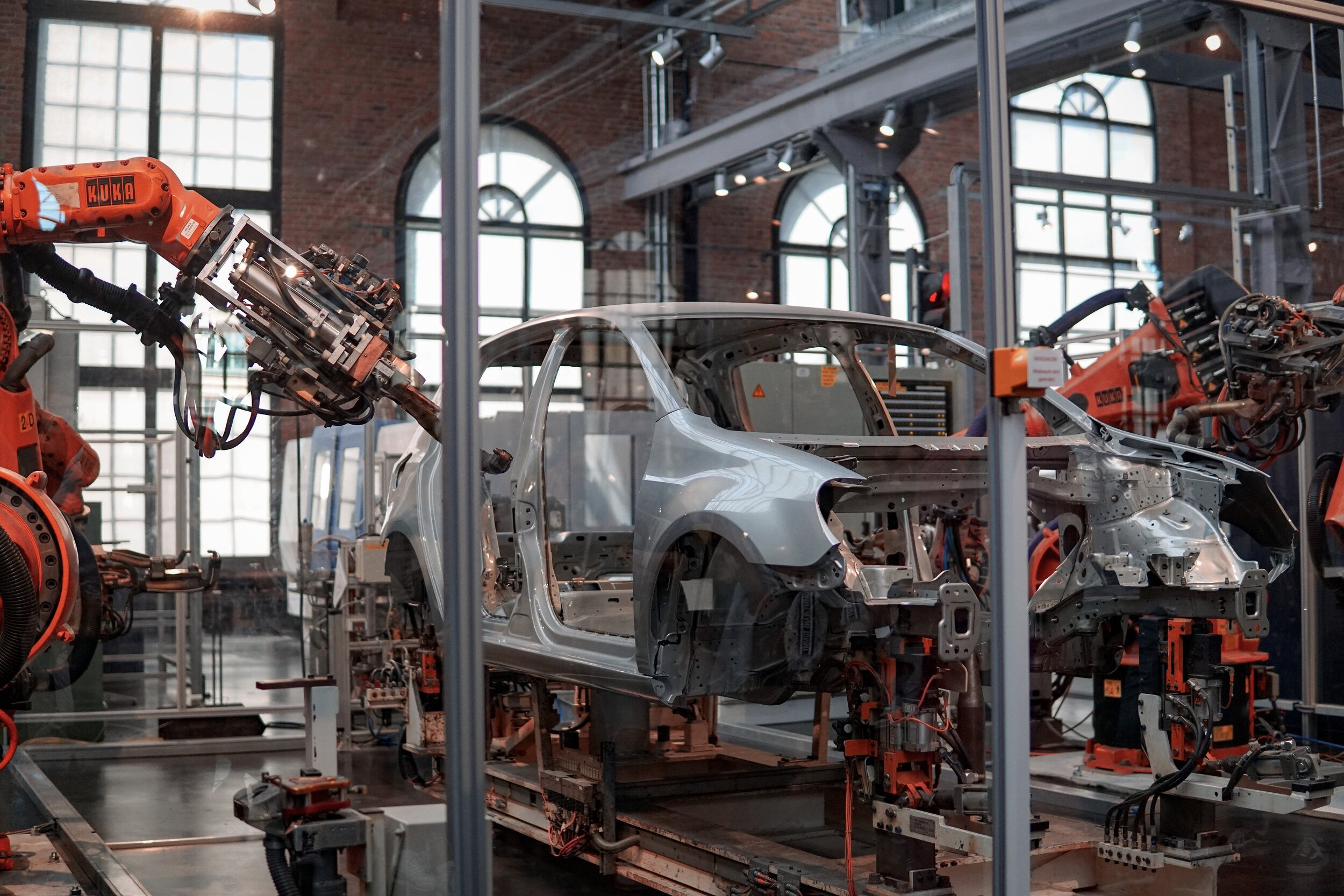
LANGUAGE OF LEAN
MTM
MTM (Methods Time Measurement) is a systematic method for analyzing and optimizing work processes that is widely used in the field of Lean Management.
MTM (Methods Time Measurement) is a systematic method for analyzing and optimizing work processes that is widely used in the field of Lean Management. MTM is based on the idea of breaking down work into small, easily analyzed and optimized tasks, and is therefore an important tool for improving efficiency and productivity in operations.
The origin of MTM can be traced back to the early 20th century, when industrial engineers in Europe and the United States first began to develop time-and-motion studies. These early studies sought to identify the most efficient ways to perform tasks and reduce waste in manufacturing operations. Over time, MTM evolved into a standardized methodology, with clear guidelines and tools for process analysis and improvement.
One of the key features of MTM is its focus on standardizing work processes. This is accomplished by breaking down each task into its component parts and then determining the most efficient way to perform each part. The result of this analysis is a set of standardized work methods that can be used to train workers and ensure consistency in operations.
Another important aspect of MTM is its focus on continuous improvement. The MTM methodology includes regular reviews of work processes and the use of data and analysis to identify areas for improvement. This approach helps organizations to continuously improve their operations and remain competitive over time.
One of the best ways to utilize MTM is in the context of Lean management. In Lean, the focus is on identifying and eliminating waste in all aspects of operations. By applying the MTM methodology to work processes, organizations can identify inefficiencies and then work to eliminate them. This helps to create a more streamlined, efficient, and productive work environment.
Another important application of MTM is in the context of training and development. By using MTM to analyze and standardize work processes, organizations can provide clear and consistent training to workers. This helps to ensure that all workers are performing their tasks in the most efficient way, which leads to improved productivity and reduced waste.
Finally, MTM can also be used in the context of project management. By analyzing work processes in advance of a project, organizations can ensure that they have the resources and capabilities needed to complete the project on time and within budget.
In a nutshell, MTM is a powerful tool for improving efficiency and productivity in operations. Its focus on standardizing work processes and its emphasis on continuous improvement make it an ideal methodology for Lean management and for organizations looking to improve their operations over time.
JIT
Just-in-Time (JIT) is a manufacturing and inventory control system in which raw materials, components, and finished products are delivered to the production line exactly when they are needed.
Just-in-Time (JIT) is a manufacturing and inventory control system in which raw materials, components, and finished products are delivered to the production line exactly when they are needed. The goal of JIT is to minimize inventory levels and reduce lead times, while maintaining high levels of production efficiency.
JIT is a pull-based system, which means that production is driven by customer demand rather than by a production schedule. This is achieved by using Kanban, a signaling system that alerts the supplier to send more materials or components when the inventory level of a specific item reaches a predetermined minimum level.
The origins of JIT can be traced back to the manufacturing practices of the Toyota Motor Company in the 1950s. It was developed by Taiichi Ohno, an engineer at Toyota, as a response to the inefficiencies he observed in the company's production processes. Ohno recognized that by reducing the amount of inventory and increasing the flow of materials, Toyota could improve its production efficiency and responsiveness to customer demand.
One of the key principles of JIT is the elimination of waste, or "muda" in Japanese. Ohno identified seven types of waste in manufacturing: overproduction, waiting, unnecessary motion, overprocessing, defects, excess inventory, and unused human potential. JIT aims to eliminate these forms of waste by creating a smooth and efficient flow of materials and products through the production process.
JIT also relies on the concept of "one piece flow", which is the production of one item at a time, rather than producing large batches of items. This allows for better control of the production process, as well as the ability to quickly identify and correct any problems that may arise.
Another important aspect of JIT is the use of visual management tools, such as Andon boards and Kanban boards. These tools allow for real-time monitoring of the production process, and can alert workers to potential problems before they become major issues.
JIT also requires a high level of collaboration and communication between suppliers, manufacturers, and customers. This is necessary to ensure that materials and components are delivered to the production line exactly when they are needed, and that finished products are delivered to customers in a timely manner.
JIT has a number of benefits for manufacturers. One of the most significant is that it can help to reduce inventory levels, which can free up valuable floor space, reduce storage costs, and minimize the risk of stockouts. JIT can also help to improve production efficiency by reducing lead times and minimizing downtime caused by waiting for materials or components.
JIT can also help to improve product quality by reducing defects, and increasing the ability to quickly identify and correct any problems that may arise in the production process.
JIT also helps companies to be more responsive to customer demand by reducing lead times and increasing the speed of delivery. This can help to improve customer satisfaction, and increase the chances of repeat business.
JIT also helps companies to be more flexible and adaptable to changes in customer demand. It allows companies to more easily shift production to different products or product lines, which can help to maintain profitability during periods of slow sales.
However, it's worth noting that JIT is not suitable for all industries and companies, it's best applied in companies where the production process is well-defined, the demand is stable and predictable, and the lead times are short. Implementing JIT can also be challenging and requires a significant investment of time and resources to establish an effective system.
Additionally, JIT requires a high level of coordination and communication with suppliers and customers, which can be difficult to achieve. This is particularly true for companies that have a large number of suppliers or customers, or those that operate in
Smoothed Production
Smoothed production is integral for customer satisfaction as it is a part of the ordering and complete fulfillment process. It makes sure that the supply chain capabilities are enough for stable production.
The topic of discussion today will be the so-called smoothed production. It is integral for customer satisfaction as it is a part of the ordering and complete fulfillment process. It makes sure that the supply chain capabilities are enough for stable production.
Smooth production benefits you by having a proper influence on your workplace configuration. It does this by helping to create a stable output with optimized inventory via a pre-condition. This presupposition/pre-condition simplifies your workplace based on the following conditions:
Standardized work processes
One-Piece Flow within the workstation
Complete processing
Stabile customer TAKT TIME
Minimal TAKT TIME loss
Maximum Output
Flexible deployment of workers
Quicker material change
Two-Bin-Principle
The smooth production is structured in the following:
Planning Strategy
Constant lot sizes
Stabile material needs
Fixed production times
Flexible inventories
Fixed timelines
Higher delivery dependability
It is implemented by:
Material flow
Scheduling methods
No part shortages
Pull-principle
Supermarket
Route traffic
Small containers
Warehouse Organization
Full transparency
Minimal warehouse levels
Set assembly
Bar codes and Data Matrix Codes
You may be asking the question, “but why do we need smooth production?”
It is a well-known fact that smooth production has many veritable advantages. With that said, there are also some potential drawbacks, but those can be eliminated or at the very least mitigated in the implementation phase.
Here are some of the benefits and drawbacks of smooth production:
The next question you might be asking is, “how does one implement smooth production?”.
Following are some of the requirements for smooth production:
Variable worker allocations should be the basis for the production power of the system. The variable shift models are first optimized for maximum output and then implemented specifically.
Two factors determine the minimum inventory of safety stock for a part number. The first is the variability in customer ordering habits. The second factor is the degree to which the program is successful in the production line. To hit the right spot between these two factors will require systematic optimization with the help of a mathematical model.
To determine what the maximum inventory of each part number should be, we should look at the delivery cycle of that said part number. This is essential for weekly pick-ups or delivery.
The production equipment inventory should be in accordance with necessary tool changes and set-up times.
The weekly production plan should be consistently released to the concerned parties once the production macro planning has been finished.
An information board at the assembly areas will contain all the planned orders.
The material requirement determination should solely be on the basis of the production plan.
Assembly areas should be designated for the online measurement of production units. A data matrix system should be implemented for reducing errors in the documentation process.
The ability to control production is a must if there are any noticeable short-term reactions arising due to discrepancies between the expected outcome and the actual outcome of the production plan.
Any daily deviations must be dealt with proper countermeasures. The production plan must be flexible enough to allow time to deal with backlogs. Meeting shipping deadlines is the primary goal.
A time-saving approach must be implemented in moving full racks from assembly areas to warehousing.
The requirements of the long-term sales plan should be integrated into the production plan so that production capacities and worker allocation are determined.
It is imperative that order calling and Just-In-Time delivery schedule data be automatically transferred to the resource planing system so that production planning can be done.
The production planning for the system will determine the specific production calendars with your organizations shift models.
All underlying data in the system must contain related shipping dates or the dates can be transferred from the demand data as well.
To control the complete system, the updated inventory trend with planned shipping dates, for example, weekly and monthly, should be represented graphically.
All possible scenarios should be simulated, because it is important to determine optimum capacities, performance, etc. for universal or shared production areas.
So, what factors make smooth production successful?
The two factors are planned output realization and controlling of supply
Production plan fulfillment as a part of planned output realization (source: Information board at production area as part of shop floor mgt)
Performance grading of workers in the production area that is done on the basis of the number of Dollars created in exchange for optimal material usability and worker effort (whether overtime or temporary workers)
Material usability of purchased parts, WIP, and raw materials when assembly time bears the cost or parts become short (Source: Information board at production area as part of shop floor mgt)
Special trips for the respective assembly area as a truthful Dollar figure
Supply capabilities and service grade for finished goods are measured using the number of delivered parts and the number of delivery dates met as a result of customer requests when demand data is transferred. (Source: Information board at production area as part of shop floor mgt)
Alternative measures for the success of smooth production:
Usage of constant customer feedback to determine customer satisfaction as used by companies e.g. from the automotive industry
Iterative comparison of customer feedback with important shipping and delivery figures
Target values of no customer feedback are used to get parameters to measure with
With the help of Kaizen workshops in conjunction with the introduction and implementation are used to create optimal basic parameters of success:
The finished goods inventory levels are available transparently to be used as an early warning signal
A minimal failure rate is strived for in the overall process of making sure of data from the production and logistics division
Over-production of products is reduced by ensuring that upstream assemblies are only producing the right amount of product to be used by the downstream processes
With the implementation of workshops, the set-up time can be reduced drastically
Constant reduction of purchase parts does not diminish the availability of the material in the production line while also reducing downtime
Optimal balance is achieved for assembly lines and areas and the requirements are met for variable worker allocation
The specifications of operator qualification shall determine how the qualification and training of workers should be conducted
There has been evidence of improvement in production flexibility in comparison to the past
Lighthouse Project
When talking about Light House Projects this means nothing less than that a small sector of your organization e.g a department is already turned around.
When talking about Light House Projects this means nothing less than that a small sector of your organization e.g a department is already turned around. By that we are talking about living already the ideal state, that you defined for the complete organization.
Processes and structures can be seen as guidance for your organizations’ lean journey. It provides directions, shows what is possible and therefore is the kickstarter for a successful roll-out as people can convince themselves with their own eyes.
Just keep in mind that the lean journey with its process of continuous improvement is never over. The pioneer has to lead the way.
SMED
Single Minute Exchange of Die. A method of increasing the amount of productive time and to reduce the planned downtime to single digit minutes.
Single Minute Exchange of a Die
This series of techniques was invented by Shigeo Shingo to set-up manufacturing equipment in less than 10 minutes. Most of the time people think in one minute but is thought as single digit minutes.
So what is behind the set-up time reduction?
This method is driving to increase the net production time as much as possible by minimizing the needed time to change from one model to another. As far as you have two or more products running on your line or to simply exchange parts of your machine or equipment that regularly needs to be replaced. This is increasing the flexibility of your production and allows you to react on changes in demand more quickly.
When trying to reduce changeover tomes the typical goal is to reach less than 10 minutes. The short summary of SMED activities is to analyze each element of the changeover with the EMIPS method to see if it can be eliminated, modified or moved outside the process, integrated, tasks are parallelized or synchronized.
SMED
When looking at those three stages we can simplify it further for each stage:
Just ask yourself:
Separate:
Can this task, as currently performed, be done while the line is still running?
Convert:
Which process steps can be moved out of the changeover itself and be parallelized or completely taken out? How can you do it?
Synchronize:
How can the remaining tasks be synchronized so you need as little time as possible to complete the changeover?
I save you the story with the pit stop in formula 1 - just google it by yourself and you will find the evolution of pit stops. Quite interesting and still valuable.
So what are the benefits of SMED?
The first effect you will see on improvements of the OEE of your manufacturing facility. If this is important for you and you are numbers driven. In the end you will reduce downtimes and therefore manufacturing costs as your machines will have a greater net operating time.
With a long term perspective SMED will enable you to have smaller batch sizes, which will improve your possibilities to react faster on changes of customer demands and in addition your inventory (tied capital) and WIP (work in progress) will decrease.
Stay Connected
Ad
We want information fast and in a nutshell. We from OI recommend Blinkist* - because it’s simply the best.
* = Affiliate Link