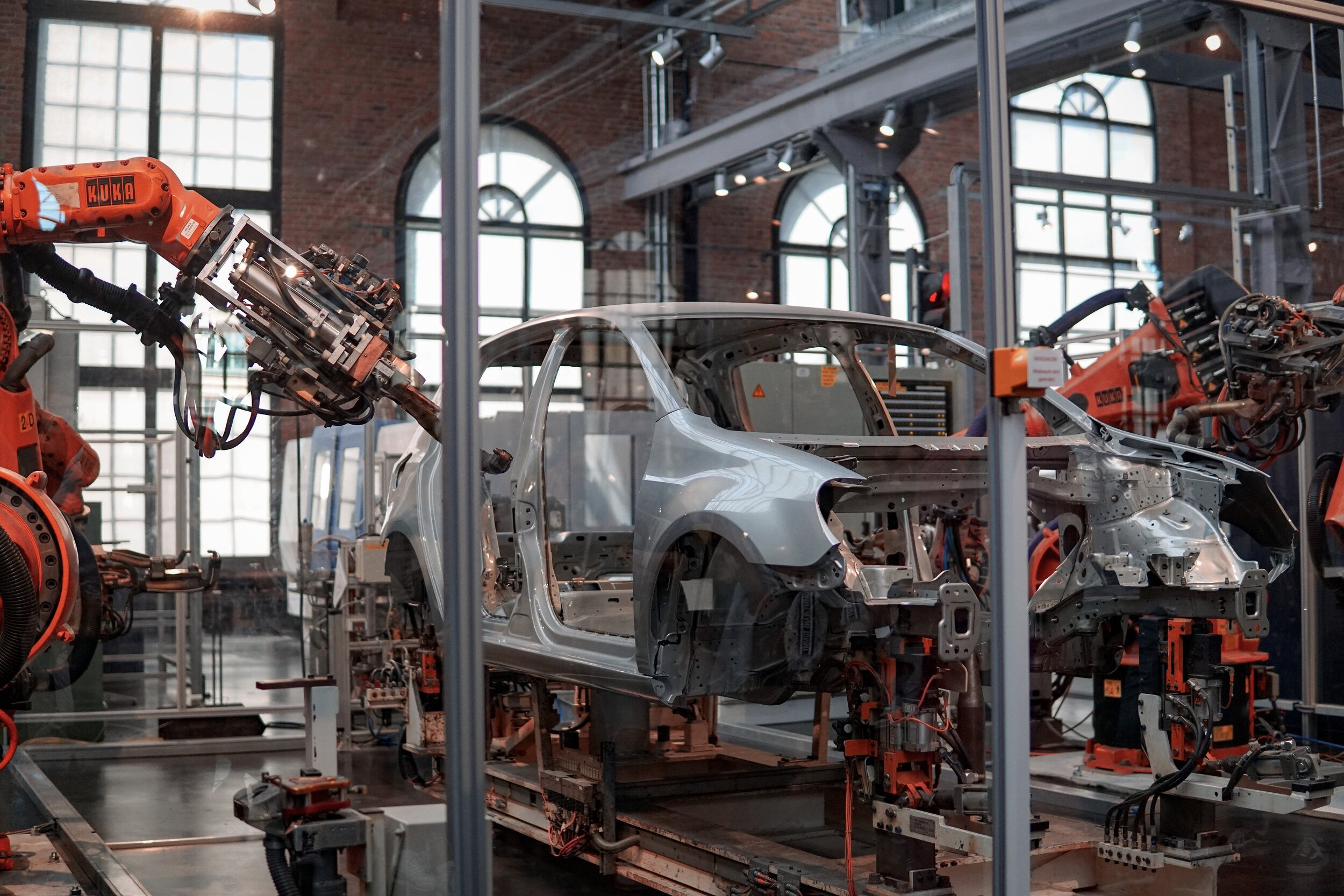
LANGUAGE OF LEAN
Doctor Nurse Principle
The operator creating the value (doctor) receives the materials and tools from the logistics provider (nurse), so that his/her primary activity is not interrupted by secondary activities.
In the Doctor Nurse principle, the operator creating value is considered as the doctor, he receives tools and goods he needs to do his job from the nurse in this case logistics. For this reason, the doctor can’t do his job without the support of the nurse.
What can we learn from hospitals and how can we adapt it to the lean world.
In hospitals it is crucial that the doctor can fully concentrate on a surgery, the doctor is the single point of contact towards the patient using his tools combined with his training. Everything distracting him from being focused has to be eliminated. In order to give him this capability he needs assistant right next to him. The nurse’s job is to support the doctor and provide him with all equipment, tools and material he needs just in time.
Applying this principle to production is not that hard. To use the doctor nurse principle on the shop floor some requirements have to be met. As mentioned think about the operators as the doctor, they have to concentrate on production. As they are the once generating value for the whole organization by assembling the components which customer are willing to pay for – they need to be placed in the center of all activities – the rest is supportive.
In lean manufacturing this is called the line-back approach. Primary processes are the once that add value so focus on the operation and prepare everything that supports it. The nurse takes care of all other activities, most of the time non-value adding activities but necessary.
Doctor Nurse Principle
Arrange the work station in a way that gives the nurse free accessibility to the work area without disturbing the doctor, i.e. filling up kanban shelfs with new material while simultaneously removing empty boxes.
With the approach of separation of primary and secondary processes in two physical areas none of the process will be interrupted by the other.
In addition, this principle is driving the mindset of the organization to focus on a lean production process and how best it can be supported. If you do so, you will also have the advantage by separating value-adding and non-value-adding activities to find you approaches to minimize the non-value adding activities.
Another way of calling the nurse a nurse is a water spider or in lean terms a Mizusumashi – the inbound material supplier.
Shojinka
Constantly improving the amount of workers in a production cell to match the volume of demand and type which has been given to the unit - requires that training is provided to every worker in various process steps.
Constantly improving the amount of workers in a production cell to match the volume of demand and type which has been given to the unit requires that training is provided to every worker in various process steps. The layout of the work cell is done in a circular or U-shaped layout, where the number of operators performing can vary and be adjusted. The capacity and ability to have an adjustable manufacturing process is relevant to meet the demand profile and have a sustainable growth.
Ever thought if there was a particular way through which you can use less manpower but produce more? Needless to say, there is a way through which you can do this: Maximizing the output while simultaneously minimizing the input is a business 101 idea and theory that we carry with us since inception, and strive hard to completely tackle for the whole of our careers.
There certainly is a way through where you can do more with less, and that way is known as Shojinka. It is also referred to as "flexible staffing" or "flexible manufacturing." Shojinka is again a Japanese term, and it was born from the lean manufacturing principles of Toyota. There is no denying that the idea of "flexible staffing" has proven to be the best performer in lean theory.
So what can be understood as Shojinka
Primarily, Shojinka is defined by two elements. The first one is the operators are trained on several workstations and following a qualification matrix. The second one is the layout for the work cell, of cause preferable in a U-Shape layout rather than a straight old fashioned line, but this has to be discussed in all cases separately.
Let’S have a look on the Pros and Cons of Shojinka
Pros
Flexible staffing, as its name suggests, has the biggest advantage in that the staff is flexible. This means that the operators have been provided with training in almost every part of the production following the qualification matrix.
This will enable them to work in areas of production where there is more demand or will allow them to switch quickly as the demand changes. Unlike a highly specialized working environment or fixed linear manufacturing, flexible staffing allows you to keep your efficiency high under every type of manufacturing demand, rather than an ideal pre-determined set. In addition to this, Shojinka also provides an opportunity for operators to work on improving products or on the various side whenever the demand falls all across the board. It will not only enable your staff or the operators to become more effective and efficient at changing levels of demand, but it will also allow them to swap between these specific levels on a shop floor that has been properly and correctly set up.
The inputs and the final outcomes are kept on the identical and corresponding sides of the work cell due to the U-shaped manufacturing line, which ultimately helps your organization of logistics and transportation. Furthermore, it also enables the operators to move conveniently between the first process step and the final process step on an assembly line without the need to walk its whole or complete length.
Cons
As soon as it has been implemented and applied, there are almost no cons to the Shojinka assembly line.
But to start off implementing flexible staffing you need to clear of some major obstacles to get started. If not already implement you have to install a training matrix and train your operators accordingly, to get them qualified to handle all aspects of your operation. Undoubtedly, it may require you to make some investment upfront.
Simultaneously with the training of your operators you will need to standardize every process step in your production. By doing so you will reduce the amount of training and therefore qualification needed in order to fulfill the requirements for the single process steps, as they are broken down to the simplest operation.
Clear and simple “Standard Operation Instructions“ (SOI) will be required to explain the operation and guide operators through the qualification and later performing the process step. By this due to variation of operators in a assembly cell they can get fast into new work requirements. In addition the supervisor can always react faster as the standard process is always described and if deviation occurs the cause is faster detected and eliminated.
So the cons can be wrapped up as investments upfront. Paying all of the expenses at the initial stages for the purpose of integrating and incorporating Shojinka will prove to be worthwhile in the end. There is no denying that your workforce will ultimately become significantly streamlined and that Takt Time of goods will be flexible to the max.
Kamishibai Board
The Kamishibai Board helps your organization to visualize and manage recurring tasks in a very simple but effective way.
The Kamishibai Board is part of the visual management in Lean Management that supports you on managing recurring tasks in a way that the status of each task is clearly recognizable by everyone in your organization.
The tasks are listed by their frequency and the responsible persons. The design of the cards can vary, but typically T-Cards are used as the handling is quite easy. These cards contain on both sides the information of each task. One side of the card is red the other one green. RED: to do, GREEN: done. So the color is indicating the status of each task.
By using these two color coded cards everybody in the organization will recognize if all activities are on track or if there is a backlog ahead on performing daily, weekly or monthly activities.
Example Kamishibai Board - weekly tasks with assigned persons
Kamishibai is a Japanese term, to bring it in operations terms it can be understood as mini-audits. The Kamishibai is a great starting point for Gemba Walks mainly in the admin area of your organization but can also be utilized in the service and maintenance department. It also supports 5S activities and assists in checking the continuous improvement actions on checking on standards and improvements during regular meet ups.
The Kamishibai approach has different sections. E.g. a simple planning board with T-cards with a red and a green side, a list of person in charge and a 3C list. The 3C list thereby describes the Concern, defines the Cause and lists the Countermeasures, find a free template (in flip chart format) here.
The planning section has the tasks tank, on the far left side all tasks are stored in holders (T-Cards) or e.g. magnetic cards that are also green on the one and red on the other side. One section further to the right you can implement a matrix with responsible person for each row and all weekdays as column. By this you can easily assign tasks.
Between the organizational and the problem solving part there should be space for the escalation or support needed tasks. It might happen that an assignee is not able to fulfill a task as he/she is in the need of information or active support from a different level or department.
To sum it up. The benefits of the Kamishibai methodology is mainly the visualization part. It gives clear structure and is understandable at first sight. With the Kamishibai you are able to perform so called “mini-audits” on a regular basis that helps you driving the continuous improvement process in your organization and supports you on performing effective Gemba Walks. Instead of heaving some chit chats you can bring information straight to the point and address any issues fast.
You can use the Kamishibai methodology for all kinds of work areas in your organization, e.g. you have control indicators for methods, processes, documents, standards and much more. In the end the Kamishibai helps you to keep the routine of defined standard work procedures as results of KAIZEN activities. If it works congrats, if not congrats - you found something that can be improved.
Makigami
With the help of a Makigami - administrative processes are recorded and redesigned.
The Japanese term Makigami is developed out of two. First the MAKI (yeah like the Sushi) meaning roll or rolled and KAMI meaning paper. Before you go wild, in the word combination you write kami with “g”. So the question that rises is: What you do with a rolled paper? You use the Makigami to draw and redesign administrative processes. Like with all Lean or Opex activities, once the process is visualized with the help of a Makigami “value-adding” and “non-value adding” activities are marked. On the bottom of the Makigami you will find a time axis which shows the operating time and the pure value adding time.
With the help of the Makigami process analysis, the process is always viewed from the perspective of the process itself, never from the perspective of the employees. This has to be clear also for the waste attack activities in the process. With the Mantra of OPEX: the central question that must be brutaly honest answered: Is the customer willing to pay for this process step/activity? Is this what you are doing adding value to the final product or service?
After you recorded the current state of your process you start to redesign it by asking yourself permanent the following question:
What should the ideal process look like?
Take your planned future development and corporate vision into account to make sure you are not running in the wrong direction.
Andon
Andon is a crucial part of visual management on the shop floor that gives a signal that indicates if and where there is a problem.
Andon is a crucial part for the visual management on the shop floor that gives a signal that indicates if and where there is a problem. Typically indicated with a traffic light signal red = failure mode, yellow = non-conforming performance and green = normal operation mode.
The methodology of Andon as part of the shop floor management, is to show the current operating status of a machine or a production line in a way that everyone can see and understand it immediately. As typically in Lean Terms Andon comes from the Japanese language and means paper lamp or just lamp.
Going along the Andon-Systematic there is to mention the Andon-Cords. The cords are used by operators to activate the lamps by either tear the cord or more likely nowadays pressing the corresponding buttons, which are attached above the production line and are easily accessible for the operators hanging downwards or as button attached at the work station.
If a non-conforming condition occurs, the yellow Andon signal initiates the support so that the problem that has occurred can be remedied immediately with additional supportive functions, such as maintenance. In worst case it is also possible to stop the complete production (red signal) until the problem has been solved or at least suitable countermeasures are in place.
An Andon has three main functions:
Visualization of the operating status of a machine/assembly line
Possibility for the operator to report an non-conforming condition and escalate it using a defined escalation process
Production or belt stop, so that no non-conforming products or components are passed on to the next process step
Old fashion Andon Board
The clear display of the operating states of several workstations was used quite early in the development of the Andon systems. The godfather of the TPS, Taiichi Ohno once described it as followed: "When one looks up, the andon (the line stop indication board) comes into view, showing the location and nature of trouble situations at a glance."
In the course of time, the Andon board has increasingly developed into an information board for all employees involved in the process. They display status information regarding the current situation in production, such as the number of units produced per day or per hour, the degree of delivery reliability to the customer or the cumulated amount of backlog. In this way, all process participants are aware of the current situation and can act accordingly.
Andon Boards nowadays
OCT
The Operator Cycle Time is the time an operator needs to fulfill a dedicated process step, including loading and unloading but excluding waiting time.
The Operator Cycle Time is the time an operator needs to fulfill a dedicated process step, including loading and unloading but excluding waiting time.
The Operator Cycle Time is measured from when the operator starts his/her process and is stopped when he/she is ready for the next workpiece (no matter if it’s there or not). Yes I said that the OCT is exclusive waiting time, but not exclusive the waiting time within the process itself. That means if the operator is waiting for a machine, he/she loaded, to finish the operation and unload the workpiece, this waiting time will be included in the OCT.
Most of the time OCT can be seen as the same as “cycle time”. The main difference comes from the waiting time an operator has, while a machine is running a process and the operator him-/herself would be ready for the next piece. This means in the end the OCT is always shorter as the CT. Going even further this means that the OCT can be shortened when installing a HANEDASHI device that autounloads the workpiece after the operation.
As with all lean management activities and targeted increase on productivity and flexibility time is on focus. But make sure to understand the process first, before running improvement actions you have to know what to improve.
OTED
One touch exchange of a die.
Depending on your field of industry the defined times to perform a changeovers varies between 1.5 and 1 minute.
To run OTED successfully following actions are required upfront:
Reduction of adjustments needed down to zero
No fastening with screws needed
100% positive locking between die and tool carrier
Proper fitting methods
Separation between tooling and function
The target is simply explained: The exchange of a die is done with one single motion.
When having a look at the development of improving changeovers the first step is to implement the single-minute exchange of a die (SMED). SMED helps you in the beginning to figure out how to perform the changeover with less motion. OTED is then the high level of changeovers. As mentioned as SMED can be also understood as single digit exchange of a die, yes this means everything under 10 minutes is SMED, OTED stands for the ultimate target. Through continuous improvement actions on SMED you are striving to reach the state of being able to exchange tooling in the takt of your line with one single motion.
In the end with OTED you have to deal like with all the other Lean Tools, don’t just apply it to be cool and “lean”. If it doesn’t make sense for your operation or process don’t do it. But when you decide to strive for OTED and you and your team are convinced by the promised improvements , make sure to understand the process flow first then take action.
Production Diary
The production diary, as part of the shop floor management system, defines a shift based weekly forecast incl. upcoming tasks for mgmt., supporting functions and is openly displayed on the shop floor.
With the help of a production diary, based on a pre-defined shift planning all other functions and outcomes are planned and tracked. This includes the mgmt. team as well as all supporting functions. In order that everyone is aware about the upcoming week the production diary is openly displayed on the shop floor. With the production diary and the pre-set structure of daily meetings of the shop floor mgmt. all daily activities are carried out. Best known part is e.g. Gemba Walks and the included problem solving activities e.g. A3 or just confirming that all processes run as planned.
With this big part of shop floor mgmt. it is clear that all regular meetings planned along the production diary are set. All other unplanned activities or extra meetings need to be conducted respecting the fixed schedule of the production diary.
5 Why
The 5 Why methodology is a well known part of the root cause analysis. Key is to ask five times in the row – why?
The 5 Why methodology is a well known part of the root cause analysis. Key is to ask five times in the row – why? It is not the only way to determine the root cause(s) of problems. Just to mention that it usually comes together with an ISHIKAWA analysis. If you want to get deeper into problem solving including ISHIKAWA and 5Why we recommend you the article taking on the 7Steps approach.
The practice of asking why five times in a row whenever a problem occurs supports you on identifying root cause(s) and to determine effective counter measures that are developed through the process of 5Why. Then it is a simple part of PDCA to develop and implement effective measures.
To be able to steer a wide product portfolio, survive the competitive pressure and at the same time satisfying your customers with a high quality product at a reasonable price can be a tough game. Most of the time you don’t have enough time to run the complete product development cycle, do your validation and verification… The end of the story is that you start production because you need to deliver – which automatically leads to mistakes in running daily business. Therefore, the simple method of 5Why can be used to support, not only, your quality department to get faster to the bottom of problems.
The solution for a problem is not always easy, sometimes the root cause is hidden. Therefore the method is an important element of the root cause analysis. One tries to get to the root of the problem step by step with why questions, because one assumes that several causal connections interlock. The system is easy to explain, but there is a lot behind it. If you really take the time to ask the questions carefully and discuss them, the results are extremely profitable.
You should go through these steps of the 5-Why method. Describe your problem as detailed as possible. As more facts you have, you are faster on getting to the bottom of the problem.
What is the difficulty?
When did it first occur?
How often does it occur?
Is this failure randomly coming or reoccurring in a pattern?
Can you repeat the failure?
What is the effect of this failure?
and so on….
It is very important to get a fast idea of the situation on site. Take the Gemba Walk as great opportunity to talk to the people who are actually involved and to see it with your own eyes instead of guessing from your office.
Avoid making assumptions at this stage - you may draw the wrong conclusions.
Keep calm and try to understand the complete context first.
Understanding the context is where the 5-Why method comes in. Gradually ask why questions in order to get a feeling for the interrelationship of effects. This works for many areas of the company, in production, but also in your private life.
Example:
Problem: I miss all the fun part with my kids…
Why do I miss so much? - Because I’m not often at home.
Why am I not often at home? - Because of my position at work I have long working hours and business trips.
Why do I have long working hours and business trips? Because I can’t get my work done in 8 hours and bad in delegating work.
Why can I get my shit done in 8 hours and miss to delegate things? Because I’m sloppy in prioritizing and time management and don’t trust others.
Why can’t I prioritize my activities and don’t trust others? Because I don’t have the information needed to do so.
Reverse conclusion: If I’m not getting the necessary information in a certain amount of time in an acceptable quality I’m not able to steer my employees but also miss the time with my kids.
Sometimes 2 questions are necessary, sometimes 8 or even more to bring you to the “right” conclusion. But don’t give up half way.
Develop appropriate counter measures:
What contributes to solve the problem and who can implement which measures? How long will this take and what consequences will the implementation have?
First: I should try to have set timeframes with my kids which are holy and untouchable.
Second: I should define what information for me is necessary to run my company.
Third: According to the defined Information I train my employees what I need.
Fourth: I implement a clear systematic approach that I have all information latest at 11:00.
(DING DONG - Sounds familiar? BINGO — Shop Floor Management with a functioning meeting cascade.)
Keep the wheel spinning!
No matter what – before start implementing ad-hoc whatever you find best – take your time to identify what actions contribute to a real long term effect, what effects it will have on other areas, etc. Nothing worse than if you think you are doing something great but in reality you make it even worse.
The cycle of questions is often interrupted too early. The real cause is then not really eliminated and after some time there are repeated difficulties.
You can test it: If the reverse of your assumptions works, you are probably at the end of the causal chain.
As mentioned in the beginning another way is the ISHIKAWA diagram
Just keep in mind that not like with the ISHIKAWA the 5 Why only leads you to one cause for a problem. But as always in life there can be more than just one that leads to an effect. Therefore, the combination of 5Why and ISHIKAWA gives you the best approach to determine causes. It will allow you to represent several major and minor causes that can contribute to the solution.
Get the big picture with an ISHIKAWA drill it down with the 5Why.
Affinity Diagram
The affinity diagram helps you to organize a large number of ideas into logical categories and natural relations.
So you have a large number of ideas and need to organize them. The affinity diagram is the perfect fit to get the job done and to structure your ideas into their natural relationships. Basically the affinity diagram describes a structured outcome from a brainstorm session. You can use it to generate, organize and consolidate information related to a product or process, complex issues or different problems. After the brainstorming session you should group the ides according to their affinity or similarity. This idea creation method was created in the 1960s by Japanese anthropologist Jiro Kawakita.
When should you use an Affinity Diagram
The typical use of an Affinity Diagram is when you are confronted with many influences or ideas in a state of chaos. Sometimes a problem seems too large or just too complex to understand it at first sight. Or you simply want that the whole team has a common understanding of a topic.
Usually you are confronted with this situation:
After a brainstorming session
When analyzing open questionnaires, such as survey results
When collecting and organizing large sets of data
When trying to develop relationships between different ideas
Or trying to reduce input to a higher level of categories
Typical process of developing an Affinity Diagram
The Affinity Diagram process gives a group a direction to go beyond normal creative thinking and defines categories to get all thoughts in order. This technique opens the doors and shows relations in between the whole organization which is typically separated due to department silo thinking. The Affinity Diagram has no limits, so don’t be irritated if you have to deal from 20 up to 400 items after a session. It is a starting point not more not less.
Materials needed: Sticky notes or cards, marking pens, and for sure a large surface (wall, table, or floor). Brown paper is a good way to start.
Step 1:
The brainstorming
Write down all ideas on separate sticky notes or cards.
Spread the sticky notes or cards randomly all over the brown paper
Gather all participants around the brown paper after all notes are taken
Hint: Use big markers so it easy to read for everybody from distance. Make key statements on the notes don’t write an essay.
Step 2:
Try to sort all ideas that are related in some way and group them up
Try to find relations between these several ideas
Let the team sort ideas
Try to find 8-10 relation groups
Repeat until all ideas are grouped
It is fully reasonable that there might be an idea staying by itself or that team members will move an already grouped note again to another. If an idea belongs in two groups, make a second sticky note or card.
Hint: In this step it is crucial that there are chats going on, it has to be done in silence. Focus is on sorting and grouping ideas. Headlines are done afterwards! Not upfront!
Step 3:
Open discussion with your team.
Try to find common categories and define headlines for each group together with all team members. Discuss what you see or why members see an idea in a different category. If necessary, make changes and move ideas between categories. In the end, when all ideas are grouped in the consent of the whole team, define the headlines of each group. Try to find a catchy headline that describes the meaning of the category in short.
Hint: Cards with the headline should be in a different color than the rest and should be self explaining about the group.
Step 4:
If reasonable, try to define “mastergroups” of several “subgroups”.
Sort all ideas to their identified category by placing all ideas under the “headline card”.
Hint: The sorting is done by gut feeling, not with a scientific approach.
SIPOC
SIPOC can be used to clearly define process steps within a process chain.
SIPOC is a > Six Sigma tool that summarizes an entire process at the start of an improvement project. SIPOC can be used to clearly identify process steps within a process chain. A SIPOC diagram is only a snapshot of a process. Each of the letters in SIPOC represent the names of the columns in the table:
S – Supplier, I – Inputs, P – Process, O – Output, C – Customer.
The SIPOC method has its origins in Six-Sigma and is used there in the definition phase of a project. To have it summarized see the following Infographic:
By applying this method, it is possible to quickly gain an overview of all the main elements of a process to be examined, even before more in-depth details are worked out.
SIPOC is a very simple and at the same time very effective method that can also be used in various situations in the lean management context.
Possible applications of a SIPOC can be:
Starting a KAIZEN workshop in order to create a common basic understanding.
To achieve a quick overview (top level) for subsequent process optimization
Simple type of documentation for existing processes
Identification of important process participants (who must attend the KAIZEN workshop)
Definition of the process steps to be investigated within a process chain
How to use SIPOC:
The SIPOC method can be used in many different forms, such as Excel spreadsheets, handwritten tables on flip charts or brownpaper versions using cards or post-it notes.
The easiest way is to start by listing the process steps. No more than 5-7 process steps should be listed, since the SIPOC method is not about carrying out a detailed process analysis, but only about gaining a rough overview.
It often makes sense to note down on the process card those departments or persons who carry out the process for the respective process steps, so that it can be recognized immediately who is responsible for the process.
Input: which input factors are necessary to perform the process step? This could be material, information, machines or a service.
Supplier: who provides these input factors? Do they come from an external supplier or from an internal supplier - perhaps as the output of a previous process step in the process chain?
Output: what is produced as a result in the respective process step. These can be material things such as components, assemblies or finished products, or intangible things such as processed information in the form of a document - e.g. a static calculation or an order confirmation.
Customer: for whom the result was actually produced. Make a distinction between external and internal customers. If no customer is found for the output size, it must be checked whether the process step makes sense at all.
Autounloading
In the lean world “auto unloading” means that every machine is automatically unloading the processed part or component, so that the operators’ task is reduced to only loading the machine.
In the lean world “auto unloading” means that every machine is automatically unloading the processed part or component, so that the operator’s task is reduced to only loading the machine. This also refers to the chaku chaku principle. The correct lean term of autounloading is the Hanedashi Principle which is explained here.
Stay Connected
Ad
We want information fast and in a nutshell. We from OI recommend Blinkist* - because it’s simply the best.
* = Affiliate Link