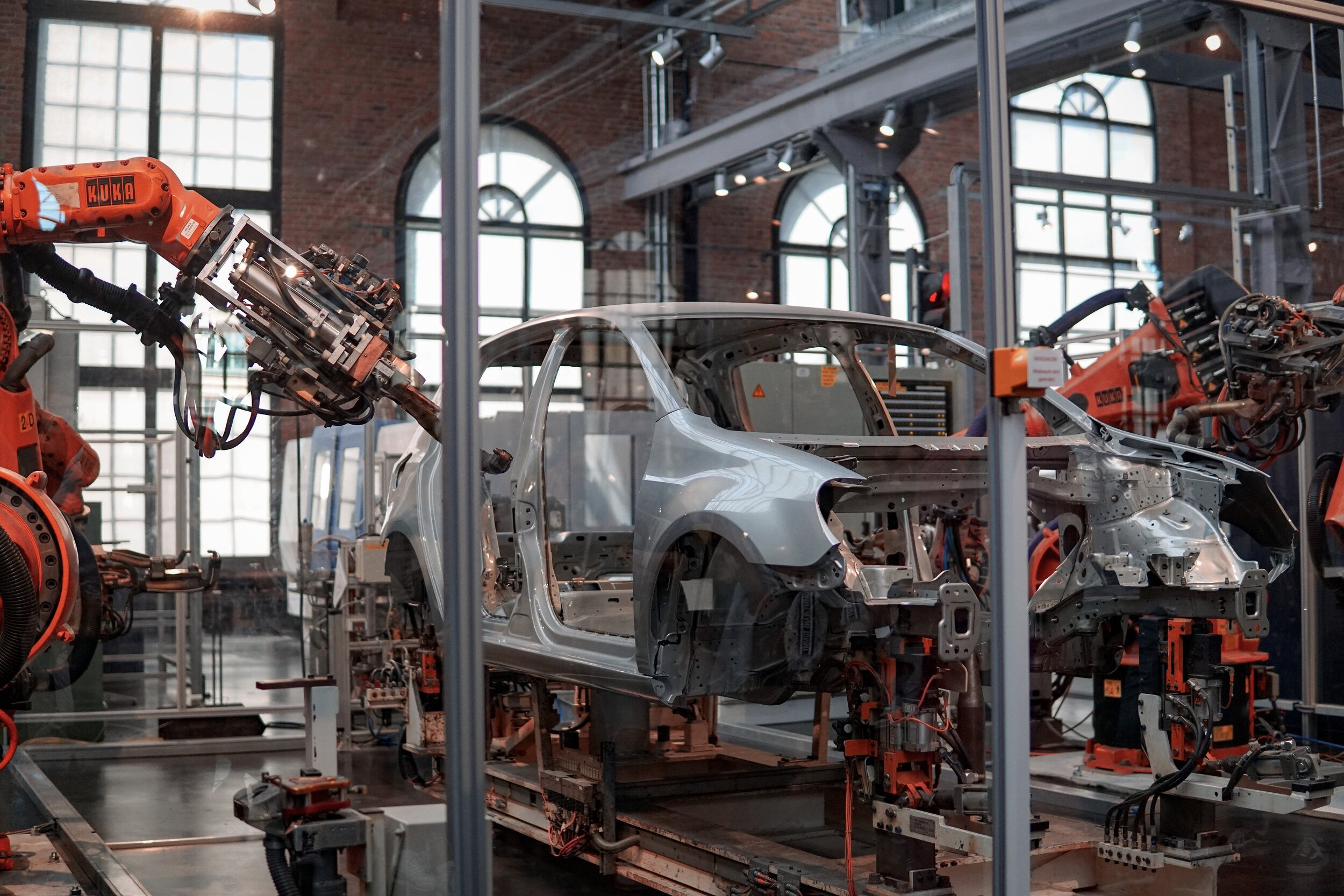
LANGUAGE OF LEAN
Pacemaker
"Pacemaker" is a term commonly used in the manufacturing industry to describe a production process that sets the pace for the rest of the production line. Sometimes also considered as bottleneck station.
"Pacemaker" is a term commonly used in the manufacturing industry to describe a production process that sets the pace for the rest of the production line. A pacemaker process is the one that determines the speed and flow of the entire production process, and therefore has a significant impact on the efficiency and productivity of the manufacturing operation. As a Lean Management Expert, it is important to understand the role and significance of a pacemaker in manufacturing, and how to effectively implement this principle for maximum efficiency and profitability.
The concept of a pacemaker process has its roots in the Toyota Production System (TPS), which is the foundation of the Lean Manufacturing philosophy. TPS emphasizes the importance of flow and standardization in manufacturing, and the pacemaker process is a key component in achieving these goals. The pacemaker process is the first step in the production line and sets the standard for the rest of the processes to follow. This means that the pace, efficiency, and quality of the pacemaker process have a direct impact on the entire production line.
In order to effectively implement the pacemaker principle, it is important to carefully select the appropriate process to serve as the pacemaker. This process should be stable, consistent, and capable of producing high-quality products in a timely manner. It is also important to standardize the pacemaker process to ensure that it runs smoothly and consistently, and that the production line can respond to changes in demand or other factors.
Once the pacemaker process has been established, it is important to monitor and measure its performance regularly. This can be done through the use of Key Performance Indicators (KPIs), such as cycle time, quality rate, and productivity. By monitoring these KPIs, it is possible to identify areas for improvement and to make changes to the pacemaker process or the rest of the production line to improve overall efficiency.
In addition to setting the pace for the production line, a pacemaker process can also have a positive impact on the morale of the manufacturing workforce. When employees see that their efforts are making a significant impact on the overall efficiency and success of the operation, they are more likely to be motivated and engaged in their work.
In a nutshell, the pacemaker principle is a key component of the Lean Manufacturing philosophy, and a valuable tool for Lean Management Experts looking to improve the efficiency and profitability of their manufacturing operations. By carefully selecting the pacemaker process, standardizing its performance, monitoring its performance regularly, and using KPIs to track progress, it is possible to achieve maximum efficiency and profitability in the manufacturing industry.
Zero Defects
Zero Defects, also known as "Zero Quality Control" or "ZQC," is a quality improvement philosophy that seeks to eliminate defects in the production process.
In other projects we have witnessed the significant impact that Zero Defects programs can have on a manufacturing organization. Zero Defects, also known as "Zero Quality Control" or "ZQC," is a quality improvement philosophy that seeks to eliminate defects in the production process. This philosophy has its roots in the Total Quality Management (TQM) movement and has been widely adopted by many manufacturing organizations.
The Zero Defects philosophy is based on the belief that quality should be built into every product, from start to finish. The goal is to eliminate defects and ensure that products are produced to the highest standard, meeting or exceeding customer expectations. This approach to quality focuses on the entire production process, from raw materials to finished goods, and encourages all employees to be actively involved in the quest for zero defects.
One of the key benefits of a Zero Defects program is that it helps to create a culture of continuous improvement. Employees are encouraged to identify areas where defects are occurring, and to work together to eliminate these issues. This creates a sense of ownership and engagement among employees, which in turn drives improved performance and results.
Another key benefit of Zero Defects is that it reduces the costs associated with rework and product defects. Defects in the production process can lead to increased costs, such as scrap, waste, and retooling. By reducing or eliminating these costs, organizations can improve their bottom line and remain competitive in their industry.
The key to success with Zero Defects is to have a well-defined process in place. This process should start with defining the standards for each product and then identifying the critical-to-quality characteristics that must be met. From there, a detailed process map should be created that outlines the steps involved in the production process, from raw materials to finished goods. This process map should also identify the potential sources of defects and highlight the steps that need to be taken to eliminate these defects.
Once the process map is in place, the next step is to implement the Zero Defects program. This involves training employees on the Zero Defects philosophy, as well as the process map and the critical-to-quality characteristics. It is also important to provide employees with the necessary tools and resources to identify and eliminate defects. This may include things like checklists, forms, and software programs.
In addition to training and tools, it is also important to have a robust feedback and continuous improvement process in place. This can include regular quality audits, customer feedback, and employee suggestion programs. The goal of these programs is to identify areas where defects are occurring, and to work together to eliminate these issues.
Finally, it is important to track progress and measure success. This can be done by tracking key performance indicators (KPIs), such as the number of defects, scrap rates, and customer satisfaction levels. By tracking these KPIs, organizations can determine whether their Zero Defects program is having a positive impact and make adjustments as needed.
In conclusion, Zero Defects is a powerful tool for organizations looking to improve the quality of their products and processes. By eliminating defects, organizations can improve customer satisfaction, reduce costs, and remain competitive in their industry. The key to success with Zero Defects is to have a well-defined process in place, and to actively involve employees in the quest for zero defects. By doing so, organizations can achieve operational excellence and realize their full potential.
Cell Production
Cell Production focuses on optimizing the flow of work and improving efficiency in manufacturing and operations.
Cell Production focuses on optimizing the flow of work and improving efficiency in manufacturing and operations. It is based on the concept of organizing work into cells, which are self-contained units responsible for performing a specific set of tasks. The goal of cell production is to minimize waste, increase flexibility, and improve overall performance.
The origins of cell production can be traced back to the 1950s and 60s, when Toyota and other Japanese companies were experimenting with new approaches to manufacturing. Over time, the concept of cell production has evolved and been refined, and today it is widely used in a variety of industries, including automotive, electronics, and consumer goods.
In order to implement cell production effectively, there are several key steps that organizations must take. Firstly, it is important to conduct a thorough analysis of the current state of the manufacturing or operations process, in order to identify areas where improvements can be made. This may involve mapping out the flow of work and identifying bottlenecks or other inefficiencies.
Once these areas have been identified, the next step is to reorganize the work into cells, taking into account the specific requirements of each cell and the skills and expertise of the employees who will be working in them. This may involve rearranging physical work spaces, or changing the way that work is assigned and managed.
It is also important to establish clear communication and feedback mechanisms, so that employees and teams can work together effectively. This may involve setting up regular meetings to discuss performance, or implementing systems for tracking and reporting on key metrics.
In order to ensure a successful implementation of cell production, it is also important to provide training and support for employees. This may involve providing training on the new processes and procedures, or offering coaching and mentoring to help employees develop the skills and knowledge they need to be effective.
Another key aspect of cell production is continuous improvement. This involves regularly reviewing performance and making adjustments as needed, in order to optimize efficiency and reduce waste. This may involve experimenting with different approaches, such as implementing new technologies or streamlining processes, in order to find the best solutions.
In conclusion, cell production is a powerful methodology for optimizing performance in operations and manufacturing. By reorganizing work into cells, minimizing waste, and continuously improving performance, organizations can increase efficiency, reduce costs, and improve overall performance. In order to be successful, organizations must take a structured and systematic approach, and be committed to ongoing improvement.
TPM - Total Productive Maintenance
Total Productive Maintenance (TPM) is a maintenance strategy that involves involving all employees in the maintenance process to maximize equipment productivity and minimize downtime.
Total Productive Maintenance (TPM) is a methodology that originated in Japan in the 1970s and has since become a widely recognized and adopted approach to operational excellence in manufacturing and other operations-focused industries. It is a comprehensive approach that seeks to optimize the performance of equipment and processes through a focus on maintaining and improving reliability and efficiency.
The origins of TPM can be traced back to the Japanese auto industry, where manufacturers were seeking ways to increase productivity and competitiveness in the face of increasing global competition. TPM emerged as a response to the need for a more proactive and integrated approach to equipment maintenance, with the goal of improving both productivity and overall equipment effectiveness (OEE).
Over time, TPM has evolved and expanded to encompass a wider range of objectives and activities. Today, it is widely regarded as a best-practice approach to operational excellence, and is widely used in many different industries, including manufacturing, healthcare, and government operations.
One of the key features of TPM is its focus on involving all employees in the maintenance and improvement process. This is achieved through the creation of cross-functional teams and the use of a range of techniques, including root cause analysis, standardization, and continuous improvement.
Another key aspect of TPM is its focus on data-driven decision-making and performance measurement. This involves the collection and analysis of data on equipment and process performance, which is then used to identify areas for improvement and to drive continuous improvement efforts.
When properly implemented, TPM can have a significant impact on organizational performance and competitiveness. This can include improvements in equipment reliability, increased productivity, reduced waste, and improved overall equipment effectiveness (OEE).
To achieve these benefits, it is important to implement TPM in a structured and systematic way, with clear goals and objectives and a strong focus on continuous improvement. This typically involves a multi-phased approach, starting with an assessment of existing processes and equipment, followed by the development of a comprehensive improvement plan and the implementation of specific improvement initiatives.
In a nutshell, TPM is a proven methodology that can help organizations achieve operational excellence by optimizing the performance of their equipment and processes. To achieve success, organizations must approach TPM in a systematic and structured way, with clear goals and objectives, and a strong focus on continuous improvement.
Key points for a successful TPM implementation:
Involve all employees in the process
Focus on data-driven decision-making
Adopt a multi-phased approach
Prioritize continuous improvement
Develop a comprehensive improvement plan.
Poka Yoke
Poka Yoke are all mechanisms that prevent unplanned mistakes from happening.
Poka-Yoke is any mechanism that helps to avoid unplanned mistakes. Poka-Yoke is that the application of straightforward, error-proof mechanisms to systematically avoid incorrect assembly, mix-ups or the downstream movement of defective parts. As a result of stable and high-quality methods begin long before the assembly section, simple Poka-Yoke measures will be enforced preventively within the construction and coming up with phase to make sure quality. Poka-Yoke is implemented to avoid: going away out or forgetting process steps, process or operational-related mistakes, incorrect or missing parts, setup or installation errors.
POKA YOKE ポカヨケ ("stupid mistakes - avoidance") is associate ideology that takes a spread of approaches to optimize production processes, particularly assembly. The main target of Poka-Yoke is strive for zero-defect production and to attain it approximately. If defects are detected, the cause is determined. If the cause can be avoided, it's eliminated pretty much as good as doable within the sense of Poka-Yoke and at the best doesn't occur again at all. Poka-Yoke was originally an initiative of Dr. Shingo, Shigeo (新郷 重夫), who is additionally a co-founder of the Toyota production system, of that Poka-Yoke is a core component. Poka-Yoke is beneath the umbrella of Kaizen 改善 ("continuous improvement for the better").
Poka-Yoke may be about recognizing the root causes in time and so eliminating them. Mistakes shouldn't solely be corrected, however prevented the in the longterm by eliminating their root causes. Within the ideal case, in the sense of Poka-Yoke, there are measures that utterly rule out a discovered error by eliminating the cause in the future, e.g. as a result of incorrect mounting is not any longer doable because of fixed given mounting ways (e.g. fitting shapes). Poka-Yoke demands product style ability to make a product design that forestalls errors (avoid incorrect operation) and is powerful against errors (despite incorrect operation no faulty processes). Thus the philosophy of Poka-Yoke doesn't solely begin within the production, however already in the product design.
A widely known everyday example is that the plug of the electric devices and the power outlets, that can't be inserted into the socket the incorrect way round. Measuring instruments may also be designed or programmed in such a way that they will not be misused. Poka-Yoke principles can also be found in other cases, e.g. ATMs dispense your credit card before the payout takes place. Fuel dispenser faucets solely work into the right tank for diesel or petrol, creating it tougher to refuel incorrectly. And so on.
Looking at Poka-Yoke in production "Nobody makes any mistakes" is the target of the Poka-Yoke methodology. Here a list of some mistakes that can typically be found in production:
Incorrect positioning of assembly components
Incorrect change of a die
Incorrect mounting
Wrong interpretation of directions
Incorrect polarity in electrical connections
Incorrect reading of measured values
Incorrect connection of hoses
Incorrect entries in devices
Assembly of wrong components
Skipped operations
Operation/programming errors on machines
POKA YOKE follows three simple steps
Measurement:
If you can’t measure you can’t control. Simple fixtures or sensors up to high performance camera systems can support the right execution of processes and provides feedback about the correct or incorrect task completion. Measures can be taken by cameras, mechanical, sensor for light and colors, position, vibration, voltage or temperature.
Detection of deviation:
E.g. deviations are determined by checking the amount of tasks done during one operation - has had the operator enough movement to do the job? Are enough components used? (actual-target comparison). Or simple exploitation geometric mismatches when pins or special marking at the workstation are still visible or not used.
Regulation
When deviations occur make sure that measures are taken such as pulling the ANDON CORD by the so called stop the line authority. Only when error-causing steps are cancelled out a permanent production of OK parts can be achieved.
Only when living according to the Poka-Yoke philosophy on a daily basis and following the principles of Poka-Yoke you will be able to achieve with smart automation and trained operators long term success. Root Cause Analysis and sustainable counter measurements are key. In addition each operator should be trained to detect their own faults during operation.
It might seam to be waste to train operators to detect failures, but no matter how much you planing and effort you put in design, failures occur during assembly or manufacturing. Just think about wiring that is now crossing moving components, parts where the collision was not seen during design and so on, trust me the list can be endless. Some failures will be detected with smart automation checking devices. But these are typically very costly and need special trained people to maintain and most of the time these little pieces of technology can only do one job. Here joins Poka-Yoke the game. Cost efficient, failures or incorrect assemblies can’t be passed on and each operator develops an eye for deviation.
Just keep in mind that if you have mass production or small to middle series can determine if you should install a 100% check or if simple Poka-Yokes can get you where you want.
The most important part of Poka-Yoke at all is that failures are detected when they occur and the exponentially rising costs of defective parts passed on are prevented.
8D
8D Reports are used to communicate results of taken problem solving steps to the customer in a standard format.
The so called “8D”-Report is a document resulting from an 8D process which is part of a structured problem solving process in quality management if there are quality issues between customer and supplier.
8D represents the eight mandatory process steps that are performed when processing a claim to get to the root of the cause. The report details the nature of the claim, responsibilities, and actions taken to prevent the problem from reoccurring:
The 8D methodology is intended to ensure that complaints are dealt with systematically. Consistent documentation of the associated troubleshooting steps and a high level of fact orientation ensure that errors in the product or system are thoroughly investigated and thus permanently corrected instead of just solving the problem.
Application
These eight steps are performed for the 8D report:
1 Define a team to solve the problem
A team familiar with the process and/or the product is formed. They analyze the problem, take corrective actions, and monitor the effectiveness.
2 Describe the problem
In this step, the problem is defined as precisely as possible and the root cause of the problem is identified.
3 Containment action
These measures are intended to resolve the problem quickly and limit the damage until a permanent solution is found.
4 Root cause analysis
You probably haven’t found the real root cause during step 2 therefor various tests and experiments are used during step 4 to search for the real root cause of the error and the most likely causes are identified. This is intended to ensure that similar errors do not occur again.
5 Planning of counter measures
It then determines the means by which the causes of the problem can be eliminated. It is tested whether these measures solve the problem efficiently and no undesired side effects occur.
6 Check effectiveness of counter measures
Once the corrective actions have been carried out successfully, the immediate actions must be stopped. In the automotive industry, only process-improving measures are regarded as permissible shutdown measures.
7 Prevent recurrence of error
To ensure that such an error does not happen again, the team must initiate and monitor preventive measures. In the automotive and aerospace industries, manufacturers must use the FMEA method to assess the risks identified during root cause analysis. .Also, quality management system rules and procedures may need to be adjusted.
8 Appreciation of team performance and Lessons Learned
In a last step, the achievements of the team are recognized and experiences are exchanged.
Stop the line authority
Stop the line authority describes the ability or permission of operators to stop the process when problems occur. By doing so it is prevented that defective parts are passed on the downstream process steps.
Stop the line authority describes the ability or permission of operators to stop the process when a deviation or problem occurs. By doing so it is prevented that defective parts are passed on the downstream process steps.
A typical example are so called “Andon cords“ that can be pulled to immediately stop the process and inform the supervisor. To read more about Andon itself go here.
When you are in the lean world you might have come across the famous Toyota quality control mechanism “Andon Cord”. The cord is a simple tool to alert others of deviations or problems in the production line, at Toyota everyone has the authority to pull the cord. By pulling the cord almost instantly production will stop and give the alert to responsible supervisors that there is a crucial issue that needs immediate action. Following the lean principles and shop floor structure, a supervisor would step up and help the operator reviewing the deviation of product or process and define counter measures. When doing so and working with an A3 Problem Solving approach, the supervisor is coaching through the problem solving process and shares with others the outcome or lessons learned on how to prevent this failure of happening again.
In Lean Manufacturing - pulling the Andon Cord is emphasized to all operators. The target is simply to block all defective parts from leaving the company and reaching the customer. At the same time it creates the opportunity to improve your processes to prevent future defects.
NEXT STEP: GO GEMBA
Instead of explaining you the complete principle of Gemba Walks here the short version. But if you want to learn more about Gemba Walks go here.
You can discuss problems as much as you want but when you don’t get yourself to see it, it is worthless. This is where the Gemba Walk comes in the game. Gemba is a Japanese term and stands for “the place where it actually happens”. This can be everywhere and everything in the process chain, but by pulling the Andon Cord the place is defined.
Key of Gemba is not to talk in wild theories or totally abstract about problems, but to have a look where it occurs and discuss them on site (looking at the process in the real world, get rid of unnecessary power points and excel sheets! Nobody cares anyway!) Too often we want to believe the statement of an “expert” and forget about it instead of going there and have a look ourselves in oder to gain a better understanding of the problem and make up our own opinion.
VISUALIZATION
When you are at the place of action, make sure to bring an A3 with you. Make sure that you describe the process properly and the failure that occurred.
In the lean manufacturing world the best known use case of the A3 report is the problem solving report. In this case the responsible person from the quality department takes the A3 report, starts the problem solving actions and follows a systematic structure that makes it possible to describe the effects that are currently leading to a deviation from the standard. Using the A3 only makes sense when you don’t know the root cause yet. If you already know the root cause don’t waste your time. Fix it and go back to normal.
Key Questions are with Gemba Walks and A3:
What should happen?
What is happening?
Explain why!
The A3 Report is foldable and can be then placed at the line or the work station. This is a great and a standardized tool to visualize that a problem is known and on the watch list.
LAST BUT NOT LEAST - STOP THE LINE (JIDOKA)
Now it is time to tackle the hardest part for all players in your organization: STOP THE LINE. In Lean Management, the original term is the Japanese word JIDOKA. This concept is driven by the maxim to have the best quality of goods and to bring the potentials out of the processes or products through continuous improvement. You have to stop all production when a deviation occurs and implement effective counter measures before restarting the line.
On the first view stopping the line might sound hard and insane, as you will stop all value adding activities and actually stop shipping goods. But think about it again. Failing to solve problems when they occur will force you to pile up your inventory with non-conforming parts that will need rework before shipping. You will bind additional resources in space and workers and by that you will burn money. Finally it will keep your organization away to improve and move forward with the developments of the market and with your competitors.
This is exactly the point where the principle of continuous improvement comes in the game, where you see all deviation as an opportunity of improvement.
To practice and learn more about continuous improvement and the CIP methodology, go ahead and read the CIP article here.
If you can’t measure you can’t control
Make sure that you have an organization wide monitoring in place which provides you with all KPIs necessary to run your business. Line stops and counter measures will be part of the tracking process in order to understand if the counter measures are effective, gain a better understanding of the processes and documentation of the improvement process itself.
What is the deviation?
What are the measures implement?
Are the counter measures effective?
You see there is again the logic of PDCA in the continuous improvement process.
All this information will be than part of the Shop Floor Mgmt. to get the information throughout the complete organization and to make sure that all players have the same understanding in what direction your organization is heading.
Layered Process Audit
LPA, or Layered Process Auditing, is a quality technique developed for manufacturing management.
Today we will talk about layered process audits.
LPA, or Layered Process Auditing, is a quality technique developed for manufacturing management. When used correctly, LPA brings your organization to improve quality, minimize scrap and rework, plus reduce customer rejections by driving cultural change throughout your company. To gain a better idea and to understand what LPA means we will have a little deep dive.
Layered Audits are a defined approach that devotes time and resources to ensuring that high-risk procedures and error-proofing mechanisms are consistent and functional. Therefore, three important components make up a Layered Process Auditing System:
Full focus on High Risk Processes (HRP) by a list of defined audits
Depending on layer of audit the audit itself is performed from various levels of management
A system of reporting and follow-up to ensure that containment is maintained based on specific needs. But also, to maintain and drive the continuous improvement process in your organization
A full stack of audits
This part of a Layered Process Auditing System is straightforward. Audits are merely a set of questions aimed to investigate machinery or processes. An LPA system's audits should concentrate solely on parts of the value adding process where deviation poses a high risk of producing defective products. E.g. if you have an end of the line quality check station that is measuring crucial parameters or functions that are critical to customers of your product and the calibration is wrong, you are producing in Takt defective or non-conforming products. No need to mention that you should keep an eye on that process. With the help of a proper LPA system you will have the EOL station within the layers allowing containment and corrective action as soon as the station surpasses set tolerances.
Multiple layers of audits comes with multiple layers of auditors
Multiple layers of authority from across your manufacturing department conduct audits on a regular basis, at a predetermined frequency, in an LPA system. For example, once per shift, the Shift Leader conduct an audit that checks the parameters or settings of your EOL-Station. Another layer of management, which may include process engineers, maintenance staff, or even the human resources department, would circulate through the system performing the exact same audit. The sample audit might be performed once a week or once a month by someone in the layer by assigning a number of auditors to this layer and establishing a timetable that cycles through the system's audits. Yet another layer of management, such as the plant manager or even executive staff (the number of levels in an LPA system can vary enormously from facility to facility, depending on your organizations demands and needs). This extra layer of auditors performs the same collection of audits on a rotating schedule, concluding the example audit once a month or once a quarter, for example.
Countermeasures, Containment Actions, Reporting and Improvement Process
In order to have an effective, a Layered Process Audit system you’ll have to combine analysis, measures and improvement process.
If an auditor observes a non-conformance during an audit, the auditor should not only document their findings but also take quick appropriate action to ensure that defective products do not leave the facility. In order to help with the documentation and immediate actions you can use the A3 report and methodology. Simple but effective. You can find it here. Anyway, the findings should be documented and made readily available to management for further analysis. An LPA system is a handy tool for debugging problem areas and identifying areas that are suitable for improvement actions when combined with a strong system for recording and reporting these audit results. A systematic approach will be discussed in the Shop Floor Mgmt. article.
Though Layered Process Audits may be developed to meet a customer or corporate demand, effective LPA systems are built, implemented, managed, accountable to, and owned by your participatory manufacturing management group. A solid LPA system may help you to take proactive control of your manufacturing operations while also enhancing product quality and business bottom line.
Deviation Management
Deviation mgmt. is the ability to identify any disruption to the standard work process and to implement effective counter measures on time.
Deviation Management is simply said the pure ability to identify deviation of a process according to the standard work process and you have a structured approach to tackle that issue.
5 Reasons to work with Deviation Management
Improve compliance and ownership of defective goods or processes
Continuous feedback to operators and staff of their deviations
Structured process for deviation documentation, tracking of counter measures and problem solving
Prioritization of improvement measures
Data collection to engage external suppliers and customers
Doctor Nurse Principle
The operator creating the value (doctor) receives the materials and tools from the logistics provider (nurse), so that his/her primary activity is not interrupted by secondary activities.
In the Doctor Nurse principle, the operator creating value is considered as the doctor, he receives tools and goods he needs to do his job from the nurse in this case logistics. For this reason, the doctor can’t do his job without the support of the nurse.
What can we learn from hospitals and how can we adapt it to the lean world.
In hospitals it is crucial that the doctor can fully concentrate on a surgery, the doctor is the single point of contact towards the patient using his tools combined with his training. Everything distracting him from being focused has to be eliminated. In order to give him this capability he needs assistant right next to him. The nurse’s job is to support the doctor and provide him with all equipment, tools and material he needs just in time.
Applying this principle to production is not that hard. To use the doctor nurse principle on the shop floor some requirements have to be met. As mentioned think about the operators as the doctor, they have to concentrate on production. As they are the once generating value for the whole organization by assembling the components which customer are willing to pay for – they need to be placed in the center of all activities – the rest is supportive.
In lean manufacturing this is called the line-back approach. Primary processes are the once that add value so focus on the operation and prepare everything that supports it. The nurse takes care of all other activities, most of the time non-value adding activities but necessary.
Doctor Nurse Principle
Arrange the work station in a way that gives the nurse free accessibility to the work area without disturbing the doctor, i.e. filling up kanban shelfs with new material while simultaneously removing empty boxes.
With the approach of separation of primary and secondary processes in two physical areas none of the process will be interrupted by the other.
In addition, this principle is driving the mindset of the organization to focus on a lean production process and how best it can be supported. If you do so, you will also have the advantage by separating value-adding and non-value-adding activities to find you approaches to minimize the non-value adding activities.
Another way of calling the nurse a nurse is a water spider or in lean terms a Mizusumashi – the inbound material supplier.
7 Steps - Problem Solving
The 7Steps problem solving is a standard analysis method.
The 7 Steps problem solving is an analysis method that is typically used in the 0miles major customer complaints and warranty complaints: when risk analysis is necessary. The single steps are as follows:
Problem description / risks on similar products and processes
Define containment actions
Data collection (grasping the facts / failure mode analysis)
Identify possible Root Causes
Implement corrective actions
Evaluate effectiveness (Tracking Chart)
Lessons Learned
Root Cause Analysis is one of the crucial and basic requirements in a quality system for continuous improvement. Its target is to recognize a deviation and its origins, resolve the issue so that it is not recurring and improve the quality of the product or processes. Root Cause Analysis always depends on time if you observe a deviation start asap your RCA-activities as no problem should be allowed to grow.
To gain a better understanding let us describe the 7 Steps in more details
1 Problem Description:
Capturing the deviation - Ask the following questions:
What is the problem? (symptom; use illustrations to describe as clear as possible)
Why is it a problem? (content of complaint / definition of problem statement)
Where was it detected? (location of occurrence/Area of the product or process)
When was it detected?
Who detected it?
How was it detected?
How many defective / suspect parts?
Can the problem appear on other products or processes?
Other parts
Generic parts
Opposite hand
2 Define containment actions:
Use a Tracking Chart to list your counter measures
Track how many defective parts have been detected
List in Pareto format what kind of failures have been detected
Put in containment actions and responsible person
Define when the actions have been planned and implemented
Data collection (grasping the facts / failure mode analysis) get and check the valid documentation:
1st part release
Maintenance records
Poka Yoke checks
Process parameters tracking charts
Work Instructions (SOI)
Control Plan
Drawings
Production information
Error collection sheet
First Time Through Report
Boundary sample
Ok part available
Ask the following questions:
Was it the correct process? - How should it be?
Was it the correct tool/fixture?
Was it the correct part?
Has something changed in the process?
Has something changed in the product design?
Is the process in control?
Do all product components meet quality requirements?
Collect pictures, evidences and records to support analysis.
3 Build the ISHIKAWA Diagram
List the problem to be studied in the "head of the fish".
Use an idea-generating technique (e.g., brainstorming) to identify the factors for non-conformance and non-detection within each category that may be affecting the problem and/or effect being studied.
Repeat this procedure with each factor under the category to produce sub-factors. Continue asking, "Why is this happening?" and put additional segments each factor and subsequently under each sub-factor.
Continue until you no longer get useful information
To learn more about the Ishikawa – read this article.
4 Identify the Root Cause
Analyze the results of the Ishikawa after team members agree that an adequate amount of information is provided for each major category. Do this by looking for those items that appear in more than one category. These become the “most likely causes".
For those items identified as the "most likely causes" the team should reach consensus on listing those items in priority order with the first item being the most “probable" cause. A useful method here is to allow each team member to allocate 3 points to their chosen root causes. The root cause with the most points can be taken for further analysis using 5 Why.
Once the most probable causes are drawn explain failure mechanism focusing on 2 aspects:
Cause of non-conformance
Cause of non-detection named
Use the 5 Why method for looking at the problem
5 Possible Actions
Create an action plan with countermeasures for non-conformance and non-detection to eliminate/minimize the effect
Do not forget about due dates and responsible persons (preferable only one person for one action)
6 Evaluate the effectiveness (Tracking Chart)
Put in permanent actions (+ responsibility) and make clear when the action has been planned, implemented and stopped. Track how many defect parts have been detected. After implementation of permanent actions remove containment measures only if there are no defects detected any more.
7 Lessons Learned
Visualize BEFORE and AFTER (KAIZEN REPORT)
Specify what needed to be documented (e.g. Standard Operating Instruction (SOI), etc.)
Grasp what you’ve learned (improvements in working and detection process)
Think about potential applicability in your organization (review similar design, equipment, components, processes, material or manufacturing processes).
Share what you have learned within your organization.
Some of the benefits of the Root Cause Analysis process are that you will identify which procedures will need to be changed, which documents describing those procedures will require modification and who will need to be trained or re-trained.
Finally, don’t forget that the root cause analysis process must lead to an effective corrective and preventive action plan. One without the other would mean that there is no certainty that the issue is solved and that the failure cannot reoccur.
If liked this article give it a thumbs up.
Affinity Diagram
The affinity diagram helps you to organize a large number of ideas into logical categories and natural relations.
So you have a large number of ideas and need to organize them. The affinity diagram is the perfect fit to get the job done and to structure your ideas into their natural relationships. Basically the affinity diagram describes a structured outcome from a brainstorm session. You can use it to generate, organize and consolidate information related to a product or process, complex issues or different problems. After the brainstorming session you should group the ides according to their affinity or similarity. This idea creation method was created in the 1960s by Japanese anthropologist Jiro Kawakita.
When should you use an Affinity Diagram
The typical use of an Affinity Diagram is when you are confronted with many influences or ideas in a state of chaos. Sometimes a problem seems too large or just too complex to understand it at first sight. Or you simply want that the whole team has a common understanding of a topic.
Usually you are confronted with this situation:
After a brainstorming session
When analyzing open questionnaires, such as survey results
When collecting and organizing large sets of data
When trying to develop relationships between different ideas
Or trying to reduce input to a higher level of categories
Typical process of developing an Affinity Diagram
The Affinity Diagram process gives a group a direction to go beyond normal creative thinking and defines categories to get all thoughts in order. This technique opens the doors and shows relations in between the whole organization which is typically separated due to department silo thinking. The Affinity Diagram has no limits, so don’t be irritated if you have to deal from 20 up to 400 items after a session. It is a starting point not more not less.
Materials needed: Sticky notes or cards, marking pens, and for sure a large surface (wall, table, or floor). Brown paper is a good way to start.
Step 1:
The brainstorming
Write down all ideas on separate sticky notes or cards.
Spread the sticky notes or cards randomly all over the brown paper
Gather all participants around the brown paper after all notes are taken
Hint: Use big markers so it easy to read for everybody from distance. Make key statements on the notes don’t write an essay.
Step 2:
Try to sort all ideas that are related in some way and group them up
Try to find relations between these several ideas
Let the team sort ideas
Try to find 8-10 relation groups
Repeat until all ideas are grouped
It is fully reasonable that there might be an idea staying by itself or that team members will move an already grouped note again to another. If an idea belongs in two groups, make a second sticky note or card.
Hint: In this step it is crucial that there are chats going on, it has to be done in silence. Focus is on sorting and grouping ideas. Headlines are done afterwards! Not upfront!
Step 3:
Open discussion with your team.
Try to find common categories and define headlines for each group together with all team members. Discuss what you see or why members see an idea in a different category. If necessary, make changes and move ideas between categories. In the end, when all ideas are grouped in the consent of the whole team, define the headlines of each group. Try to find a catchy headline that describes the meaning of the category in short.
Hint: Cards with the headline should be in a different color than the rest and should be self explaining about the group.
Step 4:
If reasonable, try to define “mastergroups” of several “subgroups”.
Sort all ideas to their identified category by placing all ideas under the “headline card”.
Hint: The sorting is done by gut feeling, not with a scientific approach.
PPM
The PPM rate (Defect Parts per Million) indicates how many NOT OK parts have occurred per million parts delivered or produced.
Parts per million or also known as Defect Parts per Million
The PPM rate (Defect Parts per Million) shows how many NOK parts have been produced or occurred with one million parts produced or delivered. Rates can be categorized into two main processes. Lower rate on processes where defects can be easily found and higher rate on processes where defects are mainly hidden, e.g. the structure on casted parts. The PPM rate is mainly used to determine the quality capability of deliveries of manufacturing goods.
Thinking about the automotive industry with the SOP (Start of Production) there are still many failures and defects in the process and those must be eliminated through continuous improvement (CIP) measures. In order to take the customer wishes into account, PPM rates are implemented as KPIs to see the progress of your actions concerning the reduction of those defects.
If you are dealing with the automotive industry you will find a lot of PPM regulations and they are often misused as a source of income. OEMs will give you penalties for exceeding the PPM rate, this is a very common approach. Small and mid-sized companies typically sign some sort of quality agreement with OEMs or their customer, Tier 3 up to Tier 1, this is sort of a framework for PPM rates for manufacturing processes throughout the complete value stream of production.
If you have your customer knocking at your door and asking for a PPM regulation, make sure to categorize your production into major fields of operation such as casting, molding, machining, etc. Or if you have dedicated manufacturing lines for your customer try to focus on the end of line quality check and agree on which ratio is acceptable and which not. Don’t go in the details, this will only give you a higher risk of screwing it up and a wider area of attack. And finally try to agree realistic PPM rates, nothing worse than promising something you already know you can’t achieve.
Just to make sure you got this, the way PPM will be evaluated depends on the criteria defined between you and your customers. E.g. agree on with how many non-conforming parts an entire delivery will be rejected.
Until know we looked on it as supplier, so let us change perspective and see it from customer point of view.
Supplier evaluation includes several performance measures in order to compare them and rank them properly. The PPM rate is the most meaningful evaluation to asses the quality among your suppliers. In addition to the PPM rate the number of complaints and costs per defect can be included as evaluation criteria. Specially in the automotive industry there are several rules and regulations but key is certification. You can make sure that your supplier follows several rules by being certified after standard norms, just think about EN ISO XXXX. Even when the certification process can be seen as complete waste of time and money, in the end you know that the suppliers know the rules of the game.
So what to do when the PPM rate is exceeding the agreed limit. First of all your quality management should step in. As customer I would ask for an 8D report, of course depending on the failure rate. Therefore again, agree what limits you will have and at what limit what actions will be necessary. It might also be that you will demand from your supplier to immediately conduct a sorting action.
What ever it is or you will work on make sure to follow a structured approach to successfully tackle the PPM rate. For this we recommend to read the PDCA article or the A3 article. No worries there is more that you can do but in the end problem solving in all the cases always follows the PDCA cycle.
The PPM rate is also a great example for a KPI that can measure the effect of your improvement or KAIZEN actions. You see it is a versatile KPI that effectively runs your business and shows you if you’re on track.
A3 Report
A3 Report and why it will help in the structure of the PDCA methodology.
The term A3 report comes simply from the size of paper which is used for the documentation of the report. The structure itself follows the PDCA methodology.
In the lean manufacturing world the best known use case of the A3 report is the problem solving report. In this case the responsible person from the quality department takes the A3 report, starts the problem solving actions and follows a systematic structure that makes it possible to describe the effects that are currently leading to a deviation from the standard. Using the A3 only makes sense when you don’t know the root cause yet. If you already know the root cause don’t waste your time. Fix it and go back to normal.
Schematic structure of an A3 report
Let us go through the different stages of an A3:
Describe the problem:
The A3 gives you the chance to initially describe the problem or symptoms - this can be done verbally or as a sketch. Don’t forget to mention when it was and under what circumstances. No matter what it must be easy to understand.
Keep in mind that the target in Lean Mgt. is always to train the people to improve their problem solving skills. Therefore if you are a quality representative try to coach the operators in this process or make a team work out of it.
The result of the description of the problem is the delta from the target state.
Root Cause Analysis:
Please be aware that your paper is only and A3 format. So either you go with an Ishikawa or a 5 Why. But not more. If you can’t conduct a root cause analysis with either on of these methods, the A3 is probably the wrong approach at all.
Counter Measures:
Following the PDCA plan your counter measures what you and your team or operators found out or might think have the most effect.
Lessons Learned:
Great you have done the job, you followed the PDCA and the root cause was found, defined measures helped and the problem is solved. No finalize the A3 report on where to find the documentation and what impact will it have on other operations as lessons learned.
When you are a quality representative using the A3 method ensure that the A3 report is also used for long term development of employees and quality standards.
With the help of the A3 report and a clear coaching through the quality department, all employees learn to recognize, evaluate and solve problems on their own. This is serving the general rule of continuous improvement (CIP)
Therefore the A3 systematic increases the problem solving competencies of your whole organization. And as already said, a problem is only the missing of an idea.
If you want to go deeper on the A3 report itself or the problem solving with the help of A3, we recommend our reading pick “Understanding A3 thinking” this book goes in the details and gives you great insights. Read our summary here. Or you can’t wait? Here is the link straight to the book:
Stay Connected
Ad
We want information fast and in a nutshell. We from OI recommend Blinkist* - because it’s simply the best.
* = Affiliate Link