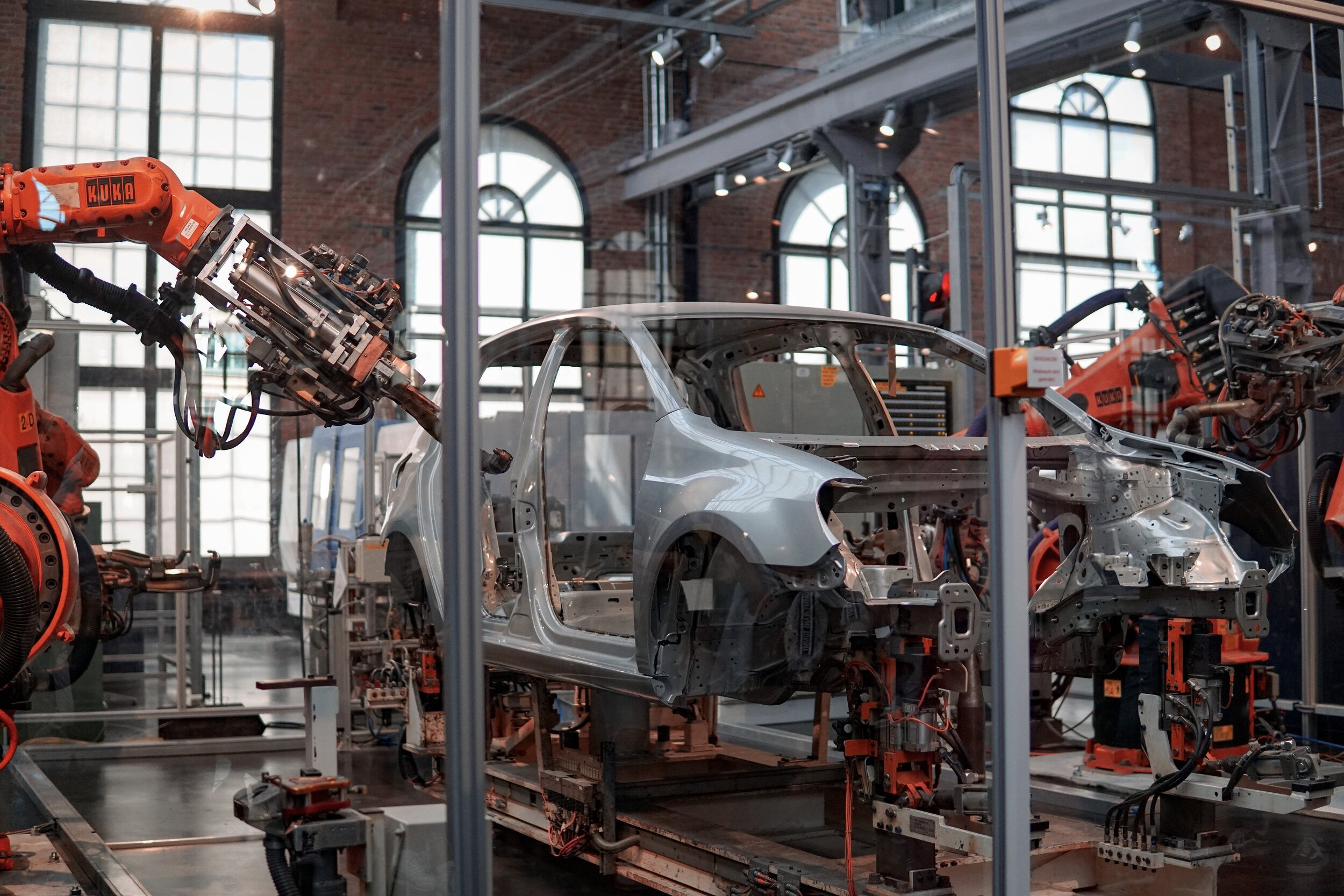
LANGUAGE OF LEAN
Zero Defects
Zero Defects, also known as "Zero Quality Control" or "ZQC," is a quality improvement philosophy that seeks to eliminate defects in the production process.
In other projects we have witnessed the significant impact that Zero Defects programs can have on a manufacturing organization. Zero Defects, also known as "Zero Quality Control" or "ZQC," is a quality improvement philosophy that seeks to eliminate defects in the production process. This philosophy has its roots in the Total Quality Management (TQM) movement and has been widely adopted by many manufacturing organizations.
The Zero Defects philosophy is based on the belief that quality should be built into every product, from start to finish. The goal is to eliminate defects and ensure that products are produced to the highest standard, meeting or exceeding customer expectations. This approach to quality focuses on the entire production process, from raw materials to finished goods, and encourages all employees to be actively involved in the quest for zero defects.
One of the key benefits of a Zero Defects program is that it helps to create a culture of continuous improvement. Employees are encouraged to identify areas where defects are occurring, and to work together to eliminate these issues. This creates a sense of ownership and engagement among employees, which in turn drives improved performance and results.
Another key benefit of Zero Defects is that it reduces the costs associated with rework and product defects. Defects in the production process can lead to increased costs, such as scrap, waste, and retooling. By reducing or eliminating these costs, organizations can improve their bottom line and remain competitive in their industry.
The key to success with Zero Defects is to have a well-defined process in place. This process should start with defining the standards for each product and then identifying the critical-to-quality characteristics that must be met. From there, a detailed process map should be created that outlines the steps involved in the production process, from raw materials to finished goods. This process map should also identify the potential sources of defects and highlight the steps that need to be taken to eliminate these defects.
Once the process map is in place, the next step is to implement the Zero Defects program. This involves training employees on the Zero Defects philosophy, as well as the process map and the critical-to-quality characteristics. It is also important to provide employees with the necessary tools and resources to identify and eliminate defects. This may include things like checklists, forms, and software programs.
In addition to training and tools, it is also important to have a robust feedback and continuous improvement process in place. This can include regular quality audits, customer feedback, and employee suggestion programs. The goal of these programs is to identify areas where defects are occurring, and to work together to eliminate these issues.
Finally, it is important to track progress and measure success. This can be done by tracking key performance indicators (KPIs), such as the number of defects, scrap rates, and customer satisfaction levels. By tracking these KPIs, organizations can determine whether their Zero Defects program is having a positive impact and make adjustments as needed.
In conclusion, Zero Defects is a powerful tool for organizations looking to improve the quality of their products and processes. By eliminating defects, organizations can improve customer satisfaction, reduce costs, and remain competitive in their industry. The key to success with Zero Defects is to have a well-defined process in place, and to actively involve employees in the quest for zero defects. By doing so, organizations can achieve operational excellence and realize their full potential.
Poka Yoke
Poka Yoke are all mechanisms that prevent unplanned mistakes from happening.
Poka-Yoke is any mechanism that helps to avoid unplanned mistakes. Poka-Yoke is that the application of straightforward, error-proof mechanisms to systematically avoid incorrect assembly, mix-ups or the downstream movement of defective parts. As a result of stable and high-quality methods begin long before the assembly section, simple Poka-Yoke measures will be enforced preventively within the construction and coming up with phase to make sure quality. Poka-Yoke is implemented to avoid: going away out or forgetting process steps, process or operational-related mistakes, incorrect or missing parts, setup or installation errors.
POKA YOKE ポカヨケ ("stupid mistakes - avoidance") is associate ideology that takes a spread of approaches to optimize production processes, particularly assembly. The main target of Poka-Yoke is strive for zero-defect production and to attain it approximately. If defects are detected, the cause is determined. If the cause can be avoided, it's eliminated pretty much as good as doable within the sense of Poka-Yoke and at the best doesn't occur again at all. Poka-Yoke was originally an initiative of Dr. Shingo, Shigeo (新郷 重夫), who is additionally a co-founder of the Toyota production system, of that Poka-Yoke is a core component. Poka-Yoke is beneath the umbrella of Kaizen 改善 ("continuous improvement for the better").
Poka-Yoke may be about recognizing the root causes in time and so eliminating them. Mistakes shouldn't solely be corrected, however prevented the in the longterm by eliminating their root causes. Within the ideal case, in the sense of Poka-Yoke, there are measures that utterly rule out a discovered error by eliminating the cause in the future, e.g. as a result of incorrect mounting is not any longer doable because of fixed given mounting ways (e.g. fitting shapes). Poka-Yoke demands product style ability to make a product design that forestalls errors (avoid incorrect operation) and is powerful against errors (despite incorrect operation no faulty processes). Thus the philosophy of Poka-Yoke doesn't solely begin within the production, however already in the product design.
A widely known everyday example is that the plug of the electric devices and the power outlets, that can't be inserted into the socket the incorrect way round. Measuring instruments may also be designed or programmed in such a way that they will not be misused. Poka-Yoke principles can also be found in other cases, e.g. ATMs dispense your credit card before the payout takes place. Fuel dispenser faucets solely work into the right tank for diesel or petrol, creating it tougher to refuel incorrectly. And so on.
Looking at Poka-Yoke in production "Nobody makes any mistakes" is the target of the Poka-Yoke methodology. Here a list of some mistakes that can typically be found in production:
Incorrect positioning of assembly components
Incorrect change of a die
Incorrect mounting
Wrong interpretation of directions
Incorrect polarity in electrical connections
Incorrect reading of measured values
Incorrect connection of hoses
Incorrect entries in devices
Assembly of wrong components
Skipped operations
Operation/programming errors on machines
POKA YOKE follows three simple steps
Measurement:
If you can’t measure you can’t control. Simple fixtures or sensors up to high performance camera systems can support the right execution of processes and provides feedback about the correct or incorrect task completion. Measures can be taken by cameras, mechanical, sensor for light and colors, position, vibration, voltage or temperature.
Detection of deviation:
E.g. deviations are determined by checking the amount of tasks done during one operation - has had the operator enough movement to do the job? Are enough components used? (actual-target comparison). Or simple exploitation geometric mismatches when pins or special marking at the workstation are still visible or not used.
Regulation
When deviations occur make sure that measures are taken such as pulling the ANDON CORD by the so called stop the line authority. Only when error-causing steps are cancelled out a permanent production of OK parts can be achieved.
Only when living according to the Poka-Yoke philosophy on a daily basis and following the principles of Poka-Yoke you will be able to achieve with smart automation and trained operators long term success. Root Cause Analysis and sustainable counter measurements are key. In addition each operator should be trained to detect their own faults during operation.
It might seam to be waste to train operators to detect failures, but no matter how much you planing and effort you put in design, failures occur during assembly or manufacturing. Just think about wiring that is now crossing moving components, parts where the collision was not seen during design and so on, trust me the list can be endless. Some failures will be detected with smart automation checking devices. But these are typically very costly and need special trained people to maintain and most of the time these little pieces of technology can only do one job. Here joins Poka-Yoke the game. Cost efficient, failures or incorrect assemblies can’t be passed on and each operator develops an eye for deviation.
Just keep in mind that if you have mass production or small to middle series can determine if you should install a 100% check or if simple Poka-Yokes can get you where you want.
The most important part of Poka-Yoke at all is that failures are detected when they occur and the exponentially rising costs of defective parts passed on are prevented.
JIDOKA
Jidoka is the Japanese word for automation. It describes a form of automation where machinery stops by itself when defects are detected and notifies humans to clarify what is going wrong.
JIDOKA - the Japanese term meaning automation. In this form of automation the machinery itself is checking the parts produced for defects after processing. With this constant checking of process quality deviations can be directly detected and when defects occur the complete process is automatically stopped until the problem is solved.
You might have come across the word autonomation, which is simply a combination of the words autonomous and automation that describes the automation with still human interactions. JIDOKA has to be seen as a manufacturing principle rather than a methodology. The idea behind JIDOKA is that all machines in the process chain can run without a dedicated operator checking for process stability and quality outcome. If there is a defect or non-conformity of the process, the machine shuts itself down, preventing the defective parts of getting passed on the downstream process steps and for this reason it prevents producing scrap.
In the Toyota Production System, autonomation is one of the main pillar and is also known as intelligent automation as it is firstly focusing on the quality and the ability of a self running system rather than just focusing on the output. You might have also heard the description of automation with a human touch - if a deviation occurs the machine itself will stop the complete manufacturing process and only with the interaction of an operator, after the problem is solved, it can continue production. The upside is pretty clear - you will not produce any defective parts or waste value adding activities on non-conforming components.
With the use of the JIDOKA principle a number of advantages are coming with it:
Processing of non-conforming parts is immediately noticed, so that neither scrap nor rework occurs. Furthermore, no defective parts are passed on to the downstream processes steps
Since the defects are detected automatically, a 100% end of line inspection is no longer needed within the scope of quality assurance
With the help of automatic error detection, operators are no longer needed to monitor machinery, which is no-value adding activity anyway, so it can be declared as waste in the form of waiting time
Operators have now the freedom to perform multiple tasks during the same time or are able to dedicate themselves to new tasks at all
Maintenance activities will also decrease as crashes or malfunction due to the passing on of non-conforming parts is avoided
JIDOKA is the basis of analyzing the root cause of failures and implement sustainable counter measures to avoid these of occurring again
Stop the line authority
Stop the line authority describes the ability or permission of operators to stop the process when problems occur. By doing so it is prevented that defective parts are passed on the downstream process steps.
Stop the line authority describes the ability or permission of operators to stop the process when a deviation or problem occurs. By doing so it is prevented that defective parts are passed on the downstream process steps.
A typical example are so called “Andon cords“ that can be pulled to immediately stop the process and inform the supervisor. To read more about Andon itself go here.
When you are in the lean world you might have come across the famous Toyota quality control mechanism “Andon Cord”. The cord is a simple tool to alert others of deviations or problems in the production line, at Toyota everyone has the authority to pull the cord. By pulling the cord almost instantly production will stop and give the alert to responsible supervisors that there is a crucial issue that needs immediate action. Following the lean principles and shop floor structure, a supervisor would step up and help the operator reviewing the deviation of product or process and define counter measures. When doing so and working with an A3 Problem Solving approach, the supervisor is coaching through the problem solving process and shares with others the outcome or lessons learned on how to prevent this failure of happening again.
In Lean Manufacturing - pulling the Andon Cord is emphasized to all operators. The target is simply to block all defective parts from leaving the company and reaching the customer. At the same time it creates the opportunity to improve your processes to prevent future defects.
NEXT STEP: GO GEMBA
Instead of explaining you the complete principle of Gemba Walks here the short version. But if you want to learn more about Gemba Walks go here.
You can discuss problems as much as you want but when you don’t get yourself to see it, it is worthless. This is where the Gemba Walk comes in the game. Gemba is a Japanese term and stands for “the place where it actually happens”. This can be everywhere and everything in the process chain, but by pulling the Andon Cord the place is defined.
Key of Gemba is not to talk in wild theories or totally abstract about problems, but to have a look where it occurs and discuss them on site (looking at the process in the real world, get rid of unnecessary power points and excel sheets! Nobody cares anyway!) Too often we want to believe the statement of an “expert” and forget about it instead of going there and have a look ourselves in oder to gain a better understanding of the problem and make up our own opinion.
VISUALIZATION
When you are at the place of action, make sure to bring an A3 with you. Make sure that you describe the process properly and the failure that occurred.
In the lean manufacturing world the best known use case of the A3 report is the problem solving report. In this case the responsible person from the quality department takes the A3 report, starts the problem solving actions and follows a systematic structure that makes it possible to describe the effects that are currently leading to a deviation from the standard. Using the A3 only makes sense when you don’t know the root cause yet. If you already know the root cause don’t waste your time. Fix it and go back to normal.
Key Questions are with Gemba Walks and A3:
What should happen?
What is happening?
Explain why!
The A3 Report is foldable and can be then placed at the line or the work station. This is a great and a standardized tool to visualize that a problem is known and on the watch list.
LAST BUT NOT LEAST - STOP THE LINE (JIDOKA)
Now it is time to tackle the hardest part for all players in your organization: STOP THE LINE. In Lean Management, the original term is the Japanese word JIDOKA. This concept is driven by the maxim to have the best quality of goods and to bring the potentials out of the processes or products through continuous improvement. You have to stop all production when a deviation occurs and implement effective counter measures before restarting the line.
On the first view stopping the line might sound hard and insane, as you will stop all value adding activities and actually stop shipping goods. But think about it again. Failing to solve problems when they occur will force you to pile up your inventory with non-conforming parts that will need rework before shipping. You will bind additional resources in space and workers and by that you will burn money. Finally it will keep your organization away to improve and move forward with the developments of the market and with your competitors.
This is exactly the point where the principle of continuous improvement comes in the game, where you see all deviation as an opportunity of improvement.
To practice and learn more about continuous improvement and the CIP methodology, go ahead and read the CIP article here.
If you can’t measure you can’t control
Make sure that you have an organization wide monitoring in place which provides you with all KPIs necessary to run your business. Line stops and counter measures will be part of the tracking process in order to understand if the counter measures are effective, gain a better understanding of the processes and documentation of the improvement process itself.
What is the deviation?
What are the measures implement?
Are the counter measures effective?
You see there is again the logic of PDCA in the continuous improvement process.
All this information will be than part of the Shop Floor Mgmt. to get the information throughout the complete organization and to make sure that all players have the same understanding in what direction your organization is heading.
FMEA
The method of the FMEA - Failure Mode and Effect Analysis has been used for years in the automotive and manufacturing industry.
Failure Mode Effects Analysis - FMEA
The method of the FMEA - Failure Mode and Effect Analysis has been used for years in the automotive and manufacturing industry.
The risk analysis framework has been applied in a wide range of industrial sectors. The first areas of application were traditionally in product development. Based on this the integration of the production process planning and the production. In the automotive industry, the joint creation of FMEA for products and processes by Today customer, supplier and subcontractor are a natural part of a cooperation.
The user is guided through the "10 Steps to Creation of the FMEA".
Step 1 - Review the process
Use a process flow chart or an already existing value stream map to identify each part of a process
List all process steps in a FMEA table
If you think the list gets too long it might is. Use this chance to split up the process and cut the elephant. It makes more sense to work on smaller parts of the process instead of getting lost in the woods.
Step 2 - List potential failures
Review all existing data and documents that can give you a hint about each component that can lead to a failure
After having a complete list try to cut it down and to combine the parts of the initial list
The chances are high that you will identify several potential risks of failures for each component
Step 3 - List potential effects of failures
The effect is the outcome of a failure on the finished good or a process step
It is common that not only one effect will occur for a single failure, don’t be suprised
Step 4 - Assign the level of failure to risks
This is based on the consequences for each failure
Think about the ranking as the worst impact that it can have
Step 5 - Assign the possibility of occurrence
How high is the possibility of occurrence
What impact will it have if occur
Step 6 - How can it be detected
What are the chances that you will detect the failure before occurring
Step 7 - Calculate the RPN (Risk Priority Number)
Severity (S)
Severity x Occurence (S x O) = criticality
Severity x Occurence x Detection (S x O x D) = RPN
Step 8 - Define the action plan
With the decision making process followed by the prioritization from the RPN (Step 7) focus on the topics with the highest RPNs
Follow a classic action plan by defining who will be doing what till when
Step 9 - Take action
Get things done!
Implement the defined improvement actions
Follow the PDCA principle
Plan - done
Do - right now
Check - Step 10
Act - loop starts over
Step 10 - Re-evaluate the RPN
Time to check on the impact of your actions
Re-evaluate each potential failure identified and determine if the improvement measures have an effect or not
If not follow the PDCA and start over with step 8
The FMEA is linked to all CIP and Kaizen activities - there is always something to improve.
Ergonomic Workplace
A work place that takes into consideration most of the ergonomic aspects such as the operator’s height, range and reach.
An ergonomic workplace is a work system that considers the ergonomic aspects of an operation and the operator such as the operator’s hight, range and reach with the goal that the operator does not need to bend or turn.
The ergonomic workplace goes hand in hand with the work improvement.
Definition and purpose
Reveal waste increasing cost and not adding value.
Find waste in the movement of workers, eliminate/improve, pursue net work adding value.
Worker Movement
Lean Manufacturing and Ergonomics may have different roots and directions but together they can complement each other and define a more efficient and safer workplace.
One of the best person known for focusing on productivity and efficiency in manufacturing processes was Henry Ford with the invention of the modern assembly line. Ford really was focusing on eliminating waste and to cut down unnecessary costs in relation to the manufacturing of his cars.
Toyota is one of the best known companies that has stretched to the maximum the idea of Lean Manufacturing and is now holding the pole position when it comes to the reputation according the elimination of “waste”.
By looking at the Lean Model as well as Work Ergonomics, you clearly see the necessity of both practices in the industrial workplace, as well as observe that both can complement each other.
The 7 types of waste to eliminate include:
Transport
Inventory
Motion/Movement
Waiting
Overproduction
Overprocessing
Defects
The list of TIMWOOD is what Toyota has defined as the seven major types of wastes or non-value-adding activities. The seven wastes do not add any value to the product and the customer in the end is not willing to pay for it. Therefore it is essential to remove as much waste as possible which will have also an effect on the ergonomic workplace and furthermore on the health of the operators.
Some of these things like transport, waiting or unnecessary movement can be reduced to a limit what the operator still needs because as human being the operator is limited by his body.
The Lean Manufacturing initiatives and workplace ergonomics stepped into the manufacturing world at different times and therefore are not fully integrated. But you are perfectly advised by combining the principles of Workplace Ergonomics with Lean Manufacturing initiatives. Through a cooperative assessment and teamwork you have the chance to complement each other in making the workplace more efficient and a safer place.
5 Why
The 5 Why methodology is a well known part of the root cause analysis. Key is to ask five times in the row – why?
The 5 Why methodology is a well known part of the root cause analysis. Key is to ask five times in the row – why? It is not the only way to determine the root cause(s) of problems. Just to mention that it usually comes together with an ISHIKAWA analysis. If you want to get deeper into problem solving including ISHIKAWA and 5Why we recommend you the article taking on the 7Steps approach.
The practice of asking why five times in a row whenever a problem occurs supports you on identifying root cause(s) and to determine effective counter measures that are developed through the process of 5Why. Then it is a simple part of PDCA to develop and implement effective measures.
To be able to steer a wide product portfolio, survive the competitive pressure and at the same time satisfying your customers with a high quality product at a reasonable price can be a tough game. Most of the time you don’t have enough time to run the complete product development cycle, do your validation and verification… The end of the story is that you start production because you need to deliver – which automatically leads to mistakes in running daily business. Therefore, the simple method of 5Why can be used to support, not only, your quality department to get faster to the bottom of problems.
The solution for a problem is not always easy, sometimes the root cause is hidden. Therefore the method is an important element of the root cause analysis. One tries to get to the root of the problem step by step with why questions, because one assumes that several causal connections interlock. The system is easy to explain, but there is a lot behind it. If you really take the time to ask the questions carefully and discuss them, the results are extremely profitable.
You should go through these steps of the 5-Why method. Describe your problem as detailed as possible. As more facts you have, you are faster on getting to the bottom of the problem.
What is the difficulty?
When did it first occur?
How often does it occur?
Is this failure randomly coming or reoccurring in a pattern?
Can you repeat the failure?
What is the effect of this failure?
and so on….
It is very important to get a fast idea of the situation on site. Take the Gemba Walk as great opportunity to talk to the people who are actually involved and to see it with your own eyes instead of guessing from your office.
Avoid making assumptions at this stage - you may draw the wrong conclusions.
Keep calm and try to understand the complete context first.
Understanding the context is where the 5-Why method comes in. Gradually ask why questions in order to get a feeling for the interrelationship of effects. This works for many areas of the company, in production, but also in your private life.
Example:
Problem: I miss all the fun part with my kids…
Why do I miss so much? - Because I’m not often at home.
Why am I not often at home? - Because of my position at work I have long working hours and business trips.
Why do I have long working hours and business trips? Because I can’t get my work done in 8 hours and bad in delegating work.
Why can I get my shit done in 8 hours and miss to delegate things? Because I’m sloppy in prioritizing and time management and don’t trust others.
Why can’t I prioritize my activities and don’t trust others? Because I don’t have the information needed to do so.
Reverse conclusion: If I’m not getting the necessary information in a certain amount of time in an acceptable quality I’m not able to steer my employees but also miss the time with my kids.
Sometimes 2 questions are necessary, sometimes 8 or even more to bring you to the “right” conclusion. But don’t give up half way.
Develop appropriate counter measures:
What contributes to solve the problem and who can implement which measures? How long will this take and what consequences will the implementation have?
First: I should try to have set timeframes with my kids which are holy and untouchable.
Second: I should define what information for me is necessary to run my company.
Third: According to the defined Information I train my employees what I need.
Fourth: I implement a clear systematic approach that I have all information latest at 11:00.
(DING DONG - Sounds familiar? BINGO — Shop Floor Management with a functioning meeting cascade.)
Keep the wheel spinning!
No matter what – before start implementing ad-hoc whatever you find best – take your time to identify what actions contribute to a real long term effect, what effects it will have on other areas, etc. Nothing worse than if you think you are doing something great but in reality you make it even worse.
The cycle of questions is often interrupted too early. The real cause is then not really eliminated and after some time there are repeated difficulties.
You can test it: If the reverse of your assumptions works, you are probably at the end of the causal chain.
As mentioned in the beginning another way is the ISHIKAWA diagram
Just keep in mind that not like with the ISHIKAWA the 5 Why only leads you to one cause for a problem. But as always in life there can be more than just one that leads to an effect. Therefore, the combination of 5Why and ISHIKAWA gives you the best approach to determine causes. It will allow you to represent several major and minor causes that can contribute to the solution.
Get the big picture with an ISHIKAWA drill it down with the 5Why.
PPM
The PPM rate (Defect Parts per Million) indicates how many NOT OK parts have occurred per million parts delivered or produced.
Parts per million or also known as Defect Parts per Million
The PPM rate (Defect Parts per Million) shows how many NOK parts have been produced or occurred with one million parts produced or delivered. Rates can be categorized into two main processes. Lower rate on processes where defects can be easily found and higher rate on processes where defects are mainly hidden, e.g. the structure on casted parts. The PPM rate is mainly used to determine the quality capability of deliveries of manufacturing goods.
Thinking about the automotive industry with the SOP (Start of Production) there are still many failures and defects in the process and those must be eliminated through continuous improvement (CIP) measures. In order to take the customer wishes into account, PPM rates are implemented as KPIs to see the progress of your actions concerning the reduction of those defects.
If you are dealing with the automotive industry you will find a lot of PPM regulations and they are often misused as a source of income. OEMs will give you penalties for exceeding the PPM rate, this is a very common approach. Small and mid-sized companies typically sign some sort of quality agreement with OEMs or their customer, Tier 3 up to Tier 1, this is sort of a framework for PPM rates for manufacturing processes throughout the complete value stream of production.
If you have your customer knocking at your door and asking for a PPM regulation, make sure to categorize your production into major fields of operation such as casting, molding, machining, etc. Or if you have dedicated manufacturing lines for your customer try to focus on the end of line quality check and agree on which ratio is acceptable and which not. Don’t go in the details, this will only give you a higher risk of screwing it up and a wider area of attack. And finally try to agree realistic PPM rates, nothing worse than promising something you already know you can’t achieve.
Just to make sure you got this, the way PPM will be evaluated depends on the criteria defined between you and your customers. E.g. agree on with how many non-conforming parts an entire delivery will be rejected.
Until know we looked on it as supplier, so let us change perspective and see it from customer point of view.
Supplier evaluation includes several performance measures in order to compare them and rank them properly. The PPM rate is the most meaningful evaluation to asses the quality among your suppliers. In addition to the PPM rate the number of complaints and costs per defect can be included as evaluation criteria. Specially in the automotive industry there are several rules and regulations but key is certification. You can make sure that your supplier follows several rules by being certified after standard norms, just think about EN ISO XXXX. Even when the certification process can be seen as complete waste of time and money, in the end you know that the suppliers know the rules of the game.
So what to do when the PPM rate is exceeding the agreed limit. First of all your quality management should step in. As customer I would ask for an 8D report, of course depending on the failure rate. Therefore again, agree what limits you will have and at what limit what actions will be necessary. It might also be that you will demand from your supplier to immediately conduct a sorting action.
What ever it is or you will work on make sure to follow a structured approach to successfully tackle the PPM rate. For this we recommend to read the PDCA article or the A3 article. No worries there is more that you can do but in the end problem solving in all the cases always follows the PDCA cycle.
The PPM rate is also a great example for a KPI that can measure the effect of your improvement or KAIZEN actions. You see it is a versatile KPI that effectively runs your business and shows you if you’re on track.
Stay Connected
Ad
We want information fast and in a nutshell. We from OI recommend Blinkist* - because it’s simply the best.
* = Affiliate Link