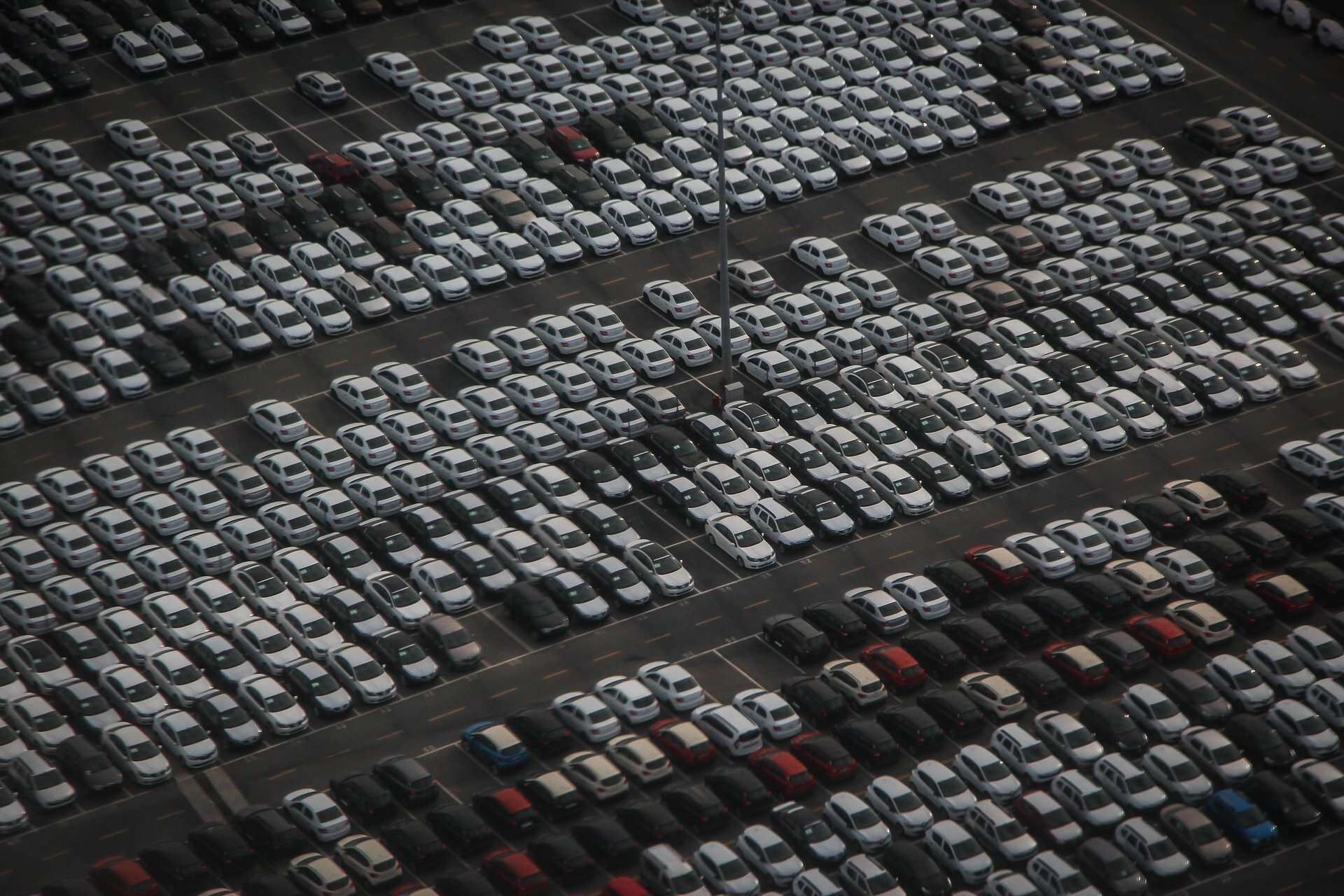
LITTLE PRODUCTION SYSTEM
One Piece Flow
One Piece Flow as key component of the “little production system” series.
One Piece Flow - every one living a life in production comes across this topic at least once per day. Either in the planning phase of an assembly line or fighting daily capacity issues. Let’s have a short look insight this topic.
Definition
In flow production, machines and workstations are arranged in this way, that the material is transported by the shortest route and the workpiece flows through the process chain.
The targets:
Movements and transports take place as the crow flies
Downtimes and stocks are avoided
The processing times are reduced
Key elements:
The material flow is free of crossings
Clear, visualized material flow
Installations are arranged in the order of operations and can be insert fast and flexible into a new process layout
Machines are close together and connected by slides and rolls, the investment calculation is done in process chain analysis
Key Performance Indicators (KPIs)
Lead time
Stock value
Turnover rate
Distances
Self assessing the levels of fulfillment according one piece flow.
Assess Your Layout concerning one piece flow
Level 1
Functional arrangement in a workshop production.
E.g. islands of processing: soft machining, hardening, hard machining and assembly are locally separated areas.
Tools and equipments are stored where space is available.
Level 2
Concept for material flow oriented layout is available.
Pilot projects / pilot process chains have been implemented.
Level 3
Machines are material flow oriented (e.g. in U-shape).
Consistent responsibility for soft and hard machining.
Pre-assembly or processing shops are service providers.
The most important operating resources for “A” parts are on site.
First production-related support services (service, operating resources, measuring technology) are installed on site.
Level 4
Machines are so close together that there is no room for buffers between the machines.
The one piece flow is optimally enabled.
The entire process chain is arranged in a U-shape or a comparable material flow-optimized form (fishbone form).
A technological leap in pre-assembly processes is required to integrate the processes into the U-shape.
Level 5
Optimized factory layout. Assembly and in-house production are spatially combined.
All necessary production-related support services (service, operating resources, measuring technology) are installed on site.
Production in Takt
Production in takt the key insights you’ll find in this chapter of our “little production system”.
Yes “Takt” - not tact. So you already learned some German ;). In this article we have a short insight on the topic production in takt. What does it mean, what are the key elements and how you can conduct a little self assessment.
Definition
Material flow in cycles describes a steady, rhythmic work, whereby the material is moved continuously and always in the same cycle. The organization required in each area is oriented to the common rhythm.
The targets:
The material flow is calmed (because synchronous)
Resources (employees and machines) are equally loaded
The production is accurate in terms of quantity and cycle and can react to fluctuations
Key elements:
Production is balanced and smoothed
Material is offered in the rhythm of the production
Work organization maintains the value-added process continuously
Consumption control
Employees qualified for the new requirements
Working time models to ensure adherence to schedules and flexibility
KPIs
Adherence to delivery dates
Fidelity
Self assessing the levels of fulfillment of production in takt.
Organization
Level 1
No standards. "Everybody does what they want."
Level 2
There are visualized standards. Value creation and supporting processes are separated. There is a pause at bottleneck machines.
Level 3
The value-adding activity at the bottleneck machine takes place continuously and without interruption.
There is a “water spider” organization for personal distribution time.
Preventive maintenance is firmly planned and is taken into account in capacity planning. Flexibility is guaranteed.
Breaks are coordinated so that no additional buffers are required at the interfaces in the process chain.
All production equipment is maintained as a preventive measure. Maintenance for bottleneck production equipment is firmly planned and is carried out in the capacity planning taken into account. All others means of production are maintained, if these are not required.
Level 4
Employees repair malfunctions themselves or organize the troubleshooting. The water spider organization is adapted to this.
You are organized that you can meet market fluctuations in the order of 15% in 3 months, 30% in 6 months.
The number of employees corresponds to the actual demand.
Level 5
The value-adding activity takes place continuously and without interruption. The team organizes itself.
Production planning
Level 1
Daily fluctuating production program, deadlines are not met.
Level 2
Production plans (assembly and pre-assembly program) exist for all production equipment, machine allocation plans, etc.).
Level 3
Balanced at product level production. Example: 800 units per Day for the next 4 Weeks. Raw material and purchased parts are used for “A” and “B” parts in consumption control procured.
Level 4
At part number level balanced and smoothed production. Production plan only for the assembly exists (except unique ones).
Level 5
Production plans can can be changed at any time. No over-/ and underproduction.
Staffing
Level 1
No planning standards.
Level 2
Personnel for order fluctuations only in framework of flex-time and voluntary overtime.
Level 3
Flexible deployment of employees, around fluctuations to compensate. Example: Employees change temporarily the cost center.
Level 4
It is regulated that employees from indirect areas in the integrated production plan. There may come standardized measures for over- and under capacity in a scheme.
Level 5
Standardized measures for over- and under capacity will be lived in the employee self-organization.
Customer Takt
Level 1
The customer takt is not known. Create unequal large buffers and stocks.
Level 2
The customer takt is known. Work systems are aligned with the customer cycle.
Level 3
Subareas are among themselves balanced according the takt.
Level 4
All optimization processes are based on the customer takt.
Level 5
The parts flow rhythmically in the customer cycle time.
Stay connnected











Ad
We want information fast and in a nutshell. We from OI recommend Blinkist* - because it’s simply the best.
* = Affiliate Link