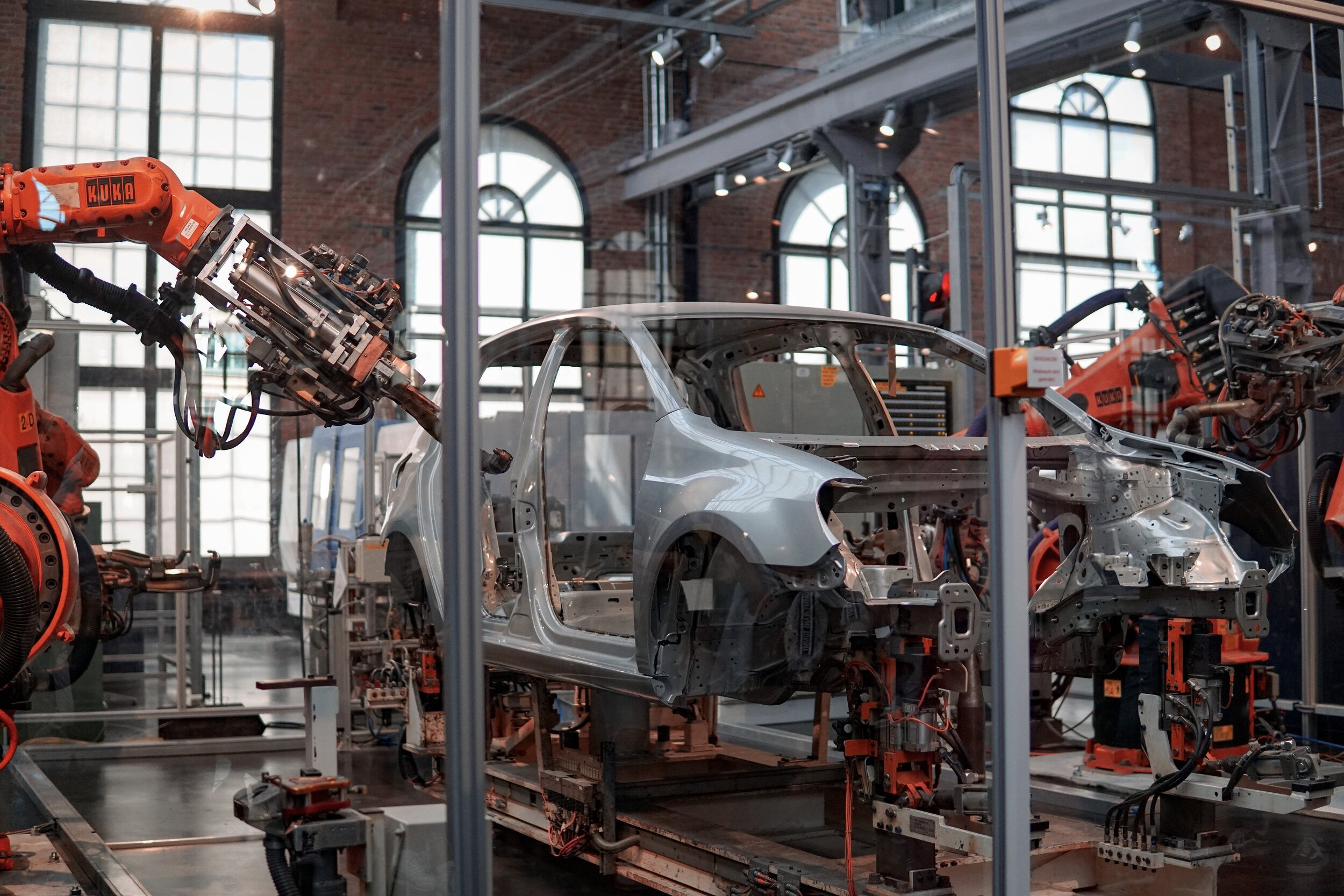
LANGUAGE OF LEAN
8D
8D Reports are used to communicate results of taken problem solving steps to the customer in a standard format.
The so called “8D”-Report is a document resulting from an 8D process which is part of a structured problem solving process in quality management if there are quality issues between customer and supplier.
8D represents the eight mandatory process steps that are performed when processing a claim to get to the root of the cause. The report details the nature of the claim, responsibilities, and actions taken to prevent the problem from reoccurring:
The 8D methodology is intended to ensure that complaints are dealt with systematically. Consistent documentation of the associated troubleshooting steps and a high level of fact orientation ensure that errors in the product or system are thoroughly investigated and thus permanently corrected instead of just solving the problem.
Application
These eight steps are performed for the 8D report:
1 Define a team to solve the problem
A team familiar with the process and/or the product is formed. They analyze the problem, take corrective actions, and monitor the effectiveness.
2 Describe the problem
In this step, the problem is defined as precisely as possible and the root cause of the problem is identified.
3 Containment action
These measures are intended to resolve the problem quickly and limit the damage until a permanent solution is found.
4 Root cause analysis
You probably haven’t found the real root cause during step 2 therefor various tests and experiments are used during step 4 to search for the real root cause of the error and the most likely causes are identified. This is intended to ensure that similar errors do not occur again.
5 Planning of counter measures
It then determines the means by which the causes of the problem can be eliminated. It is tested whether these measures solve the problem efficiently and no undesired side effects occur.
6 Check effectiveness of counter measures
Once the corrective actions have been carried out successfully, the immediate actions must be stopped. In the automotive industry, only process-improving measures are regarded as permissible shutdown measures.
7 Prevent recurrence of error
To ensure that such an error does not happen again, the team must initiate and monitor preventive measures. In the automotive and aerospace industries, manufacturers must use the FMEA method to assess the risks identified during root cause analysis. .Also, quality management system rules and procedures may need to be adjusted.
8 Appreciation of team performance and Lessons Learned
In a last step, the achievements of the team are recognized and experiences are exchanged.
Affinity Diagram
The affinity diagram helps you to organize a large number of ideas into logical categories and natural relations.
So you have a large number of ideas and need to organize them. The affinity diagram is the perfect fit to get the job done and to structure your ideas into their natural relationships. Basically the affinity diagram describes a structured outcome from a brainstorm session. You can use it to generate, organize and consolidate information related to a product or process, complex issues or different problems. After the brainstorming session you should group the ides according to their affinity or similarity. This idea creation method was created in the 1960s by Japanese anthropologist Jiro Kawakita.
When should you use an Affinity Diagram
The typical use of an Affinity Diagram is when you are confronted with many influences or ideas in a state of chaos. Sometimes a problem seems too large or just too complex to understand it at first sight. Or you simply want that the whole team has a common understanding of a topic.
Usually you are confronted with this situation:
After a brainstorming session
When analyzing open questionnaires, such as survey results
When collecting and organizing large sets of data
When trying to develop relationships between different ideas
Or trying to reduce input to a higher level of categories
Typical process of developing an Affinity Diagram
The Affinity Diagram process gives a group a direction to go beyond normal creative thinking and defines categories to get all thoughts in order. This technique opens the doors and shows relations in between the whole organization which is typically separated due to department silo thinking. The Affinity Diagram has no limits, so don’t be irritated if you have to deal from 20 up to 400 items after a session. It is a starting point not more not less.
Materials needed: Sticky notes or cards, marking pens, and for sure a large surface (wall, table, or floor). Brown paper is a good way to start.
Step 1:
The brainstorming
Write down all ideas on separate sticky notes or cards.
Spread the sticky notes or cards randomly all over the brown paper
Gather all participants around the brown paper after all notes are taken
Hint: Use big markers so it easy to read for everybody from distance. Make key statements on the notes don’t write an essay.
Step 2:
Try to sort all ideas that are related in some way and group them up
Try to find relations between these several ideas
Let the team sort ideas
Try to find 8-10 relation groups
Repeat until all ideas are grouped
It is fully reasonable that there might be an idea staying by itself or that team members will move an already grouped note again to another. If an idea belongs in two groups, make a second sticky note or card.
Hint: In this step it is crucial that there are chats going on, it has to be done in silence. Focus is on sorting and grouping ideas. Headlines are done afterwards! Not upfront!
Step 3:
Open discussion with your team.
Try to find common categories and define headlines for each group together with all team members. Discuss what you see or why members see an idea in a different category. If necessary, make changes and move ideas between categories. In the end, when all ideas are grouped in the consent of the whole team, define the headlines of each group. Try to find a catchy headline that describes the meaning of the category in short.
Hint: Cards with the headline should be in a different color than the rest and should be self explaining about the group.
Step 4:
If reasonable, try to define “mastergroups” of several “subgroups”.
Sort all ideas to their identified category by placing all ideas under the “headline card”.
Hint: The sorting is done by gut feeling, not with a scientific approach.
A3 Report
A3 Report and why it will help in the structure of the PDCA methodology.
The term A3 report comes simply from the size of paper which is used for the documentation of the report. The structure itself follows the PDCA methodology.
In the lean manufacturing world the best known use case of the A3 report is the problem solving report. In this case the responsible person from the quality department takes the A3 report, starts the problem solving actions and follows a systematic structure that makes it possible to describe the effects that are currently leading to a deviation from the standard. Using the A3 only makes sense when you don’t know the root cause yet. If you already know the root cause don’t waste your time. Fix it and go back to normal.
Schematic structure of an A3 report
Let us go through the different stages of an A3:
Describe the problem:
The A3 gives you the chance to initially describe the problem or symptoms - this can be done verbally or as a sketch. Don’t forget to mention when it was and under what circumstances. No matter what it must be easy to understand.
Keep in mind that the target in Lean Mgt. is always to train the people to improve their problem solving skills. Therefore if you are a quality representative try to coach the operators in this process or make a team work out of it.
The result of the description of the problem is the delta from the target state.
Root Cause Analysis:
Please be aware that your paper is only and A3 format. So either you go with an Ishikawa or a 5 Why. But not more. If you can’t conduct a root cause analysis with either on of these methods, the A3 is probably the wrong approach at all.
Counter Measures:
Following the PDCA plan your counter measures what you and your team or operators found out or might think have the most effect.
Lessons Learned:
Great you have done the job, you followed the PDCA and the root cause was found, defined measures helped and the problem is solved. No finalize the A3 report on where to find the documentation and what impact will it have on other operations as lessons learned.
When you are a quality representative using the A3 method ensure that the A3 report is also used for long term development of employees and quality standards.
With the help of the A3 report and a clear coaching through the quality department, all employees learn to recognize, evaluate and solve problems on their own. This is serving the general rule of continuous improvement (CIP)
Therefore the A3 systematic increases the problem solving competencies of your whole organization. And as already said, a problem is only the missing of an idea.
If you want to go deeper on the A3 report itself or the problem solving with the help of A3, we recommend our reading pick “Understanding A3 thinking” this book goes in the details and gives you great insights. Read our summary here. Or you can’t wait? Here is the link straight to the book:
Stay Connected
Ad
We want information fast and in a nutshell. We from OI recommend Blinkist* - because it’s simply the best.
* = Affiliate Link