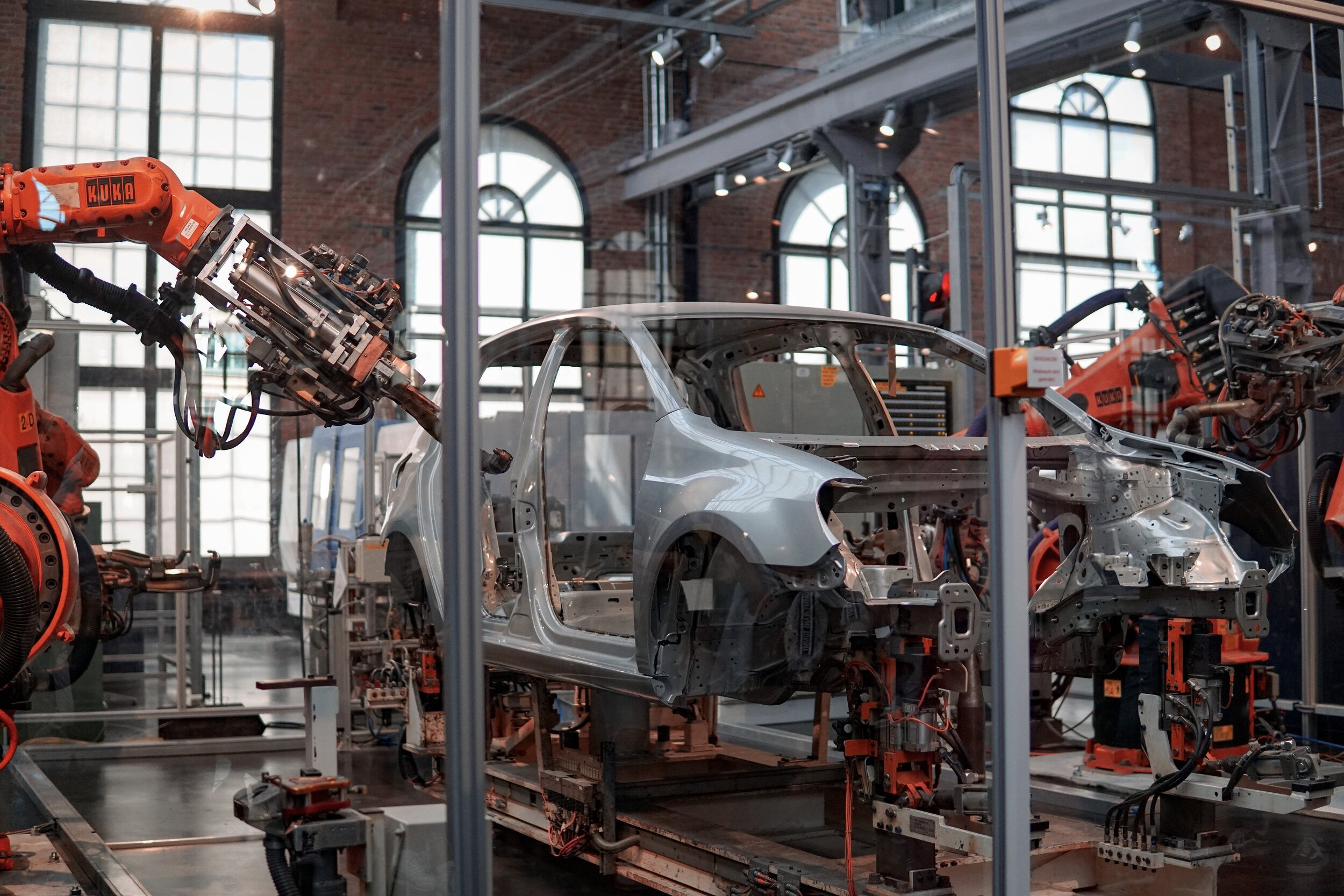
LANGUAGE OF LEAN
Ringi Seido
The Ringi Seido methodology that originates from Japan is widely recognized as an effective method for achieving operational excellence in decision making.
The Ringi Seido methodology that originates from Japan is widely recognized as an effective method for achieving operational excellence. As an operational excellence expert, I can attest the benefits of implementing Ringi Seido in your organization.
Ringi Seido, which translates to "approval process," is a consensus-based decision-making system that involves different levels of an organization in the decision-making process. It is considered an essential element of Japanese business culture and has been widely adopted by Japanese companies for decades.
One of the key principles of Ringi Seido is involving all relevant stakeholders in the decision-making process. This includes front-line employees, middle management, and executives, allowing for a comprehensive and well-rounded approach to decision-making. The goal is to gain buy-in from all levels of the organization and ensure everyone is aligned with the company's vision and direction.
The Ringi Seido process begins with a proposal for a change or new initiative, which is then shared and discussed among the relevant stakeholders. Through a series of meetings and discussions, the proposal is refined and modified until it has the support of all relevant stakeholders.
One of the key benefits of the Ringi Seido process is that it ensures all necessary information is considered before a decision is made. This helps to reduce the risk of making decisions that are not in the best interests of the organization. Additionally, the process provides the opportunity for employees to voice their opinions and share their ideas, which can lead to the discovery of new and better ways of doing things.
Another benefit of Ringi Seido is that it promotes a culture of continuous improvement. The process encourages employees to regularly review and evaluate the implementation of the approved initiatives, which allows for the identification of areas that need improvement. This leads to a continuous cycle of improvement, as the organization continuously refines its processes and procedures to achieve better results.
One of the challenges of implementing Ringi Seido is that it can be time-consuming and require significant investment in training and development opportunities for employees. However, the benefits of the methodology make it a worthwhile investment, as it can lead to significant improvements in the efficiency and effectiveness of an organization's operations.
For organizations that are interested in implementing Ringi Seido, it is essential to have a clear understanding of the methodology and the specific steps involved in the approval process. This requires the participation of all relevant stakeholders and a commitment from the organization to provide the necessary resources, including training and development opportunities, to ensure the successful implementation of the methodology.
In a nutshell, I highly recommend the implementation of Ringi Seido for organizations looking to achieve operational excellence. While it may require a significant investment in time and resources, the benefits of the methodology make it a powerful tool for achieving better results. By involving all relevant stakeholders in the decision-making process, organizations can gain buy-in from all levels of the organization and ensure everyone is aligned with the company's vision and direction. This leads to a culture of continuous improvement, which is essential for achieving long-term success.
Value Creation
What the customer is willing to pay for.
The exact opposite of waste is value creation. That is what you aim for with all lean activities. Value creation are all activities that create or add value to your service or product and the customers are willing to pay for. When a service or product has been perceived or appraised to fulfill a customer need or desire as defined, the product or service may be said to have value or worth. Components of value may include quality, utility, functionality, capacity, aesthetics, timeliness or availability, price, etc.
Ergonomic Workplace
A work place that takes into consideration most of the ergonomic aspects such as the operator’s height, range and reach.
An ergonomic workplace is a work system that considers the ergonomic aspects of an operation and the operator such as the operator’s hight, range and reach with the goal that the operator does not need to bend or turn.
The ergonomic workplace goes hand in hand with the work improvement.
Definition and purpose
Reveal waste increasing cost and not adding value.
Find waste in the movement of workers, eliminate/improve, pursue net work adding value.
Worker Movement
Lean Manufacturing and Ergonomics may have different roots and directions but together they can complement each other and define a more efficient and safer workplace.
One of the best person known for focusing on productivity and efficiency in manufacturing processes was Henry Ford with the invention of the modern assembly line. Ford really was focusing on eliminating waste and to cut down unnecessary costs in relation to the manufacturing of his cars.
Toyota is one of the best known companies that has stretched to the maximum the idea of Lean Manufacturing and is now holding the pole position when it comes to the reputation according the elimination of “waste”.
By looking at the Lean Model as well as Work Ergonomics, you clearly see the necessity of both practices in the industrial workplace, as well as observe that both can complement each other.
The 7 types of waste to eliminate include:
Transport
Inventory
Motion/Movement
Waiting
Overproduction
Overprocessing
Defects
The list of TIMWOOD is what Toyota has defined as the seven major types of wastes or non-value-adding activities. The seven wastes do not add any value to the product and the customer in the end is not willing to pay for it. Therefore it is essential to remove as much waste as possible which will have also an effect on the ergonomic workplace and furthermore on the health of the operators.
Some of these things like transport, waiting or unnecessary movement can be reduced to a limit what the operator still needs because as human being the operator is limited by his body.
The Lean Manufacturing initiatives and workplace ergonomics stepped into the manufacturing world at different times and therefore are not fully integrated. But you are perfectly advised by combining the principles of Workplace Ergonomics with Lean Manufacturing initiatives. Through a cooperative assessment and teamwork you have the chance to complement each other in making the workplace more efficient and a safer place.
Heijunka
How to level production with the help of Heijunka.
Heijunka is a tool in the lean world that is striving for a leveled and smoothed dispatching of manufacturing demands which therefore leads to a reduction of waste. The meaning of levelling is to transform irregular incoming orders into uniform production batches. The target is to bring all demands on the smallest batch size possible based on a leveled production pattern. The Heijunka Board visualizes the predefined production plan for the production process. The beauty of it is that it enables you with little effort of control to implement a steady and synchronous flow of production.
If you are in a leading manufacturing position you already know how painful it can be to maintain a steady flow of work.
Customer demands are typically not perfectly leveled and this fluctuation needs to be translated into a defined takt that is given by your production process. To keep up with the incoming stream of orders and to avoid overproduction and therefore tied up cash, Heijunka can help you lowering the peaks and smoothing out production.
Heijunka is a well-known lean method for smoothing and reduce the over stressing of a production process. Heijunka is Japanese and means roughly translated levelling. The main reason for implementing Heijunka is a faster reaction time on fluctuating demands and improving the utilization of installed capacity.
With the help of Heijunka you minimize the sizes of batches to smallest size possible and start processing customer orders based on demand. This will support you on reducing your inventory as you will stop producing based on utilization of line capacity and then pile up finished goods without being sold.
At the bottom, Heijunka allows you to produce and deliver value to your customer at a steady pace and gives you the chance to react faster on deviations, while not overstressing the process. Therefore this method gives you always two options for levelling your production: By type or by quantity.
Balancing by type:
Go through your portfolio and define the average demand of each product. Based on the average demand the production is smoothed out to meet it. The target is to level the capacity of our line. Use Heijunka to keep up with the demands of each product of your portfolio and use it to visualize the production plan.
Balancing by quantity:
The main road blocker to establish a smooth and continuous production flow is producing in batches. The target is clear: produce only what is ordered. Therefore, Heijunka enables you to level your production by the average volume you get. By levelling your production this way, you will be able to achieve all demand by the end of the week. With the help of Heijunka you will keep your processes running without overburden it when unplanned peaks are coming in.
The Heijunka Box is a tool implemented on the shop floor in order to visualize the workload that needs to be fulfilled in order to meet the average demand. Simply spoken it has cards spread over the week for each product in a logical sequence to reach optimal flow.
The Heijunka Board
Usually the Heijunka box is set up in a matrix with the first column separated by product type for each line, the following columns are the workdays of the week. Therefore your Matrix defines Product type and the quantity that needs to be produced on a specific day. Two ways are most common, either as boxes where cards are placed in or as a board with magnetic cards that stick on it.
Depending on your installed capacity and the team size you want to cover with Heijunka you might need multiple Heijunka boards. Typically the cards you use are having the format of Kanban cards, that are following the process of the processed good until the end and then are placed back to the collection box for new planning.
Heijunka is a great lean method that allows you to organize your workflow around average customer demand. You protect your processes and employees from over stressing due to uneven production and quantity sizes. Furthermore, it supports you on realizing a complete pull system throughout production.
Stay Connected
Ad
We want information fast and in a nutshell. We from OI recommend Blinkist* - because it’s simply the best.
* = Affiliate Link