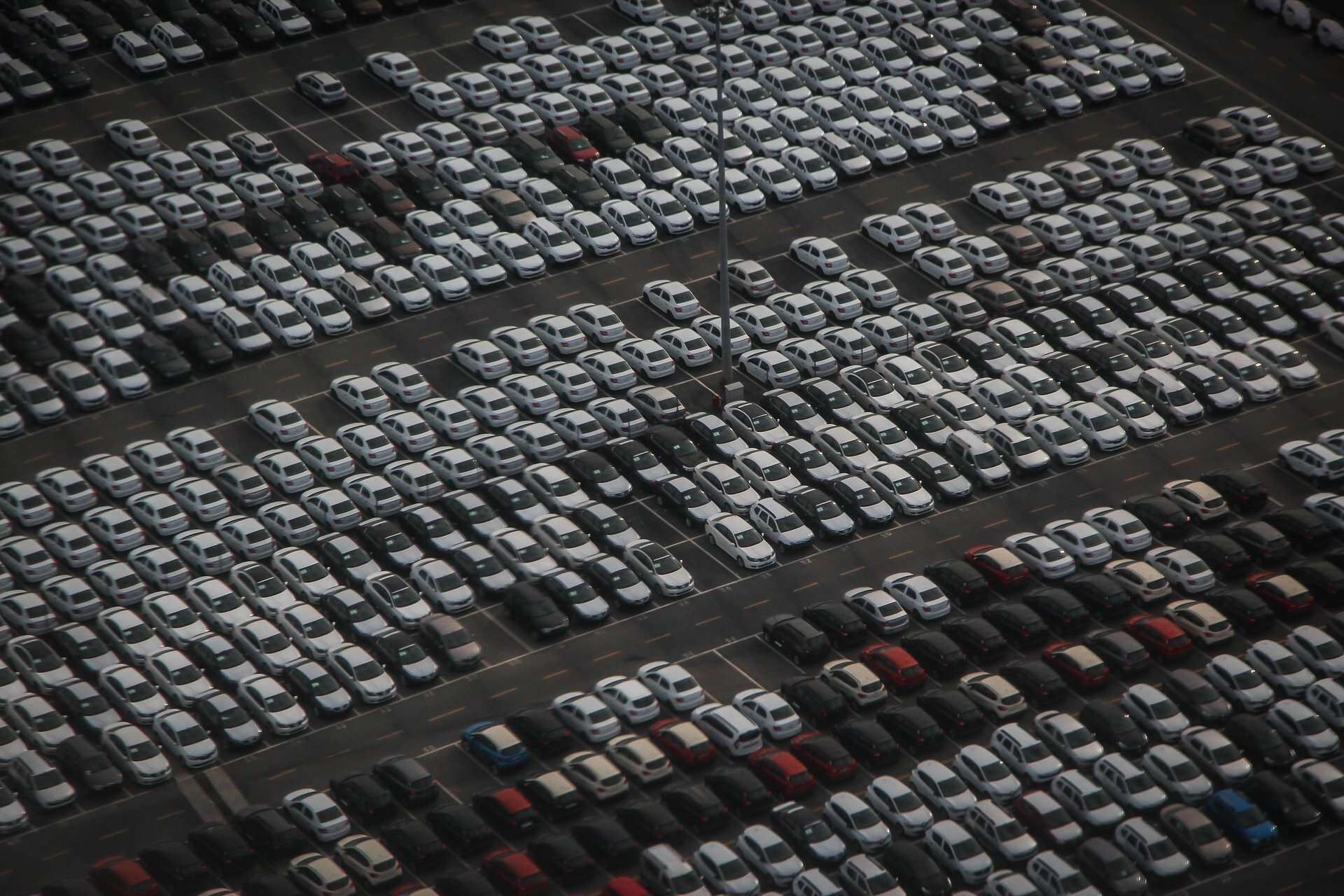
LITTLE PRODUCTION SYSTEM
Flexible Equipment
Flexible facilities are machines, equipment and installations that can be quickly and efficiently adjusted to the product-specific and logistical wishes of the internal and external customers.
In this new article in the series “little production system” we will have a view on equipments and machinery of your facility. Have fun reading and learning.
Definition
Flexible facilities are machines, equipment and installations that can be quickly and efficiently adjusted to the product-specific and logistical wishes of the internal and external customers.
The targets:
No set-up times for platform parts necessary
Customer-synchronous setup times for variant parts are realized
Decoupling of employees and device (binding factor direction 0.1) is realized
The loss of production during relocation of a flexible device is less then one shift
The flexible facilities consist of of autonomous, modular units, which can be converted or combined into production or assembly devices
Resources that are available under the flexible devices are interchangeable
In case of service and assemblies the components of flexible equipments are interchangeable in customer takt
Ensuring the customer synchronous delivery in the required quality from an economic point of view
Cost-effective solutions have advantages (low cost automation)
Key elements:
Set-up in takt
Requirements for the flexible operation
Facilities
Product quality
Costs / economic efficiency
Relocation flexibility
Binding factor (operator / equipment)
Autonomous units
Service friendliness
Work preparation
Provision of operating resources; supply and disposal
Manufacturing strategy by platform and variant parts
Design of devices and tools
Automation (low cost automation)
Key Performance Indicators (KPI)
Setup times
Binding factor
Moving time
Self assessing the levels of fulfillment according flexible equipment
Assess your set-up procedure - set up in takt
Level 1
Planned times are available, but not related to is-time. Setup sequence and duration are always different.
Level 2
Set-up analyses on bottleneck stations and nominal/actual comparisons are partially carried out. Setup times are reduced by setup preparation during machining and first piece inspection. There are setup standards for individual facilities.
Level 3
At all “A” facilities are set-up standards. Systems for fast Set-ups are developed and in pilot areas tested. A strategy for set-up in the team is introduced.
Level 4
At all manufacturing and assembly equipments are set-up/exchange standards. At all “A/B” facilities are scaffolding systems - as far as economical - introduced. High runner lines can be exchanged in customer takt (setup time < 5 Min.). SMED (Single Minute Exchange of a Die) is realized.
Level 5
No set-up times for platform parts. Customer-synchronous set-up times for variant parts. First piece quality without readjustment and test runs. Standardization of:
Facilities /Assemblies
Resources
Work processes (e.g. set-up, process chain).
All factories have problems, writes manufacturing executive Rob Tracy. Sooner or later, your plant will fall behind in on-time delivery, your workforce will lose morale and the production calendar will fill up with emergency “hot list” scheduling. Tracy points out that getting a factory back in shape may be hard, but it’s not complicated. He explains step-by-step how to identify weaknesses, set attainable goals, get the cooperation of the whole organization and make improvements that last.
Read more here.
Requirements for the operation of flexible equipment
Level 1
There are specialists for every equipment.
Level 2
Individual operators can operate several devices.
Level 3
Individual operators can operate and set-up several devices. A concept for the standardization of control panels has been developed.
Level 4
Individual operators can operate several devices. The standardization of the control panels for A-installations has been implemented.
Level 5
Extensive decoupling of operator and equipment. The standardization of the control panels has been implemented in all facilities.
Levels of product quality
Level 1
No process capability, therefore 100% testing.
Level 2
Partial process capability for final processes. Predominantly 100% testing for final processes. Machine capability is a criteria for new purchases.
Level 3
Process capability at all “A” equipments. Targeted measures (e.g. investments / tolerance defusing) to achieve process capability.
Level 4
Process capability on all “A/B” equipments. Targeted measures (e.g. investments/tolerance defusing) to achieve process capability.
Level 5
On all “A/B” machines CpK > 1.66 (no more random checks). Annual PPM halving on all “A/B” machines.
Costs and economic efficiency
Level 1
Cost allocation is inadequate. Cost accounting is not transparent.
Level 2
Cost accounting for individual processes is realized.
Level 3
Cost accounting for individual processes and direct support processes is implemented (-> extended profitability analysis).
Level 4
Cost accounting for individual processes, direct and indirect support processes is implemented (-> extended profitability analysis).
Level 5
Process cost accounting is realized.
Relocation flexibility
Level 1
Fixed, rigid facilities. There are sometimes no or only individual interfaces at the facilities (inside / peripheral). There are no connecting elements.
Level 2
Expenses for moving is high (10.000 EUR). Duration of the move is long (approx. 5 days). There are partly standardized fasteners. There is partly a supply grid for electrics.
Level 3
Relocation is more flexible due to standardized procedure (costs <7.500 EUR, takes about 2 days). There are technical standards for ...
Interfaces
Fasteners
Supply voltage
Network connection
Cooling and lubricating oil
etc.
“A” facilities are retrofitted - if economical.
New equipment is procured on the basis of the established standards.
Level 4
In the case of new buildings and conversions, grids for supply and disposal facilities have been implemented. “A-/B” facilities are - as far as economically feasible - designed to the specified standards retrofitted. A move costs < 5.000 EUR and takes about 1 day. New facilities do not require special foundations.
Level 5
The relocation of flexible facilities is realized in about 0.5 days.
Binding factor (operator/equipment)
Level 1
High runner line – 1,0
Small batch production: unplanned
Assembly: According to cycle compensation time in the assembly cycle
Level 2
High runner line – 0,8
Small batch production: planned for A-equipment
Assembly: Target: Tact compensation time goes towards 0
Level 3
High runner line – 0,5
Small batch production: planned for A- and B-equipment
Assembly: ongoing optimization
Level 4
High runner line – 0,3
Small batch production: C equipments have the binding factor of 0.0
Assembly: ongoing optimization
Level 5
High runner line – 0,1
Small batch production: ongoing optimization
Assembly: ongoing optimization
Autonomous units
Level 1
Rigid linking and integration of the units to form facilities (e.g. transfer lines, special machines, assembly lines). The functions of the equipment are constantly monitored by operators.
Level 2
High degree of electrical / mechanical linkage between the units and equipment. Pilot projects for unattended breaks have been implemented. “A” facilities are improved so that a customer takt can be produced without operator supervision.
Level 3
Depending on the situation, “A” equipment can be operated without automation and integrated additional equipment. “A” facilities run through during the breaks. In case of malfunctions, the equipment switches off automatically. End of cycle and malfunctions are indicated by optical and acoustic signals.
Level 4
Depending on the situation, “A/B” equipment can be operated without automation and integrated additional equipment. “A/B” equipment runs through during the breaks.
Level 5
Autonomous, modular units that can be combined as required to form production/assembly facilities.
Service friendliness
Level 1
Equipment is only repaired by specialists.
Level 2
Assemblies and components of the equipment are gradually being standardized.
Level 3
The quick exchange of assemblies and components is designed and tested in pilot cases.
Level 4
The quick exchange of assemblies and components is implemented for “A/B” installations.
Level 5
Assemblies and components can be exchanged in customer takt.
Work preparation
Level 1
Equipment is planned and procured by specialists.
Level 2
Workflow planning, work and time studies, NC programming, fixture and tool design, etc. by specialists. Selection and implementation of workshop-oriented NC programming systems.
Level 3
Planning and procurement of equipment with the involvement of all affected employees. First in-house developments of simple devices and creation of simple NC programs by the operator.
Level 4
Operators are involved in the work preparation and know the main and supporting processes. Operators are qualified to independently develop simple devices and tools and to create NC programs.
Level 5
Work preparation in the island team under consideration of the process chain. Operators independently develop simple operating equipment (low cost automation) and create NC programs.
Provision of operating resources, supply and disposal
Level 1
Central supply of resources and tool presetting. Central supply and disposal.
Level
Frequently used devices and tools are stored on the island.
Level 3
Devices for high runner parts are located decentrally in the immediate vicinity of the equipment. Decentralized tool dispensing systems have been developed and introduced in pilot cases. An emergency plan has been drawn up for the failure of central supply and disposal units.
Level 4
New operating resource supply concepts have been developed and tested in pilot cases for facilities that produce on demand. The flexibility of the equipment is supported by tool removal systems. The emergency concept for the central supply and disposal units has been implemented. Emergency plans have been drawn up for the individual areas.
Level 5
Equipment supply concepts for demand-driven equipment have been introduced. Production is ensured even if central supply and disposal units fail.
Manufacturing strategy by platform parts and variant parts
Level 1
No clear difference in demand-oriented control.
Level 2
Partial families formed as standard for...
High runner lines (consumption-controlled)
Residual production (demand-driven).
Level 3
The machine park is divided into high runner lines and remaining production.
Level 4
Platform parts and "One-Piece-Flow" for variant parts implemented.
Level 5
Limited "flexibility" with standard machine for platform parts. High "flexibility" (complete machining) for variant parts.
Design of devices and tools
Level 1
Devices and tools are designed for individual positions.
Level 2
Devices and tools are designed for families of parts and for one process.
Level 3
Devices and tools are designed for families of parts and for several processes.
Level 4
25 % of the jigs / tools are interchangeable among the equipment in the process chain.
Level 5
50 % of the jigs / tools are interchangeable among the equipment in the process chain.
Automation
Level 1
All variants up to the highest degree of automation available.
Level 2
Individual process-related automation is available, buffer size approx. 0.5 hours.
Level 3
30 % of the high runner lines are equipped with low cost automation. In small-batch production, automation adapted to the overall problem has been investigated and, where appropriate, implemented to 30 %.
Level 4
60 % of the high runner lines are equipped with low cost automation. In small-batch production, automation adapted to the overall problem has been investigated and, where appropriate, implemented to 60 %.
Level 5
100 % of the racing lines are equipped with low cost automation. In small-batch production, automation adapted to the overall problem is examined and, where appropriate, implemented 100%.
One Piece Flow
One Piece Flow as key component of the “little production system” series.
One Piece Flow - every one living a life in production comes across this topic at least once per day. Either in the planning phase of an assembly line or fighting daily capacity issues. Let’s have a short look insight this topic.
Definition
In flow production, machines and workstations are arranged in this way, that the material is transported by the shortest route and the workpiece flows through the process chain.
The targets:
Movements and transports take place as the crow flies
Downtimes and stocks are avoided
The processing times are reduced
Key elements:
The material flow is free of crossings
Clear, visualized material flow
Installations are arranged in the order of operations and can be insert fast and flexible into a new process layout
Machines are close together and connected by slides and rolls, the investment calculation is done in process chain analysis
Key Performance Indicators (KPIs)
Lead time
Stock value
Turnover rate
Distances
Self assessing the levels of fulfillment according one piece flow.
Assess Your Layout concerning one piece flow
Level 1
Functional arrangement in a workshop production.
E.g. islands of processing: soft machining, hardening, hard machining and assembly are locally separated areas.
Tools and equipments are stored where space is available.
Level 2
Concept for material flow oriented layout is available.
Pilot projects / pilot process chains have been implemented.
Level 3
Machines are material flow oriented (e.g. in U-shape).
Consistent responsibility for soft and hard machining.
Pre-assembly or processing shops are service providers.
The most important operating resources for “A” parts are on site.
First production-related support services (service, operating resources, measuring technology) are installed on site.
Level 4
Machines are so close together that there is no room for buffers between the machines.
The one piece flow is optimally enabled.
The entire process chain is arranged in a U-shape or a comparable material flow-optimized form (fishbone form).
A technological leap in pre-assembly processes is required to integrate the processes into the U-shape.
Level 5
Optimized factory layout. Assembly and in-house production are spatially combined.
All necessary production-related support services (service, operating resources, measuring technology) are installed on site.
Material Flow
Material Flow - Pull in the best from you can get, just another part of the “little production system” series.
The means of this article in the series “little production system” we will have a short insight on material flow without buffers - or simply called pull principle.
Definition
The indicator of material flow without buffer is that only as much material is moved, as in the next step is used and can be processed. Anything beyond that is in the way and obstructed.
The targets:
Avoid overproduction
Stocks are reduced flexibility is elevated
Areas are reduced, distances are shortened
Key elements:
Material is only available on planned and visualized buffers
1 piece or 1 set is delivered by low cost automation
Consumption control / Pull - principle
Mixed transport at short intervals
The material flow is continuous
Transport containers and systems are delivered in smaller quantities and more frequent
Delivery intervals are adjusted to the cycle time
Key Performance Indicators (KPI)
Buffer area
Stock value
Logistics costs
Self assessing the levels of fulfillment of your material flow without buffers.
MICRO LEVEL of production flow
Level 1
Workshop production - Technology island
Level 2
Island production without linking the machines. Installation is flow-oriented
Level 3
In other elements (e.g. TPM, FTQ, Flexible Facilities) corresponding services are provided.
For example: Machines and equipment are in TPM level n. Flexible facilities for “A”- and “B”-parts are available.
Level 4
Upstream and downstream operations are close together, partially interlinked. Transport routes/time are used for testing, marking or washing.
Level 5
Upstream and downstream operations are moved close together and connected by chutes, roller conveyors, etc.
Documentation that should be available
Process layout; material flow without buffer, material flow in cycles and flow production
Micro level stock and buffer
Level 1
Stocks are not visualized.
Level 2
Stocks / buffers between the machines are visualized (place and quantity).
Level 3
Buffers are smaller than a daily amount.
Level 4
One-piece/set flow. Accumulating buffers as keying sequence and/or disturbances are still possible.
Level 5
One-piece/set flow. No buffer between the process steps.
Micro level transportation
Level 1
Transport of the work piece carriers or base frames by handcart between the machines. Unplanned transports.
Level 2
Transport with work piece carrier or base frame in equal, fixed Quantities. No forklift as a means of transport in the field.
Level 3
There are no base frames in use. Transport is carried out with work piece carrier.
Level 4
Manual transport at working height. Uniform transfer heights avoid lifting and lowering procedures.
Level 5
Work pieces are moved from machine to machine via rollers, slides, belts. No means of transport!
Micro level material flow control
Level 1
Manual job control is carried out by specialists. Push principle! High planning and control effort. No visualization available.
Level 2
The material flow is clearly identifiable. Order control is still required. Responsibility for the control lies with the shiftleader.
Level 3
No processed work piece is discharged from the process chain. Interventions in the process chain are only necessary in the event of malfunctions.
Level 4
Only available together with level 5.
Level 5
No order control within the process chain necessary.
Macro level stock and buffers
Level 1
Buffer between the islands are larger than 1 lot (partial lots in motion).
Level 2
Lot sizes are smaller than the daily requirement for “A” and “B” parts. “A” and “B” parts no longer go into stock.
Level 3
Lot sizes correspond to the quantities per handling rack. Buffers between the islands correspond to a maximum daily requirement.
Level 4
Reduced stocks through levelled production for “A”-parts (periodically the same quantity per part number).
Level 5
A buffer (smallest quantity is 1 piece or 1 set) is permitted for control. Levelled and smoothed production for “A” and “B”-parts.
Macro level transportation
Level 1
Transport according to order. In the processing shop, workpieces are loaded from transport racks into processing racks and vice versa.
Level 2
Mixed transports at short intervals, partly still with forklift, partly already with train + trailer between the halls.
Level 3
Continuous transport system (e.g. transport train / overhead conveyor) between upstream and downstream processes. In some cases, workpieces are already placed in the downstream needed racks during the upstream process. No transports between process step I and process step II within the process chain.
Level 4
The transport containers used avoid repackaging between upstream and downstream processes. Example: Workpieces are placed directly on the finishing frame after the last pre-processing step. Uniform transfer heights avoid lifting and lowering
Level 5
Workpieces are transported in workpiece carriers or containers with standardized modular dimensions.
Macro level material flow control
Level 1
Demand-controlled batch size production. "Economic batch sizes".
Level 2
First part numbers in consumption control between assembly and last production process. Previous block formation (during material call-off, during transport, during processing, etc.) no longer applies. In the pre-assembly area, no more than two units from the same batch are processed one after the other.
Level 3
Consumption control for all “A” and “B” parts. Any part can be processed on any day. “C”-parts management for purchased parts through logistics service providers.
Level 4
Levelled production. Consistent consumption control for “A” and “B” parts throughout the entire process chain. Sequenced delivery for selected part numbers.
Level 5
Levelled and smoothed production.
Production in Takt
Production in takt the key insights you’ll find in this chapter of our “little production system”.
Yes “Takt” - not tact. So you already learned some German ;). In this article we have a short insight on the topic production in takt. What does it mean, what are the key elements and how you can conduct a little self assessment.
Definition
Material flow in cycles describes a steady, rhythmic work, whereby the material is moved continuously and always in the same cycle. The organization required in each area is oriented to the common rhythm.
The targets:
The material flow is calmed (because synchronous)
Resources (employees and machines) are equally loaded
The production is accurate in terms of quantity and cycle and can react to fluctuations
Key elements:
Production is balanced and smoothed
Material is offered in the rhythm of the production
Work organization maintains the value-added process continuously
Consumption control
Employees qualified for the new requirements
Working time models to ensure adherence to schedules and flexibility
KPIs
Adherence to delivery dates
Fidelity
Self assessing the levels of fulfillment of production in takt.
Organization
Level 1
No standards. "Everybody does what they want."
Level 2
There are visualized standards. Value creation and supporting processes are separated. There is a pause at bottleneck machines.
Level 3
The value-adding activity at the bottleneck machine takes place continuously and without interruption.
There is a “water spider” organization for personal distribution time.
Preventive maintenance is firmly planned and is taken into account in capacity planning. Flexibility is guaranteed.
Breaks are coordinated so that no additional buffers are required at the interfaces in the process chain.
All production equipment is maintained as a preventive measure. Maintenance for bottleneck production equipment is firmly planned and is carried out in the capacity planning taken into account. All others means of production are maintained, if these are not required.
Level 4
Employees repair malfunctions themselves or organize the troubleshooting. The water spider organization is adapted to this.
You are organized that you can meet market fluctuations in the order of 15% in 3 months, 30% in 6 months.
The number of employees corresponds to the actual demand.
Level 5
The value-adding activity takes place continuously and without interruption. The team organizes itself.
Production planning
Level 1
Daily fluctuating production program, deadlines are not met.
Level 2
Production plans (assembly and pre-assembly program) exist for all production equipment, machine allocation plans, etc.).
Level 3
Balanced at product level production. Example: 800 units per Day for the next 4 Weeks. Raw material and purchased parts are used for “A” and “B” parts in consumption control procured.
Level 4
At part number level balanced and smoothed production. Production plan only for the assembly exists (except unique ones).
Level 5
Production plans can can be changed at any time. No over-/ and underproduction.
Staffing
Level 1
No planning standards.
Level 2
Personnel for order fluctuations only in framework of flex-time and voluntary overtime.
Level 3
Flexible deployment of employees, around fluctuations to compensate. Example: Employees change temporarily the cost center.
Level 4
It is regulated that employees from indirect areas in the integrated production plan. There may come standardized measures for over- and under capacity in a scheme.
Level 5
Standardized measures for over- and under capacity will be lived in the employee self-organization.
Customer Takt
Level 1
The customer takt is not known. Create unequal large buffers and stocks.
Level 2
The customer takt is known. Work systems are aligned with the customer cycle.
Level 3
Subareas are among themselves balanced according the takt.
Level 4
All optimization processes are based on the customer takt.
Level 5
The parts flow rhythmically in the customer cycle time.
Stay connnected











Ad
We want information fast and in a nutshell. We from OI recommend Blinkist* - because it’s simply the best.
* = Affiliate Link