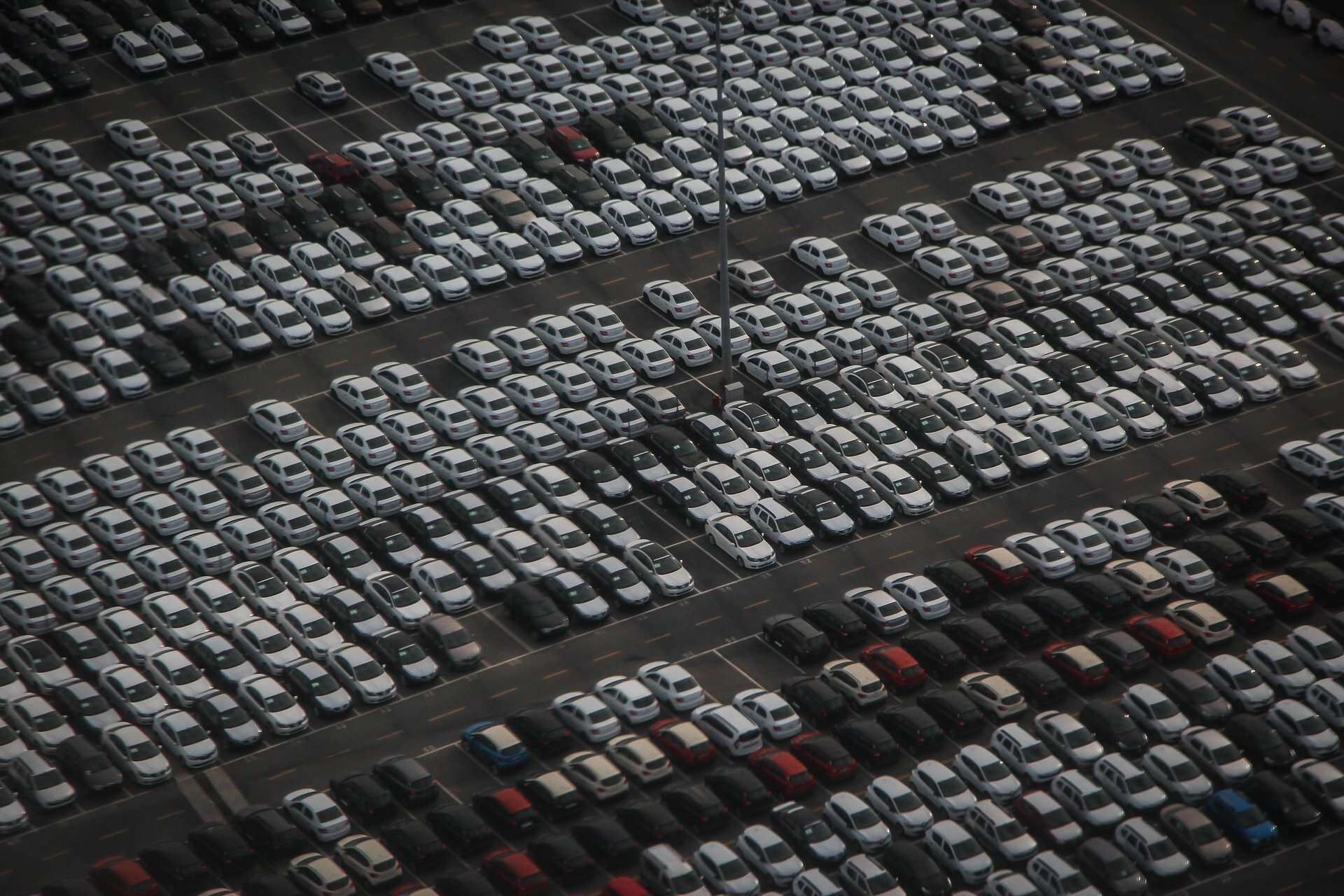
LITTLE PRODUCTION SYSTEM
One Piece Flow
One Piece Flow as key component of the “little production system” series.
One Piece Flow - every one living a life in production comes across this topic at least once per day. Either in the planning phase of an assembly line or fighting daily capacity issues. Let’s have a short look insight this topic.
Definition
In flow production, machines and workstations are arranged in this way, that the material is transported by the shortest route and the workpiece flows through the process chain.
The targets:
Movements and transports take place as the crow flies
Downtimes and stocks are avoided
The processing times are reduced
Key elements:
The material flow is free of crossings
Clear, visualized material flow
Installations are arranged in the order of operations and can be insert fast and flexible into a new process layout
Machines are close together and connected by slides and rolls, the investment calculation is done in process chain analysis
Key Performance Indicators (KPIs)
Lead time
Stock value
Turnover rate
Distances
Self assessing the levels of fulfillment according one piece flow.
Assess Your Layout concerning one piece flow
Level 1
Functional arrangement in a workshop production.
E.g. islands of processing: soft machining, hardening, hard machining and assembly are locally separated areas.
Tools and equipments are stored where space is available.
Level 2
Concept for material flow oriented layout is available.
Pilot projects / pilot process chains have been implemented.
Level 3
Machines are material flow oriented (e.g. in U-shape).
Consistent responsibility for soft and hard machining.
Pre-assembly or processing shops are service providers.
The most important operating resources for “A” parts are on site.
First production-related support services (service, operating resources, measuring technology) are installed on site.
Level 4
Machines are so close together that there is no room for buffers between the machines.
The one piece flow is optimally enabled.
The entire process chain is arranged in a U-shape or a comparable material flow-optimized form (fishbone form).
A technological leap in pre-assembly processes is required to integrate the processes into the U-shape.
Level 5
Optimized factory layout. Assembly and in-house production are spatially combined.
All necessary production-related support services (service, operating resources, measuring technology) are installed on site.
Stay connnected











Ad
We want information fast and in a nutshell. We from OI recommend Blinkist* - because it’s simply the best.
* = Affiliate Link