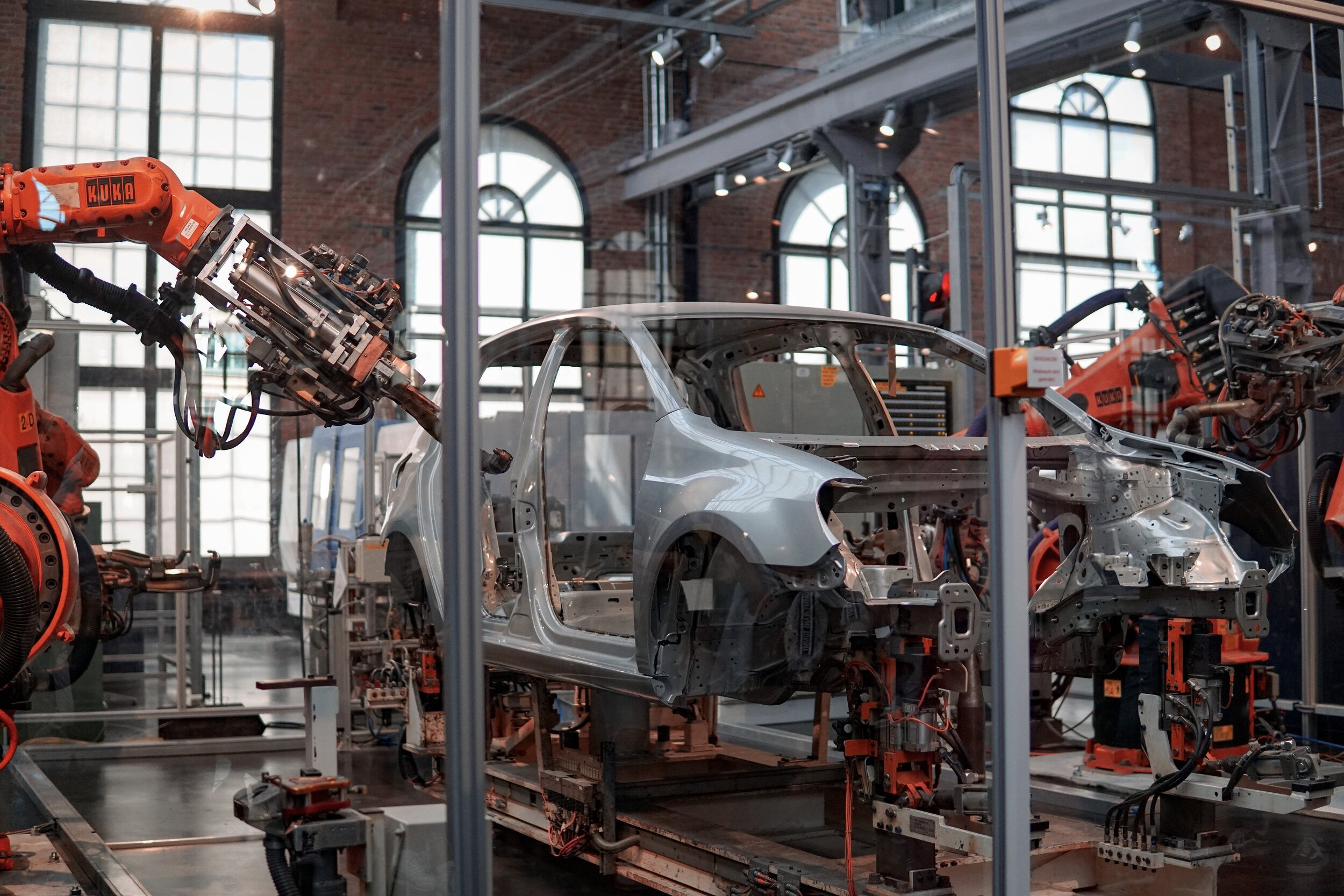
LANGUAGE OF LEAN
Shojinka
Constantly improving the amount of workers in a production cell to match the volume of demand and type which has been given to the unit - requires that training is provided to every worker in various process steps.
Constantly improving the amount of workers in a production cell to match the volume of demand and type which has been given to the unit requires that training is provided to every worker in various process steps. The layout of the work cell is done in a circular or U-shaped layout, where the number of operators performing can vary and be adjusted. The capacity and ability to have an adjustable manufacturing process is relevant to meet the demand profile and have a sustainable growth.
Ever thought if there was a particular way through which you can use less manpower but produce more? Needless to say, there is a way through which you can do this: Maximizing the output while simultaneously minimizing the input is a business 101 idea and theory that we carry with us since inception, and strive hard to completely tackle for the whole of our careers.
There certainly is a way through where you can do more with less, and that way is known as Shojinka. It is also referred to as "flexible staffing" or "flexible manufacturing." Shojinka is again a Japanese term, and it was born from the lean manufacturing principles of Toyota. There is no denying that the idea of "flexible staffing" has proven to be the best performer in lean theory.
So what can be understood as Shojinka
Primarily, Shojinka is defined by two elements. The first one is the operators are trained on several workstations and following a qualification matrix. The second one is the layout for the work cell, of cause preferable in a U-Shape layout rather than a straight old fashioned line, but this has to be discussed in all cases separately.
Let’S have a look on the Pros and Cons of Shojinka
Pros
Flexible staffing, as its name suggests, has the biggest advantage in that the staff is flexible. This means that the operators have been provided with training in almost every part of the production following the qualification matrix.
This will enable them to work in areas of production where there is more demand or will allow them to switch quickly as the demand changes. Unlike a highly specialized working environment or fixed linear manufacturing, flexible staffing allows you to keep your efficiency high under every type of manufacturing demand, rather than an ideal pre-determined set. In addition to this, Shojinka also provides an opportunity for operators to work on improving products or on the various side whenever the demand falls all across the board. It will not only enable your staff or the operators to become more effective and efficient at changing levels of demand, but it will also allow them to swap between these specific levels on a shop floor that has been properly and correctly set up.
The inputs and the final outcomes are kept on the identical and corresponding sides of the work cell due to the U-shaped manufacturing line, which ultimately helps your organization of logistics and transportation. Furthermore, it also enables the operators to move conveniently between the first process step and the final process step on an assembly line without the need to walk its whole or complete length.
Cons
As soon as it has been implemented and applied, there are almost no cons to the Shojinka assembly line.
But to start off implementing flexible staffing you need to clear of some major obstacles to get started. If not already implement you have to install a training matrix and train your operators accordingly, to get them qualified to handle all aspects of your operation. Undoubtedly, it may require you to make some investment upfront.
Simultaneously with the training of your operators you will need to standardize every process step in your production. By doing so you will reduce the amount of training and therefore qualification needed in order to fulfill the requirements for the single process steps, as they are broken down to the simplest operation.
Clear and simple “Standard Operation Instructions“ (SOI) will be required to explain the operation and guide operators through the qualification and later performing the process step. By this due to variation of operators in a assembly cell they can get fast into new work requirements. In addition the supervisor can always react faster as the standard process is always described and if deviation occurs the cause is faster detected and eliminated.
So the cons can be wrapped up as investments upfront. Paying all of the expenses at the initial stages for the purpose of integrating and incorporating Shojinka will prove to be worthwhile in the end. There is no denying that your workforce will ultimately become significantly streamlined and that Takt Time of goods will be flexible to the max.
Production Diary
The production diary, as part of the shop floor management system, defines a shift based weekly forecast incl. upcoming tasks for mgmt., supporting functions and is openly displayed on the shop floor.
With the help of a production diary, based on a pre-defined shift planning all other functions and outcomes are planned and tracked. This includes the mgmt. team as well as all supporting functions. In order that everyone is aware about the upcoming week the production diary is openly displayed on the shop floor. With the production diary and the pre-set structure of daily meetings of the shop floor mgmt. all daily activities are carried out. Best known part is e.g. Gemba Walks and the included problem solving activities e.g. A3 or just confirming that all processes run as planned.
With this big part of shop floor mgmt. it is clear that all regular meetings planned along the production diary are set. All other unplanned activities or extra meetings need to be conducted respecting the fixed schedule of the production diary.
5 Why
The 5 Why methodology is a well known part of the root cause analysis. Key is to ask five times in the row – why?
The 5 Why methodology is a well known part of the root cause analysis. Key is to ask five times in the row – why? It is not the only way to determine the root cause(s) of problems. Just to mention that it usually comes together with an ISHIKAWA analysis. If you want to get deeper into problem solving including ISHIKAWA and 5Why we recommend you the article taking on the 7Steps approach.
The practice of asking why five times in a row whenever a problem occurs supports you on identifying root cause(s) and to determine effective counter measures that are developed through the process of 5Why. Then it is a simple part of PDCA to develop and implement effective measures.
To be able to steer a wide product portfolio, survive the competitive pressure and at the same time satisfying your customers with a high quality product at a reasonable price can be a tough game. Most of the time you don’t have enough time to run the complete product development cycle, do your validation and verification… The end of the story is that you start production because you need to deliver – which automatically leads to mistakes in running daily business. Therefore, the simple method of 5Why can be used to support, not only, your quality department to get faster to the bottom of problems.
The solution for a problem is not always easy, sometimes the root cause is hidden. Therefore the method is an important element of the root cause analysis. One tries to get to the root of the problem step by step with why questions, because one assumes that several causal connections interlock. The system is easy to explain, but there is a lot behind it. If you really take the time to ask the questions carefully and discuss them, the results are extremely profitable.
You should go through these steps of the 5-Why method. Describe your problem as detailed as possible. As more facts you have, you are faster on getting to the bottom of the problem.
What is the difficulty?
When did it first occur?
How often does it occur?
Is this failure randomly coming or reoccurring in a pattern?
Can you repeat the failure?
What is the effect of this failure?
and so on….
It is very important to get a fast idea of the situation on site. Take the Gemba Walk as great opportunity to talk to the people who are actually involved and to see it with your own eyes instead of guessing from your office.
Avoid making assumptions at this stage - you may draw the wrong conclusions.
Keep calm and try to understand the complete context first.
Understanding the context is where the 5-Why method comes in. Gradually ask why questions in order to get a feeling for the interrelationship of effects. This works for many areas of the company, in production, but also in your private life.
Example:
Problem: I miss all the fun part with my kids…
Why do I miss so much? - Because I’m not often at home.
Why am I not often at home? - Because of my position at work I have long working hours and business trips.
Why do I have long working hours and business trips? Because I can’t get my work done in 8 hours and bad in delegating work.
Why can I get my shit done in 8 hours and miss to delegate things? Because I’m sloppy in prioritizing and time management and don’t trust others.
Why can’t I prioritize my activities and don’t trust others? Because I don’t have the information needed to do so.
Reverse conclusion: If I’m not getting the necessary information in a certain amount of time in an acceptable quality I’m not able to steer my employees but also miss the time with my kids.
Sometimes 2 questions are necessary, sometimes 8 or even more to bring you to the “right” conclusion. But don’t give up half way.
Develop appropriate counter measures:
What contributes to solve the problem and who can implement which measures? How long will this take and what consequences will the implementation have?
First: I should try to have set timeframes with my kids which are holy and untouchable.
Second: I should define what information for me is necessary to run my company.
Third: According to the defined Information I train my employees what I need.
Fourth: I implement a clear systematic approach that I have all information latest at 11:00.
(DING DONG - Sounds familiar? BINGO — Shop Floor Management with a functioning meeting cascade.)
Keep the wheel spinning!
No matter what – before start implementing ad-hoc whatever you find best – take your time to identify what actions contribute to a real long term effect, what effects it will have on other areas, etc. Nothing worse than if you think you are doing something great but in reality you make it even worse.
The cycle of questions is often interrupted too early. The real cause is then not really eliminated and after some time there are repeated difficulties.
You can test it: If the reverse of your assumptions works, you are probably at the end of the causal chain.
As mentioned in the beginning another way is the ISHIKAWA diagram
Just keep in mind that not like with the ISHIKAWA the 5 Why only leads you to one cause for a problem. But as always in life there can be more than just one that leads to an effect. Therefore, the combination of 5Why and ISHIKAWA gives you the best approach to determine causes. It will allow you to represent several major and minor causes that can contribute to the solution.
Get the big picture with an ISHIKAWA drill it down with the 5Why.
Stay Connected
Ad
We want information fast and in a nutshell. We from OI recommend Blinkist* - because it’s simply the best.
* = Affiliate Link