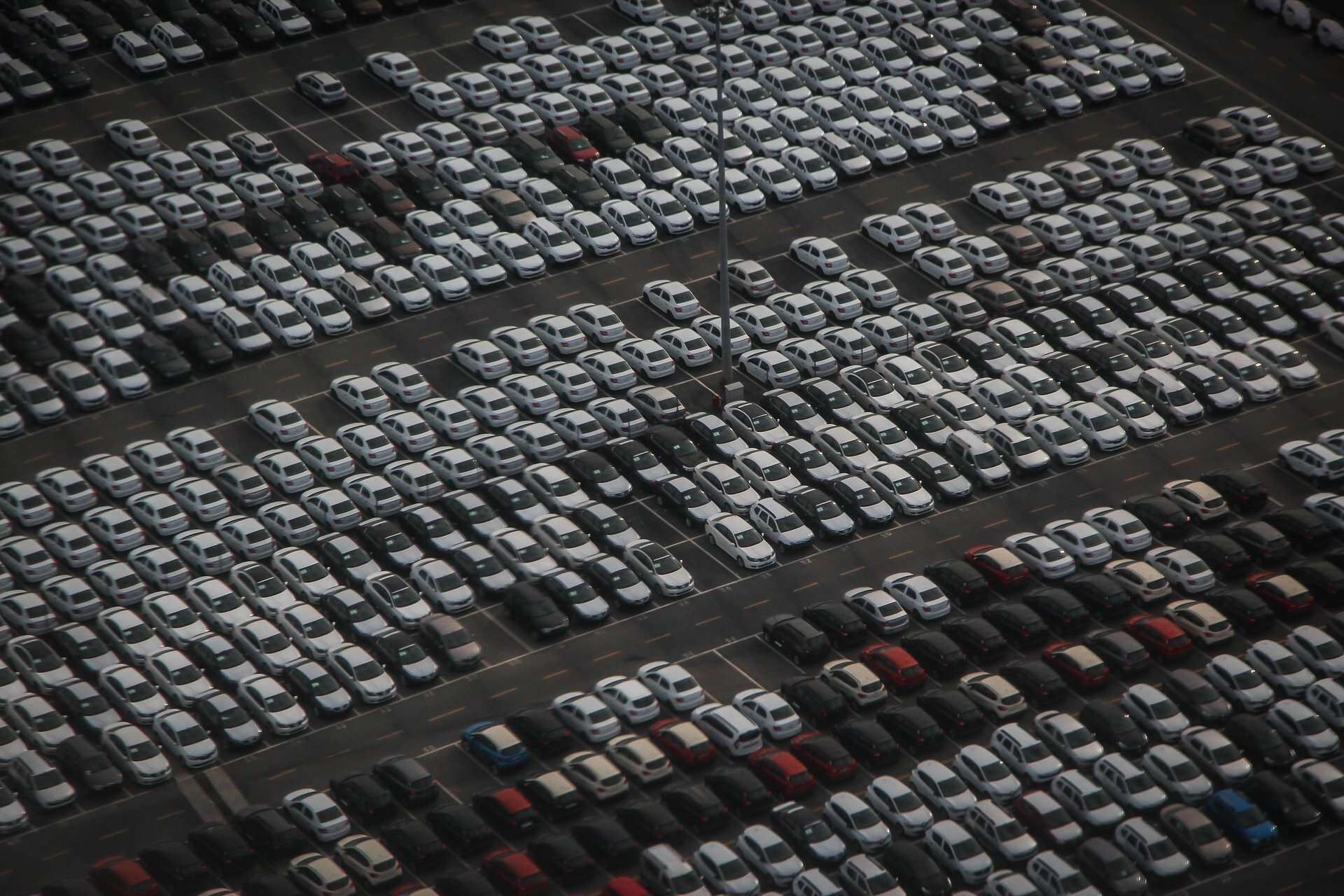
LITTLE PRODUCTION SYSTEM
Flexible Equipment
Flexible facilities are machines, equipment and installations that can be quickly and efficiently adjusted to the product-specific and logistical wishes of the internal and external customers.
In this new article in the series “little production system” we will have a view on equipments and machinery of your facility. Have fun reading and learning.
Definition
Flexible facilities are machines, equipment and installations that can be quickly and efficiently adjusted to the product-specific and logistical wishes of the internal and external customers.
The targets:
No set-up times for platform parts necessary
Customer-synchronous setup times for variant parts are realized
Decoupling of employees and device (binding factor direction 0.1) is realized
The loss of production during relocation of a flexible device is less then one shift
The flexible facilities consist of of autonomous, modular units, which can be converted or combined into production or assembly devices
Resources that are available under the flexible devices are interchangeable
In case of service and assemblies the components of flexible equipments are interchangeable in customer takt
Ensuring the customer synchronous delivery in the required quality from an economic point of view
Cost-effective solutions have advantages (low cost automation)
Key elements:
Set-up in takt
Requirements for the flexible operation
Facilities
Product quality
Costs / economic efficiency
Relocation flexibility
Binding factor (operator / equipment)
Autonomous units
Service friendliness
Work preparation
Provision of operating resources; supply and disposal
Manufacturing strategy by platform and variant parts
Design of devices and tools
Automation (low cost automation)
Key Performance Indicators (KPI)
Setup times
Binding factor
Moving time
Self assessing the levels of fulfillment according flexible equipment
Assess your set-up procedure - set up in takt
Level 1
Planned times are available, but not related to is-time. Setup sequence and duration are always different.
Level 2
Set-up analyses on bottleneck stations and nominal/actual comparisons are partially carried out. Setup times are reduced by setup preparation during machining and first piece inspection. There are setup standards for individual facilities.
Level 3
At all “A” facilities are set-up standards. Systems for fast Set-ups are developed and in pilot areas tested. A strategy for set-up in the team is introduced.
Level 4
At all manufacturing and assembly equipments are set-up/exchange standards. At all “A/B” facilities are scaffolding systems - as far as economical - introduced. High runner lines can be exchanged in customer takt (setup time < 5 Min.). SMED (Single Minute Exchange of a Die) is realized.
Level 5
No set-up times for platform parts. Customer-synchronous set-up times for variant parts. First piece quality without readjustment and test runs. Standardization of:
Facilities /Assemblies
Resources
Work processes (e.g. set-up, process chain).
All factories have problems, writes manufacturing executive Rob Tracy. Sooner or later, your plant will fall behind in on-time delivery, your workforce will lose morale and the production calendar will fill up with emergency “hot list” scheduling. Tracy points out that getting a factory back in shape may be hard, but it’s not complicated. He explains step-by-step how to identify weaknesses, set attainable goals, get the cooperation of the whole organization and make improvements that last.
Read more here.
Requirements for the operation of flexible equipment
Level 1
There are specialists for every equipment.
Level 2
Individual operators can operate several devices.
Level 3
Individual operators can operate and set-up several devices. A concept for the standardization of control panels has been developed.
Level 4
Individual operators can operate several devices. The standardization of the control panels for A-installations has been implemented.
Level 5
Extensive decoupling of operator and equipment. The standardization of the control panels has been implemented in all facilities.
Levels of product quality
Level 1
No process capability, therefore 100% testing.
Level 2
Partial process capability for final processes. Predominantly 100% testing for final processes. Machine capability is a criteria for new purchases.
Level 3
Process capability at all “A” equipments. Targeted measures (e.g. investments / tolerance defusing) to achieve process capability.
Level 4
Process capability on all “A/B” equipments. Targeted measures (e.g. investments/tolerance defusing) to achieve process capability.
Level 5
On all “A/B” machines CpK > 1.66 (no more random checks). Annual PPM halving on all “A/B” machines.
Costs and economic efficiency
Level 1
Cost allocation is inadequate. Cost accounting is not transparent.
Level 2
Cost accounting for individual processes is realized.
Level 3
Cost accounting for individual processes and direct support processes is implemented (-> extended profitability analysis).
Level 4
Cost accounting for individual processes, direct and indirect support processes is implemented (-> extended profitability analysis).
Level 5
Process cost accounting is realized.
Relocation flexibility
Level 1
Fixed, rigid facilities. There are sometimes no or only individual interfaces at the facilities (inside / peripheral). There are no connecting elements.
Level 2
Expenses for moving is high (10.000 EUR). Duration of the move is long (approx. 5 days). There are partly standardized fasteners. There is partly a supply grid for electrics.
Level 3
Relocation is more flexible due to standardized procedure (costs <7.500 EUR, takes about 2 days). There are technical standards for ...
Interfaces
Fasteners
Supply voltage
Network connection
Cooling and lubricating oil
etc.
“A” facilities are retrofitted - if economical.
New equipment is procured on the basis of the established standards.
Level 4
In the case of new buildings and conversions, grids for supply and disposal facilities have been implemented. “A-/B” facilities are - as far as economically feasible - designed to the specified standards retrofitted. A move costs < 5.000 EUR and takes about 1 day. New facilities do not require special foundations.
Level 5
The relocation of flexible facilities is realized in about 0.5 days.
Binding factor (operator/equipment)
Level 1
High runner line – 1,0
Small batch production: unplanned
Assembly: According to cycle compensation time in the assembly cycle
Level 2
High runner line – 0,8
Small batch production: planned for A-equipment
Assembly: Target: Tact compensation time goes towards 0
Level 3
High runner line – 0,5
Small batch production: planned for A- and B-equipment
Assembly: ongoing optimization
Level 4
High runner line – 0,3
Small batch production: C equipments have the binding factor of 0.0
Assembly: ongoing optimization
Level 5
High runner line – 0,1
Small batch production: ongoing optimization
Assembly: ongoing optimization
Autonomous units
Level 1
Rigid linking and integration of the units to form facilities (e.g. transfer lines, special machines, assembly lines). The functions of the equipment are constantly monitored by operators.
Level 2
High degree of electrical / mechanical linkage between the units and equipment. Pilot projects for unattended breaks have been implemented. “A” facilities are improved so that a customer takt can be produced without operator supervision.
Level 3
Depending on the situation, “A” equipment can be operated without automation and integrated additional equipment. “A” facilities run through during the breaks. In case of malfunctions, the equipment switches off automatically. End of cycle and malfunctions are indicated by optical and acoustic signals.
Level 4
Depending on the situation, “A/B” equipment can be operated without automation and integrated additional equipment. “A/B” equipment runs through during the breaks.
Level 5
Autonomous, modular units that can be combined as required to form production/assembly facilities.
Service friendliness
Level 1
Equipment is only repaired by specialists.
Level 2
Assemblies and components of the equipment are gradually being standardized.
Level 3
The quick exchange of assemblies and components is designed and tested in pilot cases.
Level 4
The quick exchange of assemblies and components is implemented for “A/B” installations.
Level 5
Assemblies and components can be exchanged in customer takt.
Work preparation
Level 1
Equipment is planned and procured by specialists.
Level 2
Workflow planning, work and time studies, NC programming, fixture and tool design, etc. by specialists. Selection and implementation of workshop-oriented NC programming systems.
Level 3
Planning and procurement of equipment with the involvement of all affected employees. First in-house developments of simple devices and creation of simple NC programs by the operator.
Level 4
Operators are involved in the work preparation and know the main and supporting processes. Operators are qualified to independently develop simple devices and tools and to create NC programs.
Level 5
Work preparation in the island team under consideration of the process chain. Operators independently develop simple operating equipment (low cost automation) and create NC programs.
Provision of operating resources, supply and disposal
Level 1
Central supply of resources and tool presetting. Central supply and disposal.
Level
Frequently used devices and tools are stored on the island.
Level 3
Devices for high runner parts are located decentrally in the immediate vicinity of the equipment. Decentralized tool dispensing systems have been developed and introduced in pilot cases. An emergency plan has been drawn up for the failure of central supply and disposal units.
Level 4
New operating resource supply concepts have been developed and tested in pilot cases for facilities that produce on demand. The flexibility of the equipment is supported by tool removal systems. The emergency concept for the central supply and disposal units has been implemented. Emergency plans have been drawn up for the individual areas.
Level 5
Equipment supply concepts for demand-driven equipment have been introduced. Production is ensured even if central supply and disposal units fail.
Manufacturing strategy by platform parts and variant parts
Level 1
No clear difference in demand-oriented control.
Level 2
Partial families formed as standard for...
High runner lines (consumption-controlled)
Residual production (demand-driven).
Level 3
The machine park is divided into high runner lines and remaining production.
Level 4
Platform parts and "One-Piece-Flow" for variant parts implemented.
Level 5
Limited "flexibility" with standard machine for platform parts. High "flexibility" (complete machining) for variant parts.
Design of devices and tools
Level 1
Devices and tools are designed for individual positions.
Level 2
Devices and tools are designed for families of parts and for one process.
Level 3
Devices and tools are designed for families of parts and for several processes.
Level 4
25 % of the jigs / tools are interchangeable among the equipment in the process chain.
Level 5
50 % of the jigs / tools are interchangeable among the equipment in the process chain.
Automation
Level 1
All variants up to the highest degree of automation available.
Level 2
Individual process-related automation is available, buffer size approx. 0.5 hours.
Level 3
30 % of the high runner lines are equipped with low cost automation. In small-batch production, automation adapted to the overall problem has been investigated and, where appropriate, implemented to 30 %.
Level 4
60 % of the high runner lines are equipped with low cost automation. In small-batch production, automation adapted to the overall problem has been investigated and, where appropriate, implemented to 60 %.
Level 5
100 % of the racing lines are equipped with low cost automation. In small-batch production, automation adapted to the overall problem is examined and, where appropriate, implemented 100%.
Standards and Visualization
Learn about the basics of standards and visualization in this article of our series “little production system”.
In this article we go into detail of standards and visualization
First things first - lets define our understanding of standards and visualization
Standardization and visual management is a management tool which serves to define and develop clear, binding process flows in the product creation chain and the entire organization of the company and to make them visible to all employees.
The targets:
A self-dynamic behavior of all employees involved in the processes with the aim of a permanent further development has been created
The immediate identification of deviations from standards and a direct control of success is ensured (target-performance comparison)
The processes and procedures are secured and further developed.
The productivity is increased
Continuous avoidance of waste is encouraged
The work processes are even and balanced
Flexible staff deployment is encouraged
Key elements for this are:
Visualization of:
Paths, parking spaces
Tools, operating resources
Relevant work steps for efficiency, quality, safety
Production flow and process sequence
Quantities and faults
Regular audits for continuous improvement
Standardized documentation:
Information areas in all areas
Visible, up-to-date data is used for goal-oriented improvements by teams
Uniform documentation
Connection between team goals / company goals
Levels of fulfillment according the standardization and visual mgt. - Procedures
Level 1
Floor and floor space markings, process visualization hardly existent, not up-to-date or not in use. The employees try to give "their best".
Level 2
Visualization (paths, places) according to a uniform standard. Specialists have developed methodical standards. The standards largely describe the what but not the how.
Level 3
Visualization of tools, equipment, etc. available. Standards are developed in the areas. Working steps for quality, safety and efficiency are clearly defined and recognizable everywhere.
Level 4
Production flow and process sequence are clearly visualized. All direct and indirect activities are subject to standards. No standard is older than 5 months. Corresponding qualification programs are continuously updated.
Level 5
Standards are available for all processes, clearly visualized and acted upon. Deviations can be detected immediately. Regular audits are carried out to check and improve.
Levels of fulfillment - Operating and Performance Data
Level 1
On-site information refers to points prescribed by law; hardly any operational information. No actualization, responsibility is not defined.
Level 2
Arbitrary, chaotic visualization on different levels. Selective representation of data, partly not updated. Little to no understanding of visualization.
Level 3
Visualization of performance data and partly of improvement activities. Visible correlation between measures at company and department level. Updating is carried out routinely. Information oriented to target groups. Current target/actual comparisons are visible. Visualized management systems (e.g. handling of errors, disturbances, deviations ...)
Level 4
Visualization of performance data and goals in 80% of all areas, up-to-date and adapted to individual requirements. Updating is standardized. Employees assume responsibility for the presentation and updating of certain information and data.
Level 5
In all areas there are information and planning centers. The visualization of current data supports goal-oriented planning and improvement activities. The company-wide standard formats are used. Information is personalized. The transparent factory.
One Piece Flow
One Piece Flow as key component of the “little production system” series.
One Piece Flow - every one living a life in production comes across this topic at least once per day. Either in the planning phase of an assembly line or fighting daily capacity issues. Let’s have a short look insight this topic.
Definition
In flow production, machines and workstations are arranged in this way, that the material is transported by the shortest route and the workpiece flows through the process chain.
The targets:
Movements and transports take place as the crow flies
Downtimes and stocks are avoided
The processing times are reduced
Key elements:
The material flow is free of crossings
Clear, visualized material flow
Installations are arranged in the order of operations and can be insert fast and flexible into a new process layout
Machines are close together and connected by slides and rolls, the investment calculation is done in process chain analysis
Key Performance Indicators (KPIs)
Lead time
Stock value
Turnover rate
Distances
Self assessing the levels of fulfillment according one piece flow.
Assess Your Layout concerning one piece flow
Level 1
Functional arrangement in a workshop production.
E.g. islands of processing: soft machining, hardening, hard machining and assembly are locally separated areas.
Tools and equipments are stored where space is available.
Level 2
Concept for material flow oriented layout is available.
Pilot projects / pilot process chains have been implemented.
Level 3
Machines are material flow oriented (e.g. in U-shape).
Consistent responsibility for soft and hard machining.
Pre-assembly or processing shops are service providers.
The most important operating resources for “A” parts are on site.
First production-related support services (service, operating resources, measuring technology) are installed on site.
Level 4
Machines are so close together that there is no room for buffers between the machines.
The one piece flow is optimally enabled.
The entire process chain is arranged in a U-shape or a comparable material flow-optimized form (fishbone form).
A technological leap in pre-assembly processes is required to integrate the processes into the U-shape.
Level 5
Optimized factory layout. Assembly and in-house production are spatially combined.
All necessary production-related support services (service, operating resources, measuring technology) are installed on site.
Zero Defects
Learn about the basics of zero defects in this chapter of our “little production system”.
Zero Defects - Failure Strategy (First Time Quality - FTQ). This article gets a little touch on the chapter of zero defects and failure strategy.
First things first - lets define our understanding of zero defects and first time quality FTQ
First time quality (FTQ) is a comprehensive approach to the implementation of the "zero - defects strategy" in all steps of product and process development and the value chain.
The targets:
Consistent method application in all product life cycles is ensured
Error-free production (prototype > series > customer service) is achieved
The maintenance and improvement of process and series quality is guaranteed
FTQ is valid for all company processes
The processes are trouble-free
The IATF 16949 or ISO/TS 16949 requirements are fulfilled
Key elements:
Description of the process and product development, with the corresponding tools, up to series production: Advanced Quality Planning (AQP).
Levels of fulfillment - Quality Planning
Level 1
There is no system for advance quality planning (AQP).
Level 2
D-&P-FMEA’s are used sporadically and uncoordinated.
Level 3
There are standards for advance quality planning. Elements of these are used without the need to monitor measures and deadlines.
Level 4
All elements of the AQP are applied. Continuous project plans are available. An auditing does not take place.
Level 5
The AQP is continuous from product development to the customer. All AQP elements are lived and audited at regular intervals.
Fulfillment levels of quality improvement
Level 1
Problems are ignored. The blame is placed on looking for the other one. Solutions are found based on experience in the event of an error. Notices are general held and not up to date.
Level 2
Partial informal records to problems and measures. Some Data is recorded but hardly analyzed. Errors and problems already exist longer and always kick back on.
Level 3
Errors and problems are recorded and evaluated. The most important problems are being addressed by some Q-employees with a formal system edited. Problem solving projects are initiated. An audit system to ensure permanent problem solutions is installed.
Level 4
All errors and problems are controlled in a PDCA control loop. A large part of the employees participates in the team of problem solvers. Problem solving steps are documented and visualized. The improvement process is regularly audited. Quality objectives are visualized.
Level 5
Errors are potentials. All areas and employees take part in systematic problem solving approach. Problems become immediately analyzed, measures are initiated immediately. All errors and problems are solved at their "root" grabbed and released. Ambitious quality targets are agreed, developments are known and visualized.
Dealing with errors and non-conforming products
Level 1
Defective products or products that are not corresponding to the specifications, lie without marking in the shop floor area and are referred to as committee considered.
Level 2
Defective products are marked, but remain without further consideration. Partly become informal kept records.
Level 3
Daily recording of non-conforming products and sharing, analyses are carried out. Visualized representation to type and frequency of errors. Partial problem solution with internal suppliers. Regular communication with external suppliers is in place.
Level 4
Defective material / products are analyzed and systematically reduced. Errors are reduced in costs and ppm measured, visualized and connected with targets.
Level 5
Detailed elaborated handling system for deviations is introduced and is for all employees applied. Costs and trends are created for every area, determined, analyzed and visualized. Main problem points will be made by means of Poka-Yoke solutions eliminated.
TPM
Productive and preventive maintenance, not only nice to have, see in this chapter of our “little production system” some insights and hints of self assessment.
TPM - Total Productive Maintenance and preventive maintenance. This article gets a little touch on the chapter of Total Productive Maintenance as well as preventive maintenance. It might be confusing as everywhere in the lean world productive maintenance is set but also preventive maintenance is in the chapter.
First things first - lets define productive maintenance (TPM)
TPM (Total Productive Maintenance) is a systematic approach to the comprehensive preventive maintenance of machines, equipment and plants (M.E.P.)
The targets:
The unplanned technical failures are minimized/eliminated
Technical availability > 95% of M.E.P., where economically reasonable, is achieved
More than 80% of the total maintenance time is planned preventive maintenance
TPM is used in all M.E.P.
Spare parts are available in the right quantity when needed
Key elements:
Procedure for introduction
Maintenance methods
Technical availability
Work organization
Qualification Operator/Service
Spare parts
Influence on M.E.P. manufacturers
Documentation
Development and application of methods for damage - early detection
Key Performance Indicators (KPI)
Availability indicator, overall plant efficiency (OPE)
Key figures of the TPM assessment sheet
Maintenance costs
Service - Reaction target
For your self assessment we will mention now the 5 levels of fulfillment for some key parts of TPM and preventive maintenance.
Levels of fulfillment - procedures and introduction
Level 1
No systematics, preventive maintenance as required.
Level 2
TPM - implementation (stages 1-3) for bottleneck or output relevant machines, planned alternative production.
Level 3
TPM - implementation (stages 1-3) for all “A” machines and associated supply facilities, advance and emergency strategies are available.
Level 4
TPM implementation (stages 1-3) for all “B” machines incl. associated supply facilities and stages 4-5 for all ”A” machines; pre-run and emergency strategies are available.
Level 5
TPM implementation (level 6) in all M.E.P., creating a lead time and having emergency strategies in place.
Fulfillment levels of Maintenance Methods
Level 1
Repair > 90% (crash, planned); preventive maintenance (experience-based, time-dependent, preventive) <10%.
Level 2
Repair < 80% (crash, planned); preventive maintenance >20% (experience-based, time-dependent, preventive).
Level 3
Repair < 50% (crash, planned); preventive maintenance >50% (experience-based, time-dependent, preventive).
Level 4
Repair < 30% (crash, planned); preventive >70% maintenance (experience-based, time-dependent, preventive).
Level 5
Repair < 20% (crash, planned); preventive >80% maintenance (experience-based, time-dependent, preventive).
Technical availability
Level 1
Approx. 80 %, high waiting times, line stops.
Level 2
> 80 %, less waiting times, but considerable additional costs due to alternative production.
Level 3
Improvement to > 90 %, for “A” machines. No waiting times due to planned maintenance.
Level 4
Increase “A“ machines > 90 %, “B” machines: + 5 %, where economically reasonable. No waiting times due to planned maintenance.
Level 5
> 95 %, where economically reasonable, no waiting times due to planned maintenance.
Levels of Work organization
Level 1
Central service, specialist team. Operators not included. All cleaning and maintenance work is carried out by the area service.
Level 2
Area service by team of specialists and simple maintenance and cleaning work carried out by the operator.
Level 3
Area service by specialists and execution of necessary activities according to maintenance plans prepared by operators and preventive maintenance (PM) - plans of service.
Level 4
Specialists available for everyone at short notice (cross-domain deployment). Operating staff actively supports the specialists.
Level 5
Comprehensive inspection, maintenance, repair of the equipment by a team (operators and specialists from inside and outside).
Qualification of operator services
Level 1
No operator qualification. Specialists for machine groups and individual fields.
Level 2
Operator qualification according to TPM implementation (step-by-step plan) Specialists create and work through PM plans. Qualification across machine groups.
Level 3
Further qualification of the specialists as trainers. Like level 2 and further additional qualification, e.g. hybrid systems + new equipment.
Level 4
Further qualification of the specialists as trainers. Specialists with hybrid training.
Level 5
Further qualification of the specialists as trainers.
Spare Parts Management
Level 1
Unregistered spare parts in small unstructured warehouses based on the experience of maintenance staff. Call on demand and not recorded.
Level 2
Spare parts planning and systematization of the warehouse (IT technical recording).
Level 3
As under level 2 and classification and reference source release (standardization).
Level 4
Spare parts for “A” machines are available in the right quantity in case of need.
Level 5
Spare parts available in the correct quantity and when required cross-company consignment stock.
Influence on machinery, equipment and plants (MEP)
Level 1
No data recording on availability or failures.
Level 2
Use of the standard documentation of the M.E.P. manufacturer.
Level 3
Display of the overall plant efficiency at “A“ machines, exchange of information with M.E.P. – manufacturers.
Level 4
Reporting of the overall plant efficiency at all plants. M.E.P. - Manufacturer uses TPM experience systematically.
Level 5
Networking machine, service and M.E.P. - manufacturer. Use of experience for own further developments of standard machines (competitive advantage).
Documentation
Level 1
No or outdated maintenance plans, no standards.
Level 2
Maintenance plans and individual standards are available.
Level 3
In the TPM - Workshop maintenance, cleaning and preventive maintenance plans including standard lines for the service were worked out. Use the flow of information internally and to manufacturers + use the manufacturer's experience.
Level 4
Intervals for maintenance, cleaning and preventive maintenance are standardized, documented and coordinated.
Level 5
Flexible planning system to coordinate all maintenance activities.
Preventive measures levels of fulfillment
Level 1
Technical individual solutions available (sensors).
Level 2
Individual solutions for “A” machines are available.
Level 3
Classifications for preventive systems have been developed.
Level 4
Preventive systems are introduced for “A” machines.
Level 5
Preventive systems themselves - systems are where it makes economic sense to have them.
Material Flow
Material Flow - Pull in the best from you can get, just another part of the “little production system” series.
The means of this article in the series “little production system” we will have a short insight on material flow without buffers - or simply called pull principle.
Definition
The indicator of material flow without buffer is that only as much material is moved, as in the next step is used and can be processed. Anything beyond that is in the way and obstructed.
The targets:
Avoid overproduction
Stocks are reduced flexibility is elevated
Areas are reduced, distances are shortened
Key elements:
Material is only available on planned and visualized buffers
1 piece or 1 set is delivered by low cost automation
Consumption control / Pull - principle
Mixed transport at short intervals
The material flow is continuous
Transport containers and systems are delivered in smaller quantities and more frequent
Delivery intervals are adjusted to the cycle time
Key Performance Indicators (KPI)
Buffer area
Stock value
Logistics costs
Self assessing the levels of fulfillment of your material flow without buffers.
MICRO LEVEL of production flow
Level 1
Workshop production - Technology island
Level 2
Island production without linking the machines. Installation is flow-oriented
Level 3
In other elements (e.g. TPM, FTQ, Flexible Facilities) corresponding services are provided.
For example: Machines and equipment are in TPM level n. Flexible facilities for “A”- and “B”-parts are available.
Level 4
Upstream and downstream operations are close together, partially interlinked. Transport routes/time are used for testing, marking or washing.
Level 5
Upstream and downstream operations are moved close together and connected by chutes, roller conveyors, etc.
Documentation that should be available
Process layout; material flow without buffer, material flow in cycles and flow production
Micro level stock and buffer
Level 1
Stocks are not visualized.
Level 2
Stocks / buffers between the machines are visualized (place and quantity).
Level 3
Buffers are smaller than a daily amount.
Level 4
One-piece/set flow. Accumulating buffers as keying sequence and/or disturbances are still possible.
Level 5
One-piece/set flow. No buffer between the process steps.
Micro level transportation
Level 1
Transport of the work piece carriers or base frames by handcart between the machines. Unplanned transports.
Level 2
Transport with work piece carrier or base frame in equal, fixed Quantities. No forklift as a means of transport in the field.
Level 3
There are no base frames in use. Transport is carried out with work piece carrier.
Level 4
Manual transport at working height. Uniform transfer heights avoid lifting and lowering procedures.
Level 5
Work pieces are moved from machine to machine via rollers, slides, belts. No means of transport!
Micro level material flow control
Level 1
Manual job control is carried out by specialists. Push principle! High planning and control effort. No visualization available.
Level 2
The material flow is clearly identifiable. Order control is still required. Responsibility for the control lies with the shiftleader.
Level 3
No processed work piece is discharged from the process chain. Interventions in the process chain are only necessary in the event of malfunctions.
Level 4
Only available together with level 5.
Level 5
No order control within the process chain necessary.
Macro level stock and buffers
Level 1
Buffer between the islands are larger than 1 lot (partial lots in motion).
Level 2
Lot sizes are smaller than the daily requirement for “A” and “B” parts. “A” and “B” parts no longer go into stock.
Level 3
Lot sizes correspond to the quantities per handling rack. Buffers between the islands correspond to a maximum daily requirement.
Level 4
Reduced stocks through levelled production for “A”-parts (periodically the same quantity per part number).
Level 5
A buffer (smallest quantity is 1 piece or 1 set) is permitted for control. Levelled and smoothed production for “A” and “B”-parts.
Macro level transportation
Level 1
Transport according to order. In the processing shop, workpieces are loaded from transport racks into processing racks and vice versa.
Level 2
Mixed transports at short intervals, partly still with forklift, partly already with train + trailer between the halls.
Level 3
Continuous transport system (e.g. transport train / overhead conveyor) between upstream and downstream processes. In some cases, workpieces are already placed in the downstream needed racks during the upstream process. No transports between process step I and process step II within the process chain.
Level 4
The transport containers used avoid repackaging between upstream and downstream processes. Example: Workpieces are placed directly on the finishing frame after the last pre-processing step. Uniform transfer heights avoid lifting and lowering
Level 5
Workpieces are transported in workpiece carriers or containers with standardized modular dimensions.
Macro level material flow control
Level 1
Demand-controlled batch size production. "Economic batch sizes".
Level 2
First part numbers in consumption control between assembly and last production process. Previous block formation (during material call-off, during transport, during processing, etc.) no longer applies. In the pre-assembly area, no more than two units from the same batch are processed one after the other.
Level 3
Consumption control for all “A” and “B” parts. Any part can be processed on any day. “C”-parts management for purchased parts through logistics service providers.
Level 4
Levelled production. Consistent consumption control for “A” and “B” parts throughout the entire process chain. Sequenced delivery for selected part numbers.
Level 5
Levelled and smoothed production.
Ideas and solutions
Ideas and solutions as one key element of every production system - so it has to be in the series of “little production system”.
Ideas and solutions are our daily companions in manufacturing industry. For real operational excellence the continuous improvement is key - one part of it is the proper problem solving therefore we are having this article in the series “little production system”, to have a short look at the idea and solutions criteria.
Definition
The Ideas and Solutions element describes methods for the systematic creation of ideas that serve the continuous improvement of all company processes.
The targets:
Systematic identification, elimination and avoidance of waste of all kinds is promoted, involving all employees of the company.
The element has the task of making the creativity and knowledge of all employees available to the company.
Key elements:
Targeted application of problem-solving techniques
Interdisciplinary problem-solving teams for direct implementation
Idea > Implementation > Standardization
Premium (simple, unbureaucratic handling, rapid implementation)
Works agreement CIP
Raising awareness of problems
Self assessing the levels of fulfillment for your Ideas and solution process in your organization.
Cost reduction
Level 1
Specialists carry out partial improvements. Decisions are not made at all or only by upper management.
Level 2
Improvement mainly by specialists. Targets are set at departmental level. These must be achieved, no matter how. The costs for labour and material per unit are transparent. Standard costs are defined, monitoring mechanisms are in place.
Level 3
Clear objectives / target topics for waste reduction are defined (stocks, rejects, responsibility for indirect costs at factory level). Teams carry out cost reduction.
Level 4
Potentials are determined by value analysis. Clear goals and action plans are developed and implemented. Unit leaders prepare budgets for direct and indirect costs, make recommendations for targets and coordinate them with superiors and colleagues.
Level 5
Budget responsibility at team level. Released resources are used for further optimization.
Productivity
Level 1
Productivity improvement through isolated instructions to work "more". Waste is ignored.
Level 2
Attempts are made to eliminate obvious waste and balance workloads. For the employees regular information on the performance of the company and its own performance level is provided.
Level 3
The eye for non-obvious waste is sharpened. Analytical waste analyses are carried out. Data is processed to compare value added to waste. Indirect activities are included and improved.
Level 4
In the reduction of waste, great importance is attached to details. Principles of economy of movement are applied. Analytical skills are developed.
Level 5
Continuous performance improvement based on agreed targets and action plans by teams. Customers and suppliers are involved.
Employee involvement
Level 1
No passing on of own implementation only for self-interest, no standardization. Hardly any formal improvement, "This is not my job, others are responsible".
Level 2
The existing system serves more for external presentation. Proposals are submitted, but implemented by others. Meetings take place regularly.
Level 3
A structured system has been introduced, but is only used by < 50% of employees. Resources are available. Everyone knows value-adding from non-value-adding activity to separate. Employees are relocating on site. Targets are agreed. Evaluation of development through process and result audits.
Level 4
CIP is part of your daily work. Core topics are intended to stimulate the imagination. Employees work together as a team on cross-team and cross-functional improvements. Infrastructure and resources are available for teamwork and on-site implementation.
Level 5
Improvements and their implementation are carried out autonomously by teams. Recognition programs (e.g. company visits, joint activities ...) are carried out.
Team Work
Team Work - what does it mean? What does it take? Great work can never be achieved alone. If you want to grow and take it to the next level - team work is key. Operations Insider - connecting the dots.
Team Work - what does it mean what does it take. Great work can never be achieved alone. If you want to grow and take it to the next level - team work is key. In this article of the “little production system” we will have a look at it and some self assessing elements.
Definition
Teamwork is characterized by the fulfillment of work tasks by a number of employees with complementary skills. They are committed to these tasks, have a common goal, use an approach for which they are committed as a team.
The targets:
The activation and use of human resources
The technical and organizational possibilities for achieving the company's goals
Key elements:
Defined roles, tasks and communication structures for island teams, project teams, management teams, divisional and departmental teams
Responsibility for quality, costs, time and improvement of standards
Development of social, technical, methodological and leadership competence
Regular development/appraisal interviews by managers
Practical flexibility of use
Regular team meetings
Problem solving activities
Team networking / cooperation
KPI
Team performance
Employee satisfaction
Check your organization with this brief self assessment of level of fulfillment
Work organization level of fulfillment
Level 1
Classical hierarchy, individual workstations division of labour.
Level 2
Spatial grouping of workplaces and plants to islands with classical division of labour.
Level 3
A new form of work organization has been developed and tested in pilot cases in the form of group work.
Level 4
The new form of work organization - all employees work in groups - has been implemented across the board.
Level 5
Within the framework of the agreed objectives, the groups jointly assume responsibility for quality, delivery dates, productivity and optimum use of resources.
Standards - level of fulfillment
Level 3
Standardized processes are documented and visualized.
Level 4
The established standards are lived.
Level 5
The established standards are lived and developed independently.
Communication structure levels of fulfillment
Level 3
Team or group discussion with a lack of efficiency. Established information and communication structures.
Level 4
Regular, efficient team or group discussions. A part of the communication structure is ensured across the board with the help of the "group speaker" function.
Level 5
Existing scope for action is perceived. Defined communication structures exist. Cross-team networking and cooperation serve to achieve goals.
Level of fulfillment – Qualification
Level 1
The level of qualification for professional competence is recorded according to the situation.
Level 2
The level of qualification for professional competence is regularly and systematically recorded and documented. Standardized training programs for occupational safety exist for new employees.
Level 3
The level of qualification in technical, methodological and social competence is regularly and systematically recorded and documented. For new employees, there are area-related familiarization programs.
Level 4
The level of qualification in technical, methodological and social competence is regularly and systematically recorded and documented. Demand-oriented and individual qualification plans are implemented and their effectiveness documented. Divisional and cross-divisional training programs are in place for new employees.
Level 5
The level of qualification in technical, methodological and social competence is regularly and systematically recorded and documented. Needs-oriented individual qualification plans are implemented and their effectiveness documented. Short training courses are a company standard. Divisional and cross-divisional training programs are in place for new employees.
Flexibility level of fulfillment
Level 2
Work tasks, time and place are determined by the supervisor.
Level 3
The employees organize themselves with support in terms of work tasks, time and place according to the standards
Level 4
The employees organize themselves partly independently with regard to work tasks, time and place in relation to the standards.
Level 5
The employees organize themselves independently with regard to work tasks, time and place in relation to the standards.
Operating Time
The operating time is the time available for machines and systems. Targets are order adjusted usage of machinery and factories.
As usual in the series of our “little porduction system” we keep it short and serve it in a nutshell.
Definition
The operating time is the time available for machines and systems.
The targets:
Order-adjusted use of machinery and equipment.
Key elements:
e.g.
The core operating time is 120 hrs/week (e.g. 5 days/week a. 24 hours) + flexibility (+ / -)
The increased operating time is 144 hrs/week (6 days/week a. 24 hrs)
The increased operating time in special cases is 168 hrs/week (7 days/week at 24 hrs)
Team- and order-oriented use of personnel resources through flexible working hours (+ / -)
Individual approval procedures are no longer necessary due to working time models agreed with the workers’ council
Compliance with legal requirements and collective agreements
Attendance time = working time
Smooth shift hand overs without interrupting production
Production through breaks
KPI
Factor of operating time used OT/168 hrs.
Level of fulfillment operating time in production
Level 1
Employees are divided into fixed shifts. Independent of the capacity situation, the shifts are run. Work absences (vacation, flextime, etc.) are primarily based on personal interests; approval by superiors. Rigid, uniform shift order without overlapping.
Level 2
Employees are divided into fixed shifts. They adapt to the current capacity situation according to instructions, various working time models can be applied using approval procedures. Work time off (vacation, flextime, and so on) is based on personal and company interests. Approval by superiors. In multi-shift operation there are fixed area-related shift changes with production interruption.
Level 3
Employees are divided into fixed shifts. Occasionally, employees adjust their working hours independently to the current capacity situation. By means of a sufficient number of agreed working time models, the entire range of necessary operating times is covered flexibly, with approval procedures. Work absences (vacation, flextime, etc.) are partly discussed in the team and coordinated with the supervisor. In multi-shift operation, there are fixed area-related shift changes without production interruption for bottleneck machines.
Level 4
Some of the employees adjust their working hours to their tasks and goals. By means of a sufficient number of agreed working time models, the entire range of necessary operating hours is covered flexibly, in some cases without the need for approval procedures. Time off work (vacation, flextime, etc.) is generally determined in the team and coordinated with the supervisor. In multi-shift operation, there are fixed area-related shift changes without interrupting production.
Level 5
Employees adapt their working hours to the tasks and objectives to be fulfilled. A sufficient number of agreed working time models cover the entire range of necessary operating hours flexibly without the need for approval procedures. Work absences (vacation, flextime, etc.) are arranged independently in the team. Work is handed over smoothly without interrupting production.
Operating time
Level 1
The core operating time is 5 working days per week á 20.5 hours.
Level 2
The core operating time is 5 working days per week á 20.5 hours. Plus special arrangements.
Level 3
The core operating time is 5 working days per week á 24 hours. Plus a maximum of one weekend shift + special arrangements. The operating time (capital-intensive / bottleneck machines) is six working days per week á 24 hours. For preventive maintenance, production downtimes are defined for bottleneck machines, taking into account dependencies.
Level 4
The core operating time is 5 working days per week á 24 hours. Plus maximum 2 weekend shifts + special arrangements.
Level 5
The core operating time is five working days per week of 24 hours. The maximum operational usage time is 6 days per week á 24 hours. The operational usage time (capital-intensive / bottleneck machines) is seven working days per week á 24 hours. For preventive maintenance, area-related production downtimes are defined taking dependencies into account.
Payment
The remuneration system describes the link between performance, qualification, commitment and payment.
In this article me make it short and simple.
Definition
The remuneration system describes the link between performance, qualification, commitment and payment.
The targets:
Mobilization and utilization of the performance potentials of people, resources and organization. Remuneration is an important management instrument.
Key elements:
System is simple, transparent and variable (+ / - ) and uniform for all collective agreement employees
Qualification and requirements
Result orientation (company, division)
Coupling to standards for team/employees
Achievement of objectives (team / employees)
Special bonuses
Performance reviews
Level of fulfillment payment
Level 1
The remuneration system is based on a description of requirements and the corresponding needs-oriented qualification for the individual workstation. Service components are partly fixed and partly variable. Target values of the employees are the degree of time and the "front water". Non-systemized, special payment independent of results at company level. No special bonuses.
Level 2
There are several charging systems. Bonus wages and other performance components are partly fixed and partly variable. Linking to performance standards is not practiced. The remuneration systems allow premiums for successful special promotions. Inconsistent, sporadic application
Level 3
Only the premium wage and the time wage exist in production. The first concepts for a uniform payment system have been developed. The remuneration systems are based on a description of requirements and the corresponding needs-oriented qualification related to individual workstations and group work. Service components are partly fixed and partly variable and linked to performance standards.
Level 4
A uniform remuneration system for wage earners has been developed and implemented in a cost-neutral manner. A uniform remuneration system has been developed and adopted for all levels. The basic performance component is linked to minimum conditions (fixed). The variable component is defined and linked to targets. Behavioural characteristics (e.g. compliance with standards) are taken into account. The remuneration system applies bonuses for defined and successful special promotions
Level 5
A uniform fee system has been implemented at all levels without affecting costs. The remuneration system is based on a description of requirements and the corresponding needs-oriented qualification for teamwork (comparison with teamwork). The variable component is defined and linked to targets. Participation in company results, divisional results according to the target agreement.
Human Resources Mgt.
Human Resources Management as part of the series “little production system - short and simple. Including a self evaluation check for your own organization.
In this article we want to have a short read on Human Resources Mgt. and the impact on your production system. As standard procedure in this series we first define our understanding of HRM, the targets and key elements. Further on you will get the 5 levels of fulfillment to have a self check of your organization.
Definition
The manager creates framework conditions, gives orientation and motivates the employees to fulfill their tasks independently and efficiently.
The targets:
Visions and strategies are developed and communicated
Framework conditions are created and maintained
Team building and team promotion is a continuous process
Responsibility and decision-making competences are promoted
Efficient personnel deployment is ensured
Responsible handling of (personnel) resources to achieve the company's goals
Key elements:
Corporate guidelines and objectives
Corporate culture, conflict management, error culture, dispute culture
Management structure / management span
Flexibility, personal responsibility, social competence
Communication and trust
On-site presence of the manager
Compliance with standards
Employee selection and deployment
Teamwork
Decentralized decision-making authority within the framework of agreed rules
Recognition
Role model function (personal conduct and appearance)
KPI
Degree of target achievement - employee satisfaction
Self assessing the levels of fulfillment for your human resources management in your organization.
Goal oriented management structure
Level 1
Responsibility and decision-making powers are not regulated. Arbitrary decision-making processes. Employees are not involved.
Level 2
Responsibility is regulated. Decision-making competence is not regulated. Bureaucratic decision-making processes. Employees are asked about the decision-making process on a case-by-case basis.
Level 3
Responsibility and decision-making powers are regulated. Simplified decision-making processes in daily business. Employees / teams are involved on a case-by-case basis in the preparation of the decision-making processes relevant to them.
Level 4
Responsibility and decision-making powers are regulated and coordinated. Bureaucratic decision-making processes are limited to "high-quality" procedures. Employees / teams are involved in the decision-making processes relevant to them.
Level 5
Responsibility and decision-making competence are in balance. Unbureaucratic decision-making processes. Employees/teams are involved in the decision-making processes relevant to them or make decisions on their own responsibility.
Management, management culture, demands on the management level
Level 1
Differently practiced management styles available. Authoritarian leadership behavior more pronounced - "I have everything under control". Executives have high professional competence and are the "firemen" of the factory/unit.
Level 2
Management guidelines are formulated and are lived very differently. The managers work in cross-divisional projects for system development and design. They develop processes for their employees but cannot yet "let go".
Level 3
Uniform management guidelines are beginning to live. Management development programs support the new leadership roles. They encourage employees to bring in ideas for improvement, jointly draw up new standards and ensure that they are consistently adhered to. They bear responsibility for costs and budgets in their area and make consistent personnel decisions.
Level 4
Managers spend the majority of their working time on system development and on supporting and developing their employees and teams on site. Daily business is delegated. The manager trusts in the abilities of the employees and promotes them systematically, rewards efforts, supports improvements and agrees on Targets. Promotes, demands and trains the Identify and eliminate of waste. They become a leader methodologically assessed and developed.
Level 5
The manager is an "entrepreneur" for his or her area and designs a corporate culture in accordance with the company's guidelines. The Managers possess technical, social and methodological competence and use their scope for action and design. This can be seen, for example, in the promotion of employee/team initiatives and responsibility, agreeing on goals and this includes: increasing the cost of achieving objectives, determining the consequences of deviations (+/-), monitoring compliance with established standards, maintaining uncomplicated, open and honest communication in daily work, acting and acting in an exemplary manner, recognizing and using conflicts and contradictions, communicating visions and initiating innovations.
Human resource management level of fulfillment
Level 1
Planning, selection, deployment and control of personnel takes place at short notice on call.
Level 2
Planning, selection, deployment and control of personnel only takes place on a divisional basis.
Level 3
The planning, selection, deployment and control of personnel takes place across all divisions.
Level 4
Generally applicable rules for the planning, selection, deployment and control of personnel are applied.
Level 5
There is a future-oriented and long-term personnel management system with the components demand-oriented (quantity, quality) personnel planning procurement and deployment according to requirements qualification and development program exploitation of the qualification potential in the entire company. Formation of functional and efficient teams.
Supporting Processes
The supporting processes (SP) provide services and material goods as a necessary prerequisite for all business processes.
Within the frame work of the series the “small production system” we have a look at the supporting processes. As usual we keep it short and to the point.
Definition
The support processes (SP) provide services and material goods as a necessary prerequisite for all business processes.
Note: Within the framework of the small production system, the SP are mainly considered in relation to value creation (e.g. service of operating resources, controlling, finance, manufacturing technology, IT, quality assurance, factory service, logistics, work preparation, purchasing, productive/unproductive material).
The targets:
The value chain is designed in such a way that a minimum of support is necessary
Optimum benefit for the value-adding process is guaranteed
Synergies between the value-adding processes and the SP are established
Specific technical know-how is available for the value-adding process.
The value-adding process is relieved by the provision of the basic supply
Legal framework conditions are conveyed to the operator and adhered by him.
Key elements:
Transparency of the process
Activity allocation
Forms of cooperation
Adherence to delivery dates, speed/responsiveness
Customer/supplier relationship
Creation of synergies
Provision of specialist know-how
Reduction of the SP effort
Economic efficiency
Development towards competitiveness
Levels of fulfillment – Transparence of processes
Level 1
Simply no transparency. Performance specifications. Catalogues of services. Process description. Lack of understanding for the necessity of benchmarking.
Level 2
Performance specifications are available. No clear structures that allow external benchmarking. Necessity for benchmarking is universally recognized.
Level 3
Service catalogues are available. Cost allocation to individual processes is given. Partial benchmarking for services and material goods
Level 4
Process sequences are documented. Costs for the entire process flow are available. Structures for benchmarking have been created. Benchmarking is increasingly applied, findings are used to optimize the processes
Level 5
Process sequences are documented and are continuously updated. External benchmarking and the resulting optimization is a continuous process.
Cost allocation
Level 1
Allocation of costs. No cost transparency.
Level 2
Cost allocation according to expenditure. Disclosure of the monopolists' cost structures.
Level 3
Budgets via service level agreements with agreed targets.
Level 4
Service agreements with performance-based billing.
Level 5
Cost allocation on the basis of optimal processes.
Forms of cooperation
Level 1
The customer "pushes" the supporting processes.
Level 2
SP and customer approach each other as required.
Level 3
Regular comparison of activities between customer and SP.
Level 4
Planning of medium and long-term activities with common objectives.
Level 5
Synchronous, cooperative problem solving and meeting deadlines.
Adherence to delivery dates – delivery on schedule
Level 1
Delivery dates are not binding and are usually not kept.
Level 2
Delivery dates are agreed, but sometimes not met.
Level 3
Delivery dates are met. The customer will be informed in the event of a delay. The improvement of the adherence to delivery dates is continuously checked by means of key figures.
Level 4
Targets for adherence to delivery dates are agreed upon between customers and suppliers.
Level 5
Complete fulfillment to agreed customer delivery dates in 100% conforming parts.
Implementation speed
Level 1
The SP is judged by the customer to be too slow.
Level 2
Measures to improve the speed of implementation have been introduced.
Level 3
The customer increasingly feels that the implementation speed is appropriate.
Level 4
Confirmation of purchasing order in case of problems, feedback of responsibility, activities and deadlines are carried out within agreed time intervals. The customer is satisfied with the implementation speed.
Level 5
Preventive solutions for occurring problems have been developed. The service provider can act directly
Customer-supplier relationship
Level 1
Case-related statements of displeasure of the customer. No apparent reaction from the service providers. Responsibilities and processes of the service providers are not clear at first glance.
Level 2
General customer satisfaction surveys are carried out sporadically. Service providers react to deficits in customer satisfaction. Contact persons for service providers are defined and known.
Level 3
General customer satisfaction surveys are conducted regularly. The development of the results is visualized and leads to improvement measures. Contact persons for the SP's feel responsible.
Level 4
A balance sheet of the project progress for larger projects is standard. Measures for improvement are incorporated directly.
Level 5
The accounting is the basis for continuous improvement. Interdisciplinary teamwork is up and running.
Target Setting
Target setting and success management describes a continuous goal agreement process, which starts with the company vision and extends to the executing team or employee. Thus all employees work target-oriented on the success of the company.
Target setting and success management is crucial for the success of all companies. If you don’t know where you want to be, sooner or later you will be lost. In this article of the series “the little production system” we will have a look at the target setting and how you can evaluate it for your organization.
Definition
Target setting and success management describes a continuous target agreement process, which starts with the company vision and extends to the executing team or employee. Thus all employees work target-oriented on the success of the company.
The targets:
The formation of objectives leads to an orientation towards common process and result objectives
The contribution to the corporate targets is ensured by the creation of measurement variables and continuous control of the achievement of objectives
Every employee recognizes his or her contribution to the achievement of the company's targets and feels committed to "his or her" goal
The achievement of objectives increases motivation and willingness to improve performance
Key elements:
Company vision
Company targets
Strategic objectives
Operational objectives
Result targets / process targets
3-level voting
Interdepartmental coordination
Visualization in the responsible area
Consistent, transparent and standardized system
Freedom of action within the framework of concerted action
Dealing with deviations
Adaptation of the objectives to changing conditions (3 levels)
KPI
Degree of target achievement
Target setting and Measurements level of fulfillment
Level 4
Divisional targets are based on strategic and operational planning The goal formation process is consistent in all divisions. The process is coordinated across all divisions. Action plans are in place at divisional/cost center level to achieve the targets.
Level 5
Target agreement is carried out via 3-level coordination
Goals are coordinated across divisions
Goals are quantified
Individual goals and common goals are in harmony
There are goals for all levels up to the group or employee
At least once a year the goal formation process takes place
Measures to achieve the objectives are defined and documented
Level of fulfillment - Success management
Level 4
KPIs are available. Possibilities for success control are used. Adaptation to changed conditions is carried out in part.
Level 5
Achievement of objectives and progress are reviewed regularly
In case of deviations, corrective measures are implemented and visualized
In the event of changes in the general conditions, the goals are adjusted
Information and communication
Level 4
There is a standardized reporting system. Targets/achievement of targets are communicated and visualized in all areas/cost centers/teams.
Level 5
Visualization of goals, achievement of goals and measures
There is a standard for the confirmation (bottom up) in case of deviations (+/- )
An integrated system has been installed and is used and lived in all areas and levels
Technological Innovation
Technological innovation describes a systematic approach to securing competitiveness through new or further developed processes in production, including production-related support areas.
Within the frame work of the series the “small production system” we have a look at the supporting processes. As usual we keep it short and to the point.
Definition
Technological innovation describes a systematic approach to securing competitiveness through new or further developed processes in production, including production-related support areas.
The targets:
Each cost center plans and implements innovation and technology projects for sustainable earnings improvement. Improvements in terms of costs, product quality and delivery capability are measurable.
Solutions from technology projects have been incorporated into product developments.
Synergy from technology projects is used organization-wide. Procedures to compensate for know-how transfer are applied.
Technological leadership in core and key technologies and the associated process chains has been achieved. This leads to a positive image with customers.
Discussions with customers and suppliers (internal and external) are held regularly.
Key elements:
Technology projects
Technology budget / costs
Ideas and solutions
Strategy
Project Management
Teamwork
Organization
Influence on product development
Climate of innovation / corporate culture
Dealing with know-how
Image
Benchmark
KPI
Innovation ratio
Rank in comparison with other companies
Innovations- and Technology projects – Level of fulfillment
Level 1
Sporadic technology development projects are taking place. Only solutions for individual technological problems.
Level 2
Planning and implementation of projects not comprehensive and only in the short term. Project costs are only partially and not integral anchored in operational planning.
Level 3
Target agreements on the number of projects to be completed per area of responsibility (e.g. 1 major project, 5 small projects). Systematic implementation of innovative projects in the support processes. Organizational prerequisites for recording project costs and calculable effects have been created.
Level 4
Project costs and calculable effects are entered in the installed tracking tool. Or: Percentages of the necessary savings from innovation and technology projects are entered in the operational planning.
Level 5
Systematic planning of innovation and technology projects with anchoring in operational planning (3 years). Realization of holistic, process-oriented solutions.
Funding of innovation and technology projects
Level 1
No budget planning, no cost transparency.
Level 2
Budget available for individual projects.
Level 3
System of internal financing has been established and is mainly applied.
Level 4
Development of external sources of financing systematically followed.
Level 5
Internal and external financing for projects has been developed and is being used.
Consultants Georg Tacke and Madhavan Ramanujam offer a zero -nonsense path for successful product design. Most companies go directly from scratch towards product design. They usually don’t know whether customers want and will pay for the product until launch is done. The authors describe “nine rules” for products and services designed to meet client demands and “willingness-to-pay.”
Read more here.
Location strategy
Level 1
Individual strategies for individual optimization are sporadically recognizable. High production depth. High number of variants, high complexity costs e.g. inventories, logistics and so on. Know-how carriers individually available, no synergy regarding know-how application.
Level 2
Core technologies are defined. Individual observations underway. Unbundling of complexity through allocation to products / locations. Knowledge is available both in central offices and decentralized. Central offices organize knowledge transfer.
Level 3
Key technologies / pacemaker technologies are defined. Overall consideration of guard rails (investment strategy, employment and qualification concept) has been carried out. Rules are defined for the selection and definition of technology partners in the context of simultaneous engineering (both for in-house production and for external procurement). Creation of manufacturing networks where economically reasonable. Working groups exchange expertise.
Level 4
Consistent application of key technologies / pacemaker technologies. Consistent application of the guard rails. Investigation / determination of production locations / production networks on a platform basis for new developments. The basis for this are defined criteria such as availability of technologies, production know-how, currency influences, logistics, existing infrastructure, social and political influences. If you have a global organization: Exchange of expertise takes place in English
Level 5
All business processes are oriented towards organization wide strategic goals. Technological leadership in core and key technologies and the associated process chains has been achieved. Worldwide application and use of existing knowledge.
Project Management
Level 1
No continuous structure available
Level 2
Planning of costs, resources, milestones for individual projects is partially executed.
Level 3
Standards for project management and controlling are used. Internal and external coordination by a central office. Project decision by technology committee.
Level 4
Coordination/networking of the thematically related projects are site-related, innovation audits are implemented by the management.
Level 5
Individual projects are coordinated with the overall project landscape worldwide. Project decisions are made by the Technology Committee and Steering Committee. Production engineering in the organization.
Influence on product development
Level 1
No systematic Simultaneous Engineering.
Level 2
Simultaneous Engineering takes place on concrete tasks value analysis projects are carried out. Preliminary technological developments do not take place.
Level 3
Joint development of product and production system begins. Preliminary technological developments take place and flow into new products.
Level 4
Comprehensive joint development of product and production system is standard.
Level 5
The product development process has been halved in time (e.g. through platform developments and rapid prototyping with a target value of 2 years). Solutions from innovation and technology projects have been incorporated into product developments.
Production in Takt
Production in takt the key insights you’ll find in this chapter of our “little production system”.
Yes “Takt” - not tact. So you already learned some German ;). In this article we have a short insight on the topic production in takt. What does it mean, what are the key elements and how you can conduct a little self assessment.
Definition
Material flow in cycles describes a steady, rhythmic work, whereby the material is moved continuously and always in the same cycle. The organization required in each area is oriented to the common rhythm.
The targets:
The material flow is calmed (because synchronous)
Resources (employees and machines) are equally loaded
The production is accurate in terms of quantity and cycle and can react to fluctuations
Key elements:
Production is balanced and smoothed
Material is offered in the rhythm of the production
Work organization maintains the value-added process continuously
Consumption control
Employees qualified for the new requirements
Working time models to ensure adherence to schedules and flexibility
KPIs
Adherence to delivery dates
Fidelity
Self assessing the levels of fulfillment of production in takt.
Organization
Level 1
No standards. "Everybody does what they want."
Level 2
There are visualized standards. Value creation and supporting processes are separated. There is a pause at bottleneck machines.
Level 3
The value-adding activity at the bottleneck machine takes place continuously and without interruption.
There is a “water spider” organization for personal distribution time.
Preventive maintenance is firmly planned and is taken into account in capacity planning. Flexibility is guaranteed.
Breaks are coordinated so that no additional buffers are required at the interfaces in the process chain.
All production equipment is maintained as a preventive measure. Maintenance for bottleneck production equipment is firmly planned and is carried out in the capacity planning taken into account. All others means of production are maintained, if these are not required.
Level 4
Employees repair malfunctions themselves or organize the troubleshooting. The water spider organization is adapted to this.
You are organized that you can meet market fluctuations in the order of 15% in 3 months, 30% in 6 months.
The number of employees corresponds to the actual demand.
Level 5
The value-adding activity takes place continuously and without interruption. The team organizes itself.
Production planning
Level 1
Daily fluctuating production program, deadlines are not met.
Level 2
Production plans (assembly and pre-assembly program) exist for all production equipment, machine allocation plans, etc.).
Level 3
Balanced at product level production. Example: 800 units per Day for the next 4 Weeks. Raw material and purchased parts are used for “A” and “B” parts in consumption control procured.
Level 4
At part number level balanced and smoothed production. Production plan only for the assembly exists (except unique ones).
Level 5
Production plans can can be changed at any time. No over-/ and underproduction.
Staffing
Level 1
No planning standards.
Level 2
Personnel for order fluctuations only in framework of flex-time and voluntary overtime.
Level 3
Flexible deployment of employees, around fluctuations to compensate. Example: Employees change temporarily the cost center.
Level 4
It is regulated that employees from indirect areas in the integrated production plan. There may come standardized measures for over- and under capacity in a scheme.
Level 5
Standardized measures for over- and under capacity will be lived in the employee self-organization.
Customer Takt
Level 1
The customer takt is not known. Create unequal large buffers and stocks.
Level 2
The customer takt is known. Work systems are aligned with the customer cycle.
Level 3
Subareas are among themselves balanced according the takt.
Level 4
All optimization processes are based on the customer takt.
Level 5
The parts flow rhythmically in the customer cycle time.
5S of Organization
Learn about the basics of 5S. This article gives you a short overview of 5S, the systematic and some criteria to take an evaluation of your own organization.
5S and workplace organization. Everybody has an idea about it or at least heard once about it. We always try to keep it short so let’s start right away.
Definition
5S Workplace organization is a standardized approach to plan from scratch, maintain and improve ergonomic, standardized, clearly arranged and safe workstations and the surrounding. 5S workplace organization is the starting point and basis for the continuous improvement process (CIP) and the outcome as standards for the organization.
The targets:
The perception of waste and the resulting awareness of improvement possibilities is achieved
A fast development and implementation of improvement measures is guaranteed
Increase in productivity
Support quality targets
Key elements for this are:
Application of the 5S-modules
Ergonomics of the workstations
Compliance with occupational safety guidelines
Regular audits
Great Book - love it! If you are trying to carry out a 5S project. This book will help you.
5S is a very simple yet powerful tool ! It is the ideal tool for initiating a continuous improvement process : it requires few resources, everyone can participate and the results are visible. Thanks to its application, you will be able to improve safety, quality, performance and your working environment.
5S can be measured in 5 levels of fulfillment which we want to describe a little bit more in detail for the different areas where 5S applies.
Order and cleanliness at the work station
Level 1
Disorder, pollution. High search effort for Work equipment, material etc. Obstructed, not observable Tool cupboards/drawers. Soiled load carriers. Radios / Food at the workplace. Graffiti and pictures on the walls.
Level 2
Places for material and Work equipment defined, much still in the wrong place Place; the unnecessary is sorted out; employee has the responsibility for the cleanliness of his Workplace; Walls are clean, no pictures available.
Level 3
Everything is obvious, freely accessible and in a defined quantity on marked place. Necessary things are sorted, color-coded and sensibly arranged. Tools and devices are the workplace assigned.
Level 4
Product, process and information flow are consistent and clear for everyone recognizable. Employees maintain and improve the condition with simultaneous Reduction of the Effort.
Level 5
Everything is top condition
Order and cleanliness at the surrounding
Level 1
Soiled, untidy factory halls, hygiene rooms etc.; Soiled working clothes; Private utensils at the workplace; Soiled disposal areas, no waste separation
Level 2
Roads and footpaths are free, clean and can be used without hindrance; hygiene rooms are clean; employees use facilities for storing personal belongings; disposal areas are clean; no waste separation
Level 3
Driveways and footpaths, parking spaces etc. are marked and clearly visible. Waste is collected and disposed of separately.
Level 4
Employees wear uniform clean work clothing. Working areas are free from unused machines and equipment. Waste avoidance programs have been introduced and are lived out.
Level 5
Your plant is a showcase
Discipline and Standards
Level 1
No awareness of the need for cleaning. Desired discipline is not exemplified. No constant standard. Existing standards are partly not observed (e.g. smoking and eating at the workplace)
Level 2
Cleaning schedules are available, are only partially adhered to and not checked. Strong differences in individual areas. There is a clear management position on topics such as "smoking and eating at work".
Level 3
Standards include friction and test points for 5S. They are structured in a uniform manner throughout the factory. The existing standards are adhered to as far as possible. The initiative for maintenance is taken by managers and "key persons”.
Level 4
The employees are obviously proud of their workplace. Everyone adheres to the existing standards. Cleaning and testing activities are carried out routinely.
Level 5
All employees have internalized the 5S principles. 5S is a basic element of your corporate culture. The adherence to and improvement of standards is a matter of course - "everyone" is a role model.
In factories around the world, Toyota consistently makes the highest-quality cars with the fewest defects of any competing manufacturer, while using fewer man-hours, less on-hand inventory, and half the floor space of its competitors. The Toyota Way is the first book for a general audience that explains the management principles and business philosophy behind Toyota's worldwide reputation for quality and reliability.
Safety and work safety
Level 1
Legally required notices; protective equipment in poor condition, partially overridden or bypassed.
Level 2
Legal requirements are fulfilled. Safety inspections by authorized representatives. Safety devices and equipment are described and clearly marked. Protective clothing is provided. Requirements are visualized.
Level 3
The requirements are known to everyone. Compliance with the standards is consistently demanded. Sources of danger are identified and eliminated. Regular audits of managers and specialists.
Level 4
Potential sources of danger are consistently eliminated. Offensive, target-oriented adjustment for safety. Handling of devices, tools ... is optimized. Environmental aspects (noise, air, light, temperature ...) are taken into account.
Level 5
There are safety standards for all workplaces. Accidents and “almost” accidents are systematically reported and analysed. Regular communication of accident statistics. Audits are carried out by staff-teams. Legal requirements are exceeded.
Safety and ergonomics
Level 1
No ergonomic workplace design available (lighting, lifting equipment)
Level 2
Employees are instructed in lifting and carrying loads.
Level 3
Ergonomic aspects are reflected in the workplace design.
Level 4
Job rotation avoids constant repetition of strenuous activities. Load lifting regulations are implemented across the board.
Level 5
All workplaces and processes are designed according to ergonomic criteria. Low-cost automation reduces heavy, dirty, stressful activities
Methods of Improvement
Level 1
Cleaning actions only on "special occasions”.
Level 2
Cleaning and clean-up operations are carried out at irregular intervals.
Level 3
Selective improvement activities instead of sustainable improvement.
Level 4
CIP is "lived" by all employees.
Level 5
Standards are goal-oriented, structured and consistently developed further. Teams of employees regularly carry out self-assessments.
As you can see the methodology of 5S can be implemented everywhere. And can only be considered as done if you can answer the following questions with yes:
Are all employees in the production, logistics and in administration educated about the goals and methods of the 5S?
Are the principles of 5S applied in everyday work and being further developed?
Is the continuance of 5S controlled within the framework of regular audits?
Is the 5S audit system is in place and regularly used by persons responsible for audits?
Is the cycle connected with problem solving methods and responsible persons actively observe the defined measures?
Stay connnected











Ad
We want information fast and in a nutshell. We from OI recommend Blinkist* - because it’s simply the best.
* = Affiliate Link