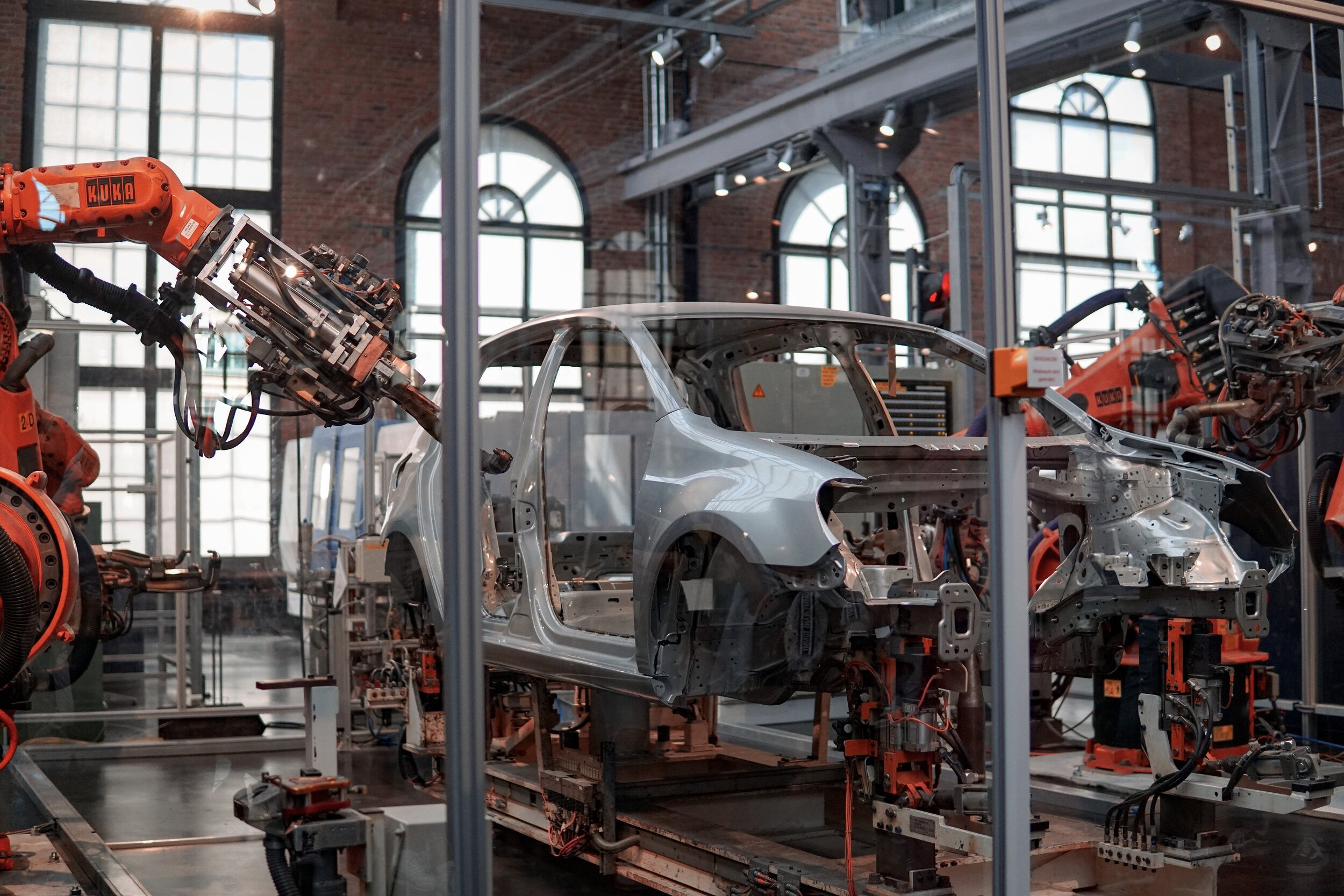
LANGUAGE OF LEAN
Smoothed Production
Smoothed production is integral for customer satisfaction as it is a part of the ordering and complete fulfillment process. It makes sure that the supply chain capabilities are enough for stable production.
The topic of discussion today will be the so-called smoothed production. It is integral for customer satisfaction as it is a part of the ordering and complete fulfillment process. It makes sure that the supply chain capabilities are enough for stable production.
Smooth production benefits you by having a proper influence on your workplace configuration. It does this by helping to create a stable output with optimized inventory via a pre-condition. This presupposition/pre-condition simplifies your workplace based on the following conditions:
Standardized work processes
One-Piece Flow within the workstation
Complete processing
Stabile customer TAKT TIME
Minimal TAKT TIME loss
Maximum Output
Flexible deployment of workers
Quicker material change
Two-Bin-Principle
The smooth production is structured in the following:
Planning Strategy
Constant lot sizes
Stabile material needs
Fixed production times
Flexible inventories
Fixed timelines
Higher delivery dependability
It is implemented by:
Material flow
Scheduling methods
No part shortages
Pull-principle
Supermarket
Route traffic
Small containers
Warehouse Organization
Full transparency
Minimal warehouse levels
Set assembly
Bar codes and Data Matrix Codes
You may be asking the question, “but why do we need smooth production?”
It is a well-known fact that smooth production has many veritable advantages. With that said, there are also some potential drawbacks, but those can be eliminated or at the very least mitigated in the implementation phase.
Here are some of the benefits and drawbacks of smooth production:
The next question you might be asking is, “how does one implement smooth production?”.
Following are some of the requirements for smooth production:
Variable worker allocations should be the basis for the production power of the system. The variable shift models are first optimized for maximum output and then implemented specifically.
Two factors determine the minimum inventory of safety stock for a part number. The first is the variability in customer ordering habits. The second factor is the degree to which the program is successful in the production line. To hit the right spot between these two factors will require systematic optimization with the help of a mathematical model.
To determine what the maximum inventory of each part number should be, we should look at the delivery cycle of that said part number. This is essential for weekly pick-ups or delivery.
The production equipment inventory should be in accordance with necessary tool changes and set-up times.
The weekly production plan should be consistently released to the concerned parties once the production macro planning has been finished.
An information board at the assembly areas will contain all the planned orders.
The material requirement determination should solely be on the basis of the production plan.
Assembly areas should be designated for the online measurement of production units. A data matrix system should be implemented for reducing errors in the documentation process.
The ability to control production is a must if there are any noticeable short-term reactions arising due to discrepancies between the expected outcome and the actual outcome of the production plan.
Any daily deviations must be dealt with proper countermeasures. The production plan must be flexible enough to allow time to deal with backlogs. Meeting shipping deadlines is the primary goal.
A time-saving approach must be implemented in moving full racks from assembly areas to warehousing.
The requirements of the long-term sales plan should be integrated into the production plan so that production capacities and worker allocation are determined.
It is imperative that order calling and Just-In-Time delivery schedule data be automatically transferred to the resource planing system so that production planning can be done.
The production planning for the system will determine the specific production calendars with your organizations shift models.
All underlying data in the system must contain related shipping dates or the dates can be transferred from the demand data as well.
To control the complete system, the updated inventory trend with planned shipping dates, for example, weekly and monthly, should be represented graphically.
All possible scenarios should be simulated, because it is important to determine optimum capacities, performance, etc. for universal or shared production areas.
So, what factors make smooth production successful?
The two factors are planned output realization and controlling of supply
Production plan fulfillment as a part of planned output realization (source: Information board at production area as part of shop floor mgt)
Performance grading of workers in the production area that is done on the basis of the number of Dollars created in exchange for optimal material usability and worker effort (whether overtime or temporary workers)
Material usability of purchased parts, WIP, and raw materials when assembly time bears the cost or parts become short (Source: Information board at production area as part of shop floor mgt)
Special trips for the respective assembly area as a truthful Dollar figure
Supply capabilities and service grade for finished goods are measured using the number of delivered parts and the number of delivery dates met as a result of customer requests when demand data is transferred. (Source: Information board at production area as part of shop floor mgt)
Alternative measures for the success of smooth production:
Usage of constant customer feedback to determine customer satisfaction as used by companies e.g. from the automotive industry
Iterative comparison of customer feedback with important shipping and delivery figures
Target values of no customer feedback are used to get parameters to measure with
With the help of Kaizen workshops in conjunction with the introduction and implementation are used to create optimal basic parameters of success:
The finished goods inventory levels are available transparently to be used as an early warning signal
A minimal failure rate is strived for in the overall process of making sure of data from the production and logistics division
Over-production of products is reduced by ensuring that upstream assemblies are only producing the right amount of product to be used by the downstream processes
With the implementation of workshops, the set-up time can be reduced drastically
Constant reduction of purchase parts does not diminish the availability of the material in the production line while also reducing downtime
Optimal balance is achieved for assembly lines and areas and the requirements are met for variable worker allocation
The specifications of operator qualification shall determine how the qualification and training of workers should be conducted
There has been evidence of improvement in production flexibility in comparison to the past
Stay Connected
Ad
We want information fast and in a nutshell. We from OI recommend Blinkist* - because it’s simply the best.
* = Affiliate Link