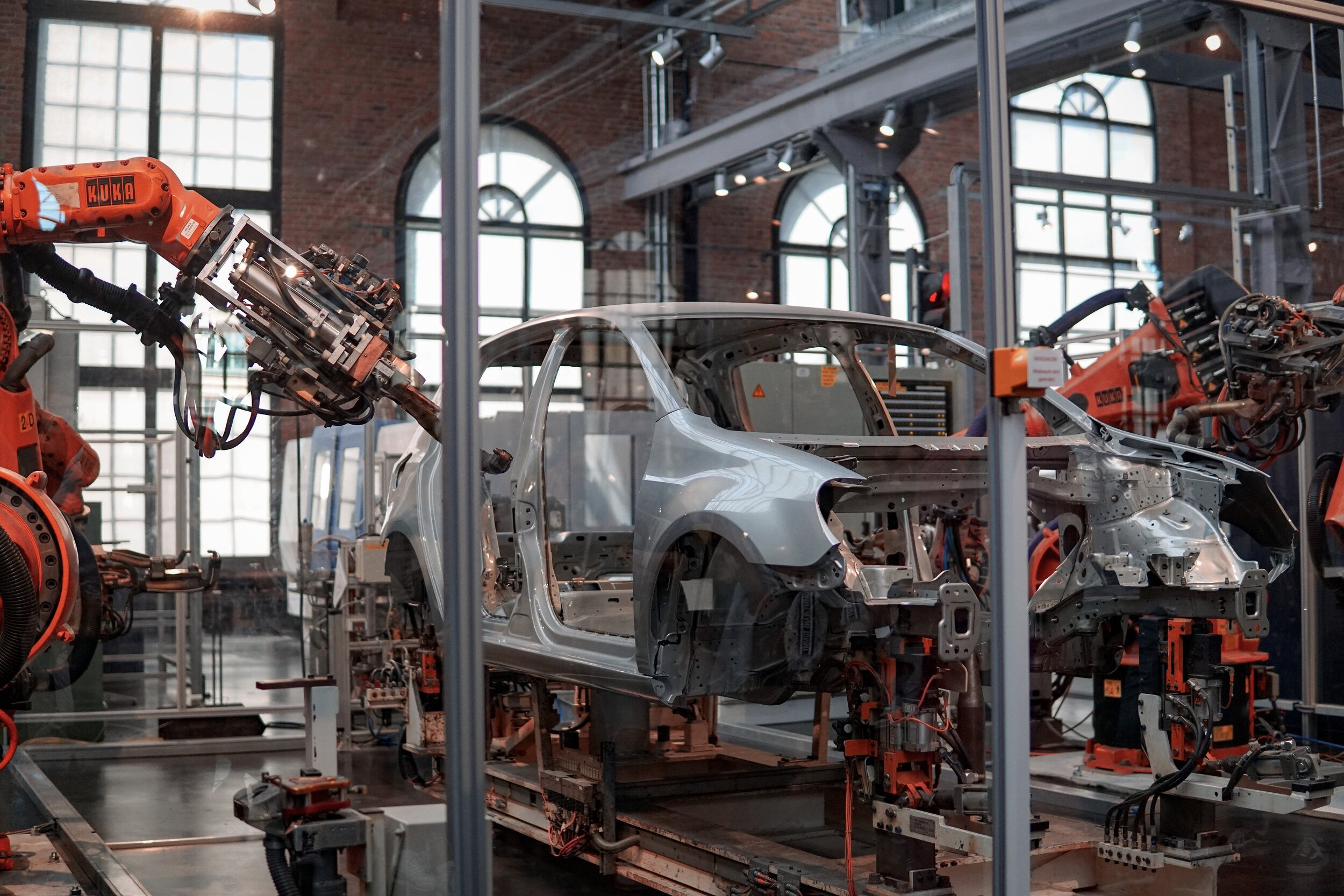
LANGUAGE OF LEAN
Genchi Genbutsu
Genchi Genbutsu encourages managers and employees to leave their desks and offices and go to the place where work is being done to see firsthand how things are working.
Genchi Gembutsu is a fundamental principle in the Lean Management system that emphasizes the importance of going to the source to observe and understand problems and opportunities. This concept was developed by Taiichi Ohno, one of the pioneers of the Toyota Production System (TPS), which is widely recognized as the precursor to Lean Management. Genchi Gembutsu is a Japanese term that translates to "go and see for yourself."
In the manufacturing industry, Genchi Gembutsu is best utilized to identify problems and opportunities in the production process. It involves visiting the production line to observe how work is being done, asking questions, and getting feedback from the workers. By going to the source, managers and leaders can see firsthand the challenges and issues that workers face on the job, and gain a deeper understanding of how the production process works.
The use of Genchi Gembutsu in the manufacturing industry is important because it allows managers to gain a comprehensive understanding of the production process, from start to finish. This includes understanding the inputs and outputs of each stage of the process, as well as the equipment and tools used. By doing so, managers can identify inefficiencies and areas where waste is being produced, and take action to eliminate these issues.
Genchi Gembutsu can also be used to identify opportunities for improvement in the production process. By observing how work is being done, managers can identify areas where work can be streamlined, and where productivity can be increased. This may involve rearranging the production line, investing in new equipment, or improving worker training and education.
One of the key benefits of Genchi Gembutsu is that it fosters a culture of continuous improvement within the organization. By encouraging managers to go to the source and observe how work is being done, organizations can identify and eliminate problems in real-time. This helps to create a more efficient and effective production process, which can lead to increased productivity and profitability.
In a nutshell, Genchi Gembutsu is a critical concept in the Lean Management system, particularly in the manufacturing industry. By going to the source to observe and understand the production process, managers can identify and eliminate inefficiencies and waste, and identify opportunities for improvement. By fostering a culture of continuous improvement, organizations can create a more efficient and effective production process, which can ultimately lead to increased productivity and profitability.
Break Through Objectives
Operational Excellence experts know the importance of establishing clear, measurable, and achievable goals in any organization.
Operational Excellence experts know the importance of establishing clear, measurable, and achievable goals in any organization. This is particularly true in the realm of Lean Management, where continuous improvement is key to success. In this context, Breakthrough Objectives play a vital role in driving progress and achieving sustainable change.
But what are Breakthrough Objectives and why are they so important? Simply put, Breakthrough Objectives are ambitious, long-term goals that aim to transform an organization and its processes. They go beyond the traditional incremental improvements that Lean Management focuses on, and aim for truly radical change. By establishing Breakthrough Objectives, organizations can focus their efforts on the most important improvements and create a clear vision for their future.
So, how can a Lean organization successfully implement and adopt Breakthrough Objectives? There are several key steps to follow:
Clarify the vision: Before setting Breakthrough Objectives, it is important to have a clear understanding of the organization’s vision and direction. This vision should align with the values and principles of Lean Management, and should be communicated clearly to all stakeholders.
Define the objectives: Once the vision is clear, it is time to define the Breakthrough Objectives. These should be specific, measurable, and achievable, and should align with the organization’s vision. It is also important to prioritize the objectives based on their importance and impact.
Engage all stakeholders: Implementing Breakthrough Objectives is a team effort, and it is crucial to engage all stakeholders in the process. This includes employees, customers, suppliers, and other key partners. By involving these stakeholders, organizations can ensure that their Breakthrough Objectives align with their needs and expectations.
Establish a clear strategy: To achieve the Breakthrough Objectives, a clear strategy must be established. This strategy should include the steps required to achieve the objectives, the resources needed, and the timeline for implementation. The strategy should also include measures for monitoring and evaluating progress.
Provide training and support: To ensure that the Breakthrough Objectives are successfully implemented, employees must be trained and supported. This may include training on Lean Management principles and practices, as well as training on new systems and processes. Employees must also be provided with the resources they need to succeed, including the right tools and equipment.
Monitor and evaluate progress: It is important to regularly monitor and evaluate progress against the Breakthrough Objectives. This helps organizations to identify areas for improvement and make adjustments as needed. By continuously monitoring and evaluating progress, organizations can ensure that they stay on track and make the necessary changes to achieve their goals.
Celebrate success: Finally, it is important to celebrate success when the Breakthrough Objectives are achieved. This helps to reinforce the importance of Lean Management principles and practices, and encourages employees to continue working towards further improvements.
In a nutshell, Breakthrough Objectives are an important tool for driving change in a Lean organization. By following these steps, organizations can successfully implement and adopt Breakthrough Objectives, and achieve truly transformative results. With a clear vision, a solid strategy, and a commitment to continuous improvement, organizations can achieve their goals and achieve Operational Excellence.
One Point Lesson
One Point Lesson (OPL) is a method used in the manufacturing industry that can greatly improve operational efficiency and overall quality.
One Point Lesson (OPL) is a method used in the manufacturing industry that can greatly improve operational efficiency and overall quality. This method is often used within the context of Lean Management, which is a strategy that focuses on maximizing value while minimizing waste. As a Lean Management Expert, I will be discussing how OPL can be used to improve operations in the manufacturing industry.
OPL is a simple but effective tool that helps to standardize and spread best practices across an organization. It is a one-page document that summarizes a lesson learned from a problem or improvement opportunity. This document is designed to be easy to understand and share, so that others can learn from the lesson and apply it in their own work. The purpose of OPL is to promote continuous improvement by capturing and sharing knowledge that can be used to prevent similar problems from happening again in the future.
One of the key benefits of using OPL is that it allows for quick and easy dissemination of knowledge and best practices. The one-page format makes it easy for employees to understand and remember the information, and the lessons learned can be quickly spread throughout the organization. This can lead to significant improvements in the quality of products and services, as well as increased efficiency in operations.
OPL can also help organizations to identify and eliminate non-value-adding activities. This is because the lessons learned can be used to identify areas where improvements can be made, and then the appropriate changes can be implemented. For example, if a problem occurs during the production process, an OPL can be created to document the cause of the problem and how it was resolved. This information can then be used to make changes that will prevent the problem from happening again in the future.
In addition to improving quality and efficiency, OPL can also help organizations to foster a culture of continuous improvement. By capturing and sharing knowledge, employees are encouraged to look for ways to improve processes and to find solutions to problems. This leads to a more engaged workforce, as employees feel that their ideas and contributions are valued.
In order to successfully implement OPL in the manufacturing industry, there are a few key steps that organizations should follow. Firstly, it is important to have a clear understanding of what information should be included in each OPL. This includes the problem or opportunity that was identified, the cause of the problem, the solution that was implemented, and the results of the solution.
Secondly, organizations should develop a system for sharing OPLs throughout the organization. This could be done through regular meetings, email, or an online platform. The key is to make sure that the information is easily accessible and can be quickly shared with others.
Finally, organizations should ensure that they have the resources in place to support the implementation of OPL. This includes providing training to employees on how to create and use OPLs, as well as having dedicated staff to manage the process.
In a nutshell, One Point Lesson (OPL) is a powerful tool that can help organizations in the manufacturing industry to improve quality, efficiency, and overall operations. By standardizing and spreading best practices, organizations can foster a culture of continuous improvement and identify and eliminate non-value-adding activities. To successfully implement OPL, organizations should follow a few key steps, including having a clear understanding of what information should be included in each OPL, developing a system for sharing OPLs, and ensuring that they have the resources in place to support the implementation.
Cell Production
Cell Production focuses on optimizing the flow of work and improving efficiency in manufacturing and operations.
Cell Production focuses on optimizing the flow of work and improving efficiency in manufacturing and operations. It is based on the concept of organizing work into cells, which are self-contained units responsible for performing a specific set of tasks. The goal of cell production is to minimize waste, increase flexibility, and improve overall performance.
The origins of cell production can be traced back to the 1950s and 60s, when Toyota and other Japanese companies were experimenting with new approaches to manufacturing. Over time, the concept of cell production has evolved and been refined, and today it is widely used in a variety of industries, including automotive, electronics, and consumer goods.
In order to implement cell production effectively, there are several key steps that organizations must take. Firstly, it is important to conduct a thorough analysis of the current state of the manufacturing or operations process, in order to identify areas where improvements can be made. This may involve mapping out the flow of work and identifying bottlenecks or other inefficiencies.
Once these areas have been identified, the next step is to reorganize the work into cells, taking into account the specific requirements of each cell and the skills and expertise of the employees who will be working in them. This may involve rearranging physical work spaces, or changing the way that work is assigned and managed.
It is also important to establish clear communication and feedback mechanisms, so that employees and teams can work together effectively. This may involve setting up regular meetings to discuss performance, or implementing systems for tracking and reporting on key metrics.
In order to ensure a successful implementation of cell production, it is also important to provide training and support for employees. This may involve providing training on the new processes and procedures, or offering coaching and mentoring to help employees develop the skills and knowledge they need to be effective.
Another key aspect of cell production is continuous improvement. This involves regularly reviewing performance and making adjustments as needed, in order to optimize efficiency and reduce waste. This may involve experimenting with different approaches, such as implementing new technologies or streamlining processes, in order to find the best solutions.
In conclusion, cell production is a powerful methodology for optimizing performance in operations and manufacturing. By reorganizing work into cells, minimizing waste, and continuously improving performance, organizations can increase efficiency, reduce costs, and improve overall performance. In order to be successful, organizations must take a structured and systematic approach, and be committed to ongoing improvement.
TPM - Total Productive Maintenance
Total Productive Maintenance (TPM) is a maintenance strategy that involves involving all employees in the maintenance process to maximize equipment productivity and minimize downtime.
Total Productive Maintenance (TPM) is a methodology that originated in Japan in the 1970s and has since become a widely recognized and adopted approach to operational excellence in manufacturing and other operations-focused industries. It is a comprehensive approach that seeks to optimize the performance of equipment and processes through a focus on maintaining and improving reliability and efficiency.
The origins of TPM can be traced back to the Japanese auto industry, where manufacturers were seeking ways to increase productivity and competitiveness in the face of increasing global competition. TPM emerged as a response to the need for a more proactive and integrated approach to equipment maintenance, with the goal of improving both productivity and overall equipment effectiveness (OEE).
Over time, TPM has evolved and expanded to encompass a wider range of objectives and activities. Today, it is widely regarded as a best-practice approach to operational excellence, and is widely used in many different industries, including manufacturing, healthcare, and government operations.
One of the key features of TPM is its focus on involving all employees in the maintenance and improvement process. This is achieved through the creation of cross-functional teams and the use of a range of techniques, including root cause analysis, standardization, and continuous improvement.
Another key aspect of TPM is its focus on data-driven decision-making and performance measurement. This involves the collection and analysis of data on equipment and process performance, which is then used to identify areas for improvement and to drive continuous improvement efforts.
When properly implemented, TPM can have a significant impact on organizational performance and competitiveness. This can include improvements in equipment reliability, increased productivity, reduced waste, and improved overall equipment effectiveness (OEE).
To achieve these benefits, it is important to implement TPM in a structured and systematic way, with clear goals and objectives and a strong focus on continuous improvement. This typically involves a multi-phased approach, starting with an assessment of existing processes and equipment, followed by the development of a comprehensive improvement plan and the implementation of specific improvement initiatives.
In a nutshell, TPM is a proven methodology that can help organizations achieve operational excellence by optimizing the performance of their equipment and processes. To achieve success, organizations must approach TPM in a systematic and structured way, with clear goals and objectives, and a strong focus on continuous improvement.
Key points for a successful TPM implementation:
Involve all employees in the process
Focus on data-driven decision-making
Adopt a multi-phased approach
Prioritize continuous improvement
Develop a comprehensive improvement plan.
Stay Connected
Ad
We want information fast and in a nutshell. We from OI recommend Blinkist* - because it’s simply the best.
* = Affiliate Link