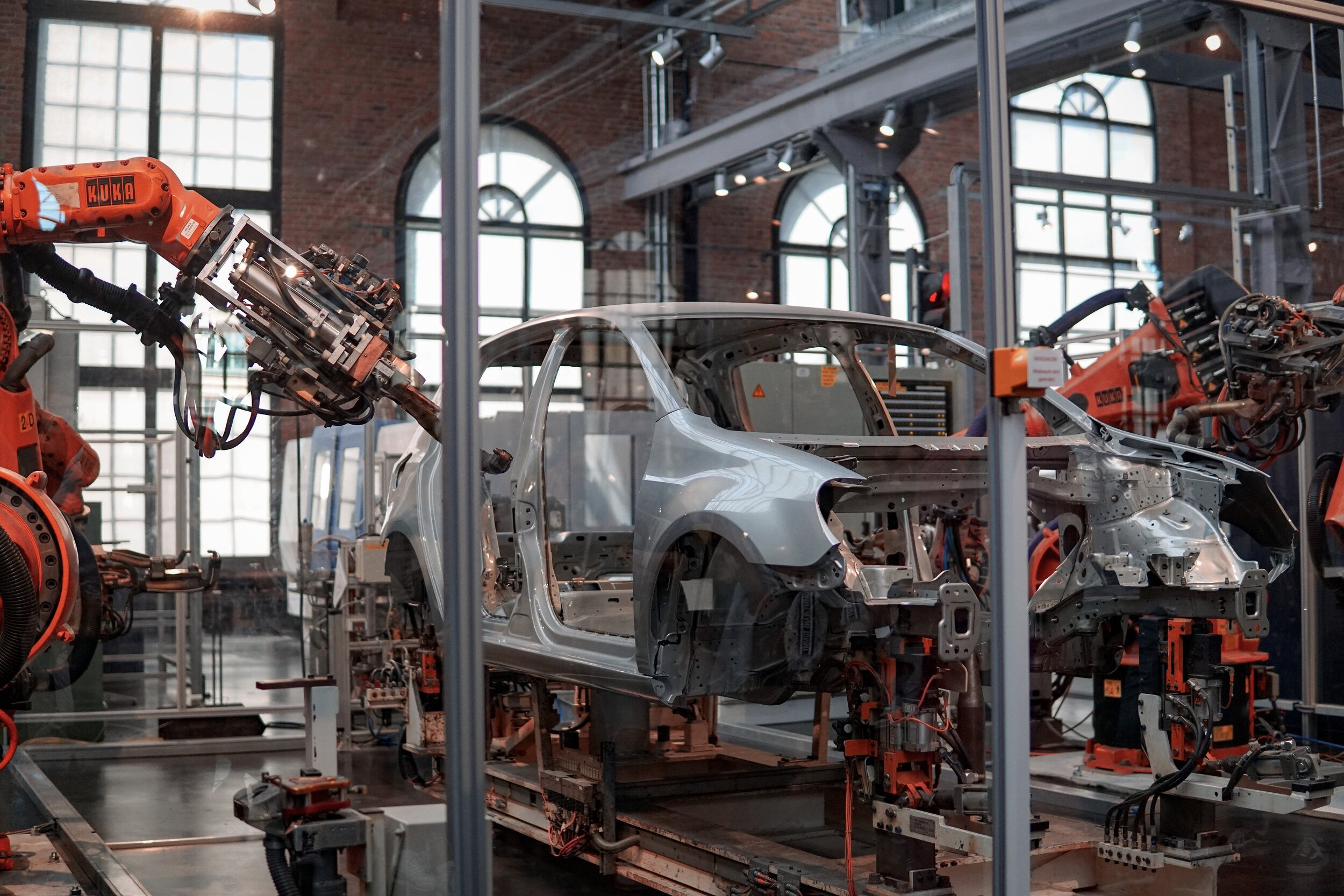
LANGUAGE OF LEAN
KANO Model
The Kano Model shows competitive advantage through knowledge. Therefore it shows the connection between product features and customer satisfaction.
The Kano Model shows competitive advantage through knowledge. Therefore it shows the connection between product features and customer satisfaction.
The Kano model structures and analysis the different types of customer requirements and sorts them into basic, performance and enthusiasm requirements. On the basis of this model, which is also known as the customer satisfaction model, products and services can be further developed which customers are more likely to pay for. The model is named after its inventor, the Japanese professor Noriaki Kano somewhen around 1980.
Thinking about our daily work, the Kano Model is quite interesting for product and service development but can also be used to give some guidance for planned product changes.
Typically when start working with the Kano Model a questionnaire is used to categorize the requirements. This questionnaire then determines which customer requirements should be taken into account for a product and to what extent.
The Kano Model recognizes that customer requirements have three different characteristics that make the purchase of a product more likely if they are met:
BASIC REQUIREMENTS
These are must have requirements by customers for a product or service. There are not highly considered and they alone are not the trigger for the purchase. But if these are missing the dissatisfaction is great. Old but still working example: you wouldn’t buy a car without windshield wipers or a cellphone without internet capability. It is expected to be there.
PERFORMANCE REQUIREMENTS
Requirements that are not taken for granted but are demanded. With a growing availability customer satisfaction grows with it. Performance requirements are defined by the customer, when we stick with the example of a car that means e.g. color, horse power, all wheel drive carplay etc. These are normal customer requirements that ensure higher quality of the product.
ENTHUSIASM REQUIREMENTS
The requirements are not expected by the customer but create enthusiasm when the are fulfilled. E.g. if you buy a new car in the area of the alps and you get free snow chains of a year of free car washes. As customer you do not expect this but you are thrilled when you get it. In other terms we are talking about going the extra mile.
In addition, with the Kano Model you find also those product or service features that are insignificant for customers satisfaction or are even leading to dissatisfaction and therefore rejection of the service or product. However, the absence of such characteristics does not have a positive effect.
What we learn from the Kano Model is that those enthusiastic characteristics become basic requirements over time. You can see this changes ongoing particularly in the technical industry such as car manufacturers and features of new cars, what comes now with the basic equipment was back in time all at extra cost.
The Kano model in practice
Following the Kano approach development teams should constantly keep an eye on the current basic requirements of their customers and try to fulfill on product developments new enthusiasm functions or features.
Customer requirements are typically identified through market research. With questionnaires customers have the chance to explicitly describe their expectations as well as what they don’t need.
Checklist: The Kano model at a glance
With the Kano systematic you are able to structure customer requirements into their characteristics
If basic characteristics are missing, dissatisfaction will occur and the product or service will not fly
Performance characteristics are showing if you understand what the customer wants and if you meet those characteristics the customer is satisfied
Enthusiasm characteristics are showing if you are willing to go the extra mile - long term customer loyalty will be the award
Over time characteristics will shift - so don’t make the mistake and rest on your success
If you want to find out more about the KANO Model I highly recommend Wills’ homepage and tool for KANO surveys. I share his love and believe like him that Kano model surveys should be easy to run. Find out more and visit KANOSURVEYS today.
A3 Report
A3 Report and why it will help in the structure of the PDCA methodology.
The term A3 report comes simply from the size of paper which is used for the documentation of the report. The structure itself follows the PDCA methodology.
In the lean manufacturing world the best known use case of the A3 report is the problem solving report. In this case the responsible person from the quality department takes the A3 report, starts the problem solving actions and follows a systematic structure that makes it possible to describe the effects that are currently leading to a deviation from the standard. Using the A3 only makes sense when you don’t know the root cause yet. If you already know the root cause don’t waste your time. Fix it and go back to normal.
Schematic structure of an A3 report
Let us go through the different stages of an A3:
Describe the problem:
The A3 gives you the chance to initially describe the problem or symptoms - this can be done verbally or as a sketch. Don’t forget to mention when it was and under what circumstances. No matter what it must be easy to understand.
Keep in mind that the target in Lean Mgt. is always to train the people to improve their problem solving skills. Therefore if you are a quality representative try to coach the operators in this process or make a team work out of it.
The result of the description of the problem is the delta from the target state.
Root Cause Analysis:
Please be aware that your paper is only and A3 format. So either you go with an Ishikawa or a 5 Why. But not more. If you can’t conduct a root cause analysis with either on of these methods, the A3 is probably the wrong approach at all.
Counter Measures:
Following the PDCA plan your counter measures what you and your team or operators found out or might think have the most effect.
Lessons Learned:
Great you have done the job, you followed the PDCA and the root cause was found, defined measures helped and the problem is solved. No finalize the A3 report on where to find the documentation and what impact will it have on other operations as lessons learned.
When you are a quality representative using the A3 method ensure that the A3 report is also used for long term development of employees and quality standards.
With the help of the A3 report and a clear coaching through the quality department, all employees learn to recognize, evaluate and solve problems on their own. This is serving the general rule of continuous improvement (CIP)
Therefore the A3 systematic increases the problem solving competencies of your whole organization. And as already said, a problem is only the missing of an idea.
If you want to go deeper on the A3 report itself or the problem solving with the help of A3, we recommend our reading pick “Understanding A3 thinking” this book goes in the details and gives you great insights. Read our summary here. Or you can’t wait? Here is the link straight to the book:
MUDA
Read and learn about the 7 kinds of waste.
MUDA – Also see Timwood
In this article we want to talk about MUDA or the 7 kinds of waste known as TIMWOOD.
The seven kinds of waste have to be discovered and eliminated in daily operations. Therefore we will be looking at the 7 kinds of waste and learn how to use appropriate lean tools to reduce these non value-adding activities.
First of all use Gemba Walks to find out more about whats happening on the shop floor. Only through the on-site inspection you can see what is really going on. It is simply not possible to record the types of waste in the conference room at the green table. The CIP Kaizen action on site is always necessary to reduce waste.
When talking about production the ultimate goal is to increase value-creating activities in the complete organization and not to reduce them. Therefore non-value-adding activities are called MUDA - Japanese for wasteful.
Overview of the 7 kinds of waste and the lean approach to avoid these
The individual parts of muda are easily remembered with a simple mnemonic aid called TIMWOOD. TIMWOOD stands for the first letters of the several kinds of waste. Lets have a look at those and some hints what it means:
T = Transport
Material flow
Product-/Value-/Process orientation
Just in Time material supply of workstations
Pull steering of production with the Kanban principle
I = Inventory
Just in Time or Just in Sequence material supply
Pull steering of production with the Kanban principle
Takt time
Linking suppliers
Reduction of batch sizes or production lots
Implementation of One Piece Flow principle
M = Motion
6 S principle
Standardization
Fixed allocated spaces
Shortest ways
W = Waiting
Multi machining
Multi process handling
Material flow in U-shaped manufacturing lines
Implementation of SMED
Installation of Andon Boards
O = Overproduction
Leveling of manufacturing orders
Mixed-Model-Production
One-Piece-Flow
O = Overprocessing/-engineering
Processes are not necessary
Kaizen activities
Quality circle
Idea Management
Reduction of complexity
Reduction of components needed
Reduction of unnecessary process steps
Reduction of hand overs and quality loops
D = Defects
Reduction of scrap rate or rework
Internal customer supplier management
Self-inspection
Poka Yoke principle
Automation
Zero Defects principle
Stop the line authority
5S activities as part of the standard work
Visual Management and visual aids
S = Unutilized Staff
Idea Mgt.
Shop Floor Mgt.
Lean Innovation
Each of the individual elements of the 7 kinds of waste often interact with each other. If you think about your organization as a system, it is necessary to classify not only one characteristics. An approach can only be derived when several classifications of waste have been analyzed.
The 3 MUDA expressions
With the individual process sections and activities and the corresponding 7 kinds of waste, they can be divided into the following activities:
Value Adding Activities
Kanji Muda - Waste in terms of machinery and equipment
Hiragana Muda - Work that needs to be done in order to fulfill the task but not really add value
Katakana Muda - Everything not needed
All this combined is your total workflow
As seen in real life up to 75% of non-optimized processes are non-value-adding activities which means they are pure waste and eat up your resources. Therefore it always makes sense to eliminate each of the 7 kinds of waste in order to increase productivity. To get an idea see the following picture:
Katakana Muda (red - waste that can be eliminated immediately)
Waiting
Searching
Filling
Double work
Stacking of components
Kanji Muda (gray and yellow - waste based on machines and equipment)
Machinery movement without any function
Oversized machines that can produce more than the required parts during the cycle time
Hiragan muda (green - work that is necessary for the provision of services under the current conditions; value-adding process steps)
Return to starting position
Cleaning
Tightening
Manual operation of machines
So how to recognize and eliminate the 7 kinds of waste?
Muda can always only be detected at the place of action. Therefore Gemba Walks are the best way to go on the search. But one thing has to be clear - it does not have to be always big projects to reduce waste. Continuous Improvement is key - recurring CIP or Kaizen activities are very supportive to develop an eye for the 7 kinds of waste. Training makes masters.
Second - it doesn’t has to be expensive. Most actions can be implemented at low cost. E.g. make a spaghetti plot to visualize and recognize obvious unnecessary movements.
Third - always have an eye on the value-adding activities. With a trained eye from GEMBA WALKS you will have improved awareness of waste already in the planing phase of new processes. Use those lessons learned and avoid waste in the beginning.
We don’t want to go into details but there are two other types of losses that can be witnessed in an organization. Mura meaning deviation and muri meaning overload (man, machine, material equally). If you want to read more about these, have a look here.
Let us come to an end - even when it is hard, we could keep going on and on…
But some rules:
No excuses!
Be creative in first place - money always comes second
Never try to explain why something doesn't work, try how it works!
Adjustments kills your time and ambitions. Adjustment means to fight the symptoms not the root cause!
Do not worry about problems that do not yet exist.
Happy Improving!
The 3 MU
Muda = waste, Muri = overload, Mura = imbalance. Read more about how to define and eliminate the 3 MUs.
In the lean world it is all about “WASTE ATTACK” > eliminate the 3 MUs. It is the bottom line of all KAIZEN and Lean activities. The 3 Mu come from the Japanese words muri, mura and muda. Muda is the most known as it describes waste and we discuss the 7 kinds of waste in the TIMWOOD article. Just to give you a hint TIMWOOD stand for: transport, inventory, motion, over production, over processing and defective parts. These kinds of waste are easily visible by observing manufacturing processes. It gets a little bit trickier if we talk about the other 2 Mu. Muda you get a straight forward feeling, mura and muri are more hidden.
The best way to explain muri is that you are over stressing a system or process. If you e.g. use a forklift that has a maximum of 500kg and you are transporting 1 ton. Your forklift won’t last long. You are either overstressing or trying to do something that can’t be done. The result of it will be a loss in performance.
Mura is unevenness or variation of processes most of the time a result from muri. You can also compare it in administrative work, if you have too little or too much to do. To stick with the example of the forklift, mura would be having only 200kg to load on the forklift on one transportation and on the next route 1.400kg. The result of this variation may be that you try to load 700kg on each route even this is exceeding the max load. The result of it will be that you have breakdowns, defects, excessive motion and other wastes. In all lean management, whether it is manufacturing, logistics, healthcare or knowledge transfer focuses on getting rid of muri, mura and muda in order to improve performance. If you want to get rid of waste in a sustainable way, you have to go upstream and start looking at how products, services or the work itself is designed. You need Value Designing and Value Engineering in the widest sense of the lean terms.
A simple and easy way to make things visible is the classic GEMBA walk – go to the production and see what crime your designers and engineers have committed. Go Gemba helps you to identify and eliminate wasteful steps in assembly and set preventive measures such as Poka Yoke devices to ensure conformity of your products. If we think of designing work itself we want to achieve a continuous and smooth stream of activities. Having this in mind always helps us to redesign processes, get rid of rework, delays or overengineered process steps. Value Stream Mapping as it is done today and redesigning it to focus on fast, high quality hands-off will result in reduced costs and time to market lead times.
MURI in terms of the designing phase will be visible in the need of long working hours to meet the schedule. You will see that it also comes from MURA because the workload itself is not levelled. Who hasn’t been in the situation that you have a design release and suddenly you are twice as busy as before. In the end MURI and MURA leads to MUDA when we start making failures under the pressure of time, when we start releasing before everything has been fully tested or checked.
In the designing phase or let’s say in the creative phase it is typically hard for employees to judge what is waste and what not. It starts with unclear requirements from the customer, but yes some work needs to be done anyway. That’s one point and another one is the mainstream mindset that design is 100% creative and can’t be standardized or quantified. We all heard about Pareto which tells as that 80% of a project are carry over parts and 20% are individual solutions for the specific project.
Lean Design is more a mental rather than a technical challenge.
Carrying on with the example of lean product development, the focus should be to streamline the routine and repetitive work packages so that there is more time for the individual, creative, value-adding part of the project. To clean out your process standardization of items, design elements, documentation, software used and the wiki of Lessons Learned from other projects are just some methods to apply basic lean principles in the development process.
If you think about decentralization of organizations with a global presence, design teams usually suffer from inefficient processes and inadequate design review meetings. Think about standardization as an organization wide language to communicate. If everybody talks the same language you have transparency which rewards you with more time for the creative part.
Considering the cost of delays in time to market, troubleshooting during launch phase and failure occurrence in the field, the design team should think about the rule of ten according costs of failure.
Lean management is based on continuous improvements (kaizen) based on standards and lean design is no different.
GEMBA WALK
Gemba - the Japanese Term for “the place where it actually happens”.
If you’re familiar with lean and you try to talk about it with others it is most of the time reduced on eliminating the 7 types of waste and people are feeling great when they know what TIMWOOD stands for. Don’t get me wrong it is great to have some knowledge and visibility out there but the downside is that it often leads to a quick end on taking action.
The key of lean is to fulfill the customer’s expectations and not reduce overproduction or WIP and all this by solving specific operational problems. The 7 kinds of waste are only the visible downside of weak or bad processes. They are only the symptoms but not the root cause.
This is always the tricky part in lean management. While it is mostly easy to identify waste it gets harder on seeing the root cause of waste in the process.
Lean is about learning to see!
Learning to see is a lean must have and you can call it a real classic in the lean world. This is the holy book of value stream mapping. With value stream mapping you are very fast on describing a process and find out where MUDA appears and how to eliminate it. With VSM you have a great tool to show your given process, analyze it, smooth it out and test some options, before you even touch machinery or equipment. It gives you a blue print of your future process.”
Read more in our reading picks here.
But let’s get to the Gemba Walk Trail
To get used to standardized problem solving in the first step is to go to the place of action. You can discuss problems as much as you want but when you don’t get yourself to see it, it is worthless. This is where the Gemba Walk comes in the game. Gemba is a Japanese Term (well surprise in the lean world) and stands for the place where it actually happens. This can be everywhere and everything in the process chain, starting from typing in customer orders over work stations on the shop floor where you actually add value on something to the fulfillment process in your outbound warehouse.
Key of Gemba is not to talk in wild theories or totally abstract about problems, but to have a look where it occurs and discuss them on site (looking at the process in the real world, get rid of unnecessary power points and excel sheets! Nobody cares anyway!) Too often we want to believe the statement of a “pro” and forget about it instead of going there and have a look ourselves to gain a better understanding of the problem and make up our own opinion.
But above the pure problem solving it is about continuous improvement and the never ending journey of learning.
The question that might raise now is: What do I have to look for?
For this more rhetorical question are countless answers. Just google Gemba in the WWW and you will find plenty of sources and recommendations on where to start and what to look for. Some points that are always included are:
What is our standard? What should be and what is?
Can the person doing the job explain me the standard?
What is the person doing and what is he/she doing deviating from the standard to make it easier?
Why do have a deviation?
Do we need more material in the process?
Do we need less machinery in the process?
Can we do it with less resources?
Are there waiting times?
Do we have defective parts coming in or out the process?
Are we producing defective goods?
How can we identify defects?
Are all documents up to date?
What indicators are used/observed and how are they visualized?
And so on…
As you can see, there is a countless number of questions you can ask yourself and your employees during a Gemba Walk. Each of these questions is correct, important and have a right to be asked. But don’t even think about creating an audit checklist and ask always the same.
To bring it together
Stop thinking upfront what you want to achieve with a Gemba Walk, like improving a specified process, think about Gemba Walks in first place to gain a better understanding of the process flow and start from there making your way down to the root cause of problems in the process. As already mentioned this narrows it down to three simple questions:
What should happen?
What is happening?
Explain why!
Finally – use the chance during Gemba Walks and try to find improvements for visualization at the process. Even if you are not conducting a Gemba Walk – when you’re passing by and clearly see that something is wrong you have the chance to go straight in.
In the end it is all about time and we all know time is money.
6R
6R - The right product at, the right time, at the right place, in the right quantity, in the right quality and for the right price.
Let’s have a look on the logistics in operation. Everybody crossing the way with logistics will hear about the famous 6Rs the “six right ones” they say.
The right components
in the right amount
at the right place
in the right quality
at the right costs
at the right time
To summarize logistics this is it. The 6 Rs show that the main task of logistics is to make material/goods/components available.
You might have heard about the 7th R > the right customer.
So we think 6R are perfectly known as they got taught for decades. But with the lean transformation all over the 7th R becomes key on hitting lean mindset in logistics. It is all about customer centric orientation of the complete supply chain. It doesn’t matter where, how and why in the end you have to start with your customer and build along the upstream your logistics set up.
And here is the most valuable point, your customers are not only outside your organization, they are among your complete organization. If everyone along the process chain sees the next step as a customer, they also have to meet the customer expectations. This gives you a great pull effect throughout the complete process chain and in addition every employee is responsible as supplier and customer, two roles in one person. With this continuous focus on the customers demand or needs, all signs from the market result in a kind of resonance throughout your complete organization and causes an effect.
Logistics made up his way from simple material supply over optimizing material flow to become a crucial part of operations. Nowadays logistics are the arteries of manufacturing industries.
The traditional way to see logistics is seen in the 6R’s as shown in the beginning. For most of the business cases the 6R’s are enough and suitable in practice. But for real operational excellence and an impact on your lean journey keep always your customers in mind.
Following the 6(7)R’s will affect 4 main areas of your production system
Smoothed production
Warehouse organization
Production synchronous material flow
Cell production
Signal Kanaban
Kanban is perfect to steer production and prevent high amount of WIP.
Every container or bin in your production facility is marked with a so called Kanban card or signal. The time the last component is taken, the Kanban is send to the source it came in production and is added to the so called Kanban Board. This board actually shows you the amount of inventory you have in production. It is a great tool to minimize the risk of overproduction and can be used to steer your production facility. Besides this it helps you to have control of your inventories itself of course . Based on the design of Kanban Cards it is possible to identify directly where the container belongs to and in what interval you have to check on it.
The checking and supply of material or components lies in the hands of the mizusumashi.
Takt Time
The rate at which product must be turned out to satisfy market demand.
Takt Time is the beat of your process. When your process is perfectly balanced the complete workload and capacity throughout the complete value adding chain is best utilized to fulfill your customer demands.
So this is already it, the customer determines your Takt. Just have a look on your available net production time and divide it by the rate of the customers demand. I do the exact same thing, when I’m in the role of a project manager I want to optimize the available resources and straighten out the workflow over the expected time needed to finish the project. In the Lean World it is also important to understand the difference between Cycle, Lead and Takt Time if you are running a sophisticated Project or SIX Sigma initiative.
So let’s have a look at the differences
Lead Time VS Cycle Time
It happens very often that people mix up Cycle Time with Lead Time. Most common is the thinking that Cycle Time is the time needed between order placement and delivery while others think it is the pure time between two deliveries.
To put this straight, Cycle Time is the time from when the work is started until it is ended. This brings us to Lead Time.
Concerning Lead Time, it starts with the first contact from customer side e.g. the placement of an order and ends with the shipping.
Easy example:
Order placed by customer on July 12.
Order processed (actually fulfillment of order July 18-20.
Order shipped on July 20.
This gives you a Cycle Time of 3 days but a Lead Time of 8.
This exactly the point where value stream mapping comes into place and can help you on cutting down Lead and Cycle Time, but I will get you there in a different article.
Don’t get on the wrong path of thinking that Cycle Time is the pure value adding, it is simply the time you need for processing the order. That is the reason why should focus on Cycle Time when starting lean initiatives and make your way from there.
Takt Time
Yes it comes from Germany, TAKT comes from Taktzeit, meaning the rhythm of music. TAKT is therefore the beat of your process it is the measurement of your existing production. The Takt Time gives you the maximum amount of time to meet customer demands. In other words Takt Time is the heart beat of your customer and if you are not able to supply your customer in Takt you will bring your customer in struggle. Then you are very quickly no longer a supplier
So what is the Takt Time formula:
(Net Operation Time Available for Production)/(Customer’s Demand)
Always in the given unit of time.
Let’s make an example with the automotive industry:
Your OEM wants 1.000 cupholders per day. You have 8 hrs shift working two shifts per day. That gives you 16hrs per day. Then you deduct times for breaks, distribution time and for preventive maintenance measures, we assume 75mins per shift, this gives you:
16 * 60 = 960 minutes
960 - 150 (75*2 Shifts) = 810 minutes
810 minutes / 1.000 cupholders
= 0,81 minutes per cupholder
or in other words you have 48,6 seconds for one cupholder
Having a look on this calculation you still have to consider some factors, such as operations that are done simultaneously.
The tricky part with Takt Time is that it is based on the assumption that you have a continuous amount of demands coming in from day to day. With high fluctuations on demand you will have to readjust your Takt Time from time to time.
Takt Time is also used to calculated a couple of other parameters, such as batch size, work in progress, shifts needed or operators needed.
What to say in the end…
If you are trying to run KAIZEN actions or CIP measures the first thing to understand is what does Cycle, Lead and Takt Time stand for. Only with the right setting in the beginning your improvement efforts will show an effect.
CHAKU CHAKU
The term Chaku Chaku comes from the Japanese and can be translated with "load load”. Also in general it has become a term for variant of a flow or series production, and the work in it.
The term Chaku-Chaku comes from the Japanese and can be translated with "load load”. Also in general it has become a term for variant of a flow or series production, and the work in it, naturalized, at of all the workplaces involved in the production of a product following each other so that the shortest possible distances between them are possible. Since there must also be space for transport, this is usually a u-shaped or omega-shaped formation.
The basis is multi-machine work: one operator works on several process steps. It is usually his task to load and unload the material. The stations work independently without the intervention of the operator, often simple tasks are taken over by the operators in order to save on machine purchases. In practice, the operators only take over the transport from station to station, sometimes there are “mini” buffers provided at the stations, in which a machined work piece can wait for a short time.
Through the Chaku Chaku production system, also known as flow production, can be different depending on the complexity of the parts to be produced also refrain from purchasing machinery or even dismantling machines. These machine systems are then replaced by mostly simple manual workstations.
In a Chaku Chaku line the operator primarily performs the loading and starting of the stations through. The material is supplied from outside, safety measures to the employees and the ejection of machined parts are automated. The capacity of the line is mostly determined by work distributions of one to three operators flexibly. The advantage of this system is that:
thus the usually high acquisition costs for complex interlinking machines
and the training time of the workers employed is usually shorter, since the
activities are often of a simple nature, and therefore don’t require extensive instructions and
there is no training on complex machines.
Also, with the Chaku Chaku principle, the cycle time can be controlled individually, for example, if the pre- and downstream machines run at different speeds, this will be controlled by the operators.
The structure of a Chaku Chaku Line is based on the simplest production principle in which manual labour is the most important factor.
The operator has to fulfill transport, quality control and process monitoring for this. In the manufacturing process, the principle applies that the machine is maintained and not man. Expensive technologies require a high occupancy of machines, are less flexible for fluctuations.
In the simple Chaku Chaku Line it is easy to achieve the required number of units through the design of flexible deployment of operators.
Hancho
Read how a Hancho will support your organization as the first management level on the shop floor.
A Hancho is the first management level in a lean organization. A hancho is the technical manager or team leader (speaker - Japanese chô) in one part of the process or a small group (Japanese han) and typically consists of 6 to 10 employees. A Hancho masters all processes in his /her area, receives a slightly higher wage (5-10 %) than normal operators and is selected and appointed by the company. The hancho’s responsibilities include reacting to abnormalities and promoting standardized work and the process of continuous improvement.
In order to increase productivity the Hancho is the key player in his role as a team leader. Above the Hancho level your organization, depending on size, has the group leaders which are having a larger number of employees underneath them.
In order to implement the role of a Hancho you need define several aspects upfront. Just answer some questions to yourself:
How many Hanchos do we need?
What will be their daily tasks?
Which qualifications are a necessity?
Which employees are suitable for this role?
Does the employee have the right professional and social qualifications?
At Toyta e.g. the Hancho has following tasks:
You see that most of the time is used for problem solving and the dealing with absence. In best case the Hancho is dedicated to only this tasks, because he contributes the most for a successful continuous improvement management on the shop floor.
Heijunka
How to level production with the help of Heijunka.
Heijunka is a tool in the lean world that is striving for a leveled and smoothed dispatching of manufacturing demands which therefore leads to a reduction of waste. The meaning of levelling is to transform irregular incoming orders into uniform production batches. The target is to bring all demands on the smallest batch size possible based on a leveled production pattern. The Heijunka Board visualizes the predefined production plan for the production process. The beauty of it is that it enables you with little effort of control to implement a steady and synchronous flow of production.
If you are in a leading manufacturing position you already know how painful it can be to maintain a steady flow of work.
Customer demands are typically not perfectly leveled and this fluctuation needs to be translated into a defined takt that is given by your production process. To keep up with the incoming stream of orders and to avoid overproduction and therefore tied up cash, Heijunka can help you lowering the peaks and smoothing out production.
Heijunka is a well-known lean method for smoothing and reduce the over stressing of a production process. Heijunka is Japanese and means roughly translated levelling. The main reason for implementing Heijunka is a faster reaction time on fluctuating demands and improving the utilization of installed capacity.
With the help of Heijunka you minimize the sizes of batches to smallest size possible and start processing customer orders based on demand. This will support you on reducing your inventory as you will stop producing based on utilization of line capacity and then pile up finished goods without being sold.
At the bottom, Heijunka allows you to produce and deliver value to your customer at a steady pace and gives you the chance to react faster on deviations, while not overstressing the process. Therefore this method gives you always two options for levelling your production: By type or by quantity.
Balancing by type:
Go through your portfolio and define the average demand of each product. Based on the average demand the production is smoothed out to meet it. The target is to level the capacity of our line. Use Heijunka to keep up with the demands of each product of your portfolio and use it to visualize the production plan.
Balancing by quantity:
The main road blocker to establish a smooth and continuous production flow is producing in batches. The target is clear: produce only what is ordered. Therefore, Heijunka enables you to level your production by the average volume you get. By levelling your production this way, you will be able to achieve all demand by the end of the week. With the help of Heijunka you will keep your processes running without overburden it when unplanned peaks are coming in.
The Heijunka Box is a tool implemented on the shop floor in order to visualize the workload that needs to be fulfilled in order to meet the average demand. Simply spoken it has cards spread over the week for each product in a logical sequence to reach optimal flow.
The Heijunka Board
Usually the Heijunka box is set up in a matrix with the first column separated by product type for each line, the following columns are the workdays of the week. Therefore your Matrix defines Product type and the quantity that needs to be produced on a specific day. Two ways are most common, either as boxes where cards are placed in or as a board with magnetic cards that stick on it.
Depending on your installed capacity and the team size you want to cover with Heijunka you might need multiple Heijunka boards. Typically the cards you use are having the format of Kanban cards, that are following the process of the processed good until the end and then are placed back to the collection box for new planning.
Heijunka is a great lean method that allows you to organize your workflow around average customer demand. You protect your processes and employees from over stressing due to uneven production and quantity sizes. Furthermore, it supports you on realizing a complete pull system throughout production.
Bottleneck
Bottlenecks are the pacemaker of your process chain.
Bottlenecks in your process are the pacemakers of existing processes. These means if you tackle your bottlenecks in your process chain, it will have a direct impact on your cash flow.
A Bottleneck in a process chain requires the longest lead time of operations, A typical indicator for a bottleneck station is a upstream increased inventory or Work in Progress. The bottleneck is therefore the weakest link in the chain.
If you are running improvement or KAIZEN Workshops on your bottleneck station the upstream or downstream process steps will never be above 100% of performance. If so the bottleneck station changed to a different process step.
Bottlenecks are great to improve!
The potential of removing bottlenecks is unbelievable high, if you miss the chance to tackle the potential of bottlenecks in order to increase your throughput you are missing the chance to increase your performance and exceed customer demand/expectations. It is quite simple – the cost per hour of a bottleneck station can be seen as the loss of one hour of your complete process chain (e.g. production line) incl. the loss of parts not produced.
The whole deal is about increasing the throughput of your assembly line, to use machines efficiently combined with optimized operator working steps to increase the profitability of the assembly in total. Don’t make the mistake and focus only on the cost reduction part of it think and don’t be fooled by thinking in partial optimization.
To bring it to the point: In manufacturing, bottlenecks are continuously slowing down the whole assembly line. Focusing on permanent existing bottlenecks will sustainable improve the performance of the whole process chain and effect even other areas.
Pareto Chart
A Pareto Chart is used to help determine the waste characteristics of a product.
A pareto chart is used in order to determine the waste characteristics of a product/good but also of processes. They are sorted onto a cart so that the most frequent defects can be visualized and stand at first place.
Today, I am writing this blog post after discussing several times with colleagues who want to understand the Pareto chart (or Pareto diagram) more deeply.
The Pareto chart is one of the basic tools of quality management. Usually, this chart consists of a combined bar and line graph. The vertical bars are representing the quantity of defects, and the line represents a cumulative percentage of the defects.
The descending order of bars is from left to right. The bar on the left will have the highest value, and the bar on the right side will have the lowest value.
Let’s discuss this in detail.
Pareto Chart
Sometimes, it is challenging for you to understand the problems and their causes. Instead of focusing on the root cause, you spend your time, solving problems, which were influencing the project least.
The Pareto diagram can help you overcome this situation. The Pareto diagram can help you segregate the defects and their cause. Once you get this info, you can focus on the cause which is generating the most defects.
The Pareto diagram is based on the Pareto Principle, which was developed by an Italian economist named Vilfredo Pareto. He found out that 80% of the wealth was spread to 20% of the population. Therefore, pareto is also known as the 80/20 rule.
We could now list several examples where this rule is confirmed such as
80% of the defects are coming from 20% of the process
or
80% of customer complaints are coming from 20% of all defects detected
or
20% of the defects are causing 80% of the problems…
The list can go on and on.
In general, this phenomenon can be interpreted as follows: Roughly 80% of the problems will be due to 20% of the causes, or the majority of issues will be due to a small number of causes.
However, keep in mind that the above rule is a general rule and the ratio is not absolute.
The Pareto chart is mainly used in quality management or Six Sigma approaches. This chart helps you to find the majority of the problems and their root causes. You then should focus on tackling those causes and therefor solve the majority of the problems.
How to Draw a Pareto Chart
Drawing a Pareto chart is very simple. The most important step is to collect the correct data.
The steps to drawing a Pareto chart are as follows:
Categorize your potential causes
Specify the measure, e.g. quantity, costs per failure, downtime, etc.
Set a time frame you measure, e.g. per shift, per week, etc.
Measure Measure Measure (If you can’t measure you can’t control)
Separate the data based on the categories
Draw a bar chart with causes on horizontal axis and number of occurrences on the vertical axis (Excel gives you predefined templates)
The category with the lowest quantity will be at the right and the highest quantity on the left
If you don’t have the histogram preset chart in excel - define a second row with the percentage value. Accumulated up to 100%. This will be your secondary axis. The values in percent will form the curve of distribution.
.To make it short - it should look like this:
Pareto Chart
Now, you can focus on the causes generating the majority of problems, analyze them, find their real root cause(s), and start to get rid of the issues one by one.
This chart can help everybody to identify causes of the most common problems. It also supports on prioritizing tasks and activities for KAIZEN Workshops or simply fire fighting. Having some Excel skills, it is very easy to create a Pareto and also often helpful communicating your actions to the upper management - you can bring it to the point.
This reading pick is not focusing on the professional approach of the Pareto (meaning quality matters in manufacturing) but more looking at the personal usage of the 80/20 Rule. We love it as it shows you how to focus on what really matters in live.
Read more in our reading picks here.
5S
The 5S Method is a five-level system for the provision of safety, cleanliness and orderliness on the workplace.
The 5S Method is a five-level system for the provision of safety, cleanliness and orderliness at the workplace. The term „5S“ is coming from 5 Japanese words that begin with the letter „S“.
These 5 words describe the 5 principles for the organization of the workplace:
1S – SEIRI
Cleaning: Sorting-out and get rid of all unwanted objects.
2S – SEITON
Orderliness: Clean-up and proper arrange tools needed.
3S – SEISO
Cleanliness: Maintain cleanliness at the workplace and keep the standards established through 5S workshops.
4S – SEIKETSU
Standardization: Establishing work standards developed by 5S sessions.
5S – SHITSU
Discipline: Observing compliance of new work standards and drive for continuous improvement.
Why do we need 5S?
Goals of the 5S during the implementation:
Safety
Flexibility
Quality
Costs
Ergonomics
How can you implement 5S at your organization?
How to implement 5S
The 5 steps of the 5S-Method:
Sorting out all unnecessary objects at your workplace
All needed objects have to be arranged in a proper way
Keep your workplace clean
Standardize the steps 1 to 3
Keep your new standard or improve it even more
5S is a continuous process!
The 5S checklist
In order to maintain the 5S procedure and standard you should be implementing a routine of a so called 5S audit. The 5S audit is an instrument of sustainable implementation of the five step system for safety, cleanliness and order at your workplace.
Therefore 5S is relevant in all areas of your company, no matter if you are working in a office or your focus is on the shop floor. To maintain the 5S implementation and the ongoing improvement of all 5 steps. The audit can support you on identifying deviation and to improve.
So why do you need the 5S Method?
It supports you on
Reduction of uncleanliness and its causes in the company
Reduction of latent waste in the company (e.g. untidiness, unneeded objects)
Reduction of defective equipment and tooling
Reduction of deviations from standardized manufacturing procedures due to unnecessary objects and frequent searches for misplaced objects
Increasing the awareness of the employees about tidiness, cleanliness, waste and deviations from standardized manufacturing procedures
Enhancing the positive impression of the company towards the customer
So what are the goals when you implement 5S in your company?
1 Increase safety at the workplace
Everything lies in its right place and employees receive a standardized and up-to-date description of their workplace
The employees know where to find everything needed in the case of an emergency
Markings on the floor are used as a visual control aid to help the employees to stay clear of any dangerous situations
2 Increased capability to react
Expeditious reaction to the requests of the customer and expediting the manufacturing process
By involving all employees, the internal flow of communication is enhanced along with the identification and removal of mistakes
It supports the expeditious preparation of e.g. work procedures, replacement of tools, increased flexibility of the employees, streamlines the work processes, increases the general economy by making the work procedures more effective; and expedites the continuous process of enhancement
Mistakes and deviations from the standardized work procedures become an exception and can be quickly eliminated
This reading pick will show you the methodology as well as real doing and conducting of 5S Sessions. It is a great guidance and a step by step instruction with lots of advice and practical tools that will allow you to conduct your 5S project from A-Z.
Read more in our reading picks here.
3 Enhanced quality
The proper arrangement of material and equipment decreases the amount of defective products and improves the repeatability of the work process
Enables the employees to determine at first glance what is needed to do to ensure quality
Makes the problems more perceivable and thus enables their solution
4 Cost reduction
Shortens unnecessary searches and reduces the time needed to find objects
Shortening time for exchange of tools > SMED
Creating new areas
Eliminating all unnecessary objects
Too excessive or insufficient supplies are discovered and are made visible
Expedient realization of counter-measures
5S designates the 5 basic principles for creating a clean, well-arranged and effective workplace with competent employees – the basis is orderliness = 5S.
5 Developing a “Visual Workplace”
In the case of a visually created workplace the work procedures are adjusted to enable all employees to have the possibility to observe the actual work process
Visualization:
Organization of the workplace
Manufacturing process
Distractions, such as defective objects, sources of danger etc.
Production indicators (plan, overproduction, or as the case may be, underproduction)
How can a 5S Audit support you?
The 5S Method makes sure that each workplace, in the production or office, is organized according to the principles of cleanliness, orderliness and safety
To secure the permanence and the continuity of adherence to the defined 5S standards it is necessary to regularly conduct 5S Audits
For the different areas of Production or Administration and others, specific questionnaires are prepared, on basis of which the obvious deviations from the defined planned state can be detected
The 5S questionnaires are combined with a list of counter-measures necessary to rectify the situation along with the names of responsible persons
Push vs Pull Principle
One of the four building blocks of lean production. Push vs Pull production.
The pull principle is one of the main blocks in lean manufacturing > pull manufacturing. The customer demand determines which good will be produced and in which quantity. Max/Min inventory levels are agreed with suppliers and customers. This gives you the opportunity to limit overproduction.
In a pull process a workstation or process step is only being triggered when the downstream processes are free to take the output. This means that only when the customer initiates a need the value adding is started. By this a customer can be seen as internal as well as external one. This is lovely as you make sure that only what you will sell will be produced.
Pull is always to prefer against push. As it allows you to manage the WIP and inventories in between workstations which has a straight impact on your lead time. To successfully install a Pull System you have three choices, it is either the well known continuous flow installed, sequential pull or the replenishment pull.
All three types of connection will help you to achieve different levels of Pull in your environment.
No matter what it always comes down to three factors in your system:
Having max one piece of inventory between two process steps
Having a fix production sequence
and having a max number of parts waiting
Thinking about the three types of a Pull System, the continuous flow system has the highest level of Pull, as all three factors are highly involved. Only One Piece at the time and in between two process steps which means a fixed sequence as well as max one part waiting for the next process step.
If you have several workstation linked in one main manufacturing process working on one final product you have a work cell or simply a production line, depending on the shape you can call it e.g. U-cell.
With the sequential pull system you will have the second best choice of a pull manufacturing. It will have a fixed quantity, the sequence of production is defined but with a max number of WIP allowed between process steps. Basically you will allow buffers in your manufacturing. This can typically be seen in FiFo lines (First in First out).
Last but not least we have a look on the Replenishment Pull. This is in other words your supermarket in the production and your third and last option of implementing pull. The supermarket has a maximum number of components, parts or products waiting to be worked or processed on. But it is not known which one will be next. This type of inventory is usually steered or controlled using the Kanban systematic.
To put it in a nutshell - the following table should be fine to give you an overview:
Autounloading
In the lean world “auto unloading” means that every machine is automatically unloading the processed part or component, so that the operators’ task is reduced to only loading the machine.
In the lean world “auto unloading” means that every machine is automatically unloading the processed part or component, so that the operator’s task is reduced to only loading the machine. This also refers to the chaku chaku principle. The correct lean term of autounloading is the Hanedashi Principle which is explained here.
Ishikawa (Fishbone Diagram)
An ISHIKAWA is a chart that resembles a fish skeleton, with a main spine and branches (bones) drawn at a slant off the spine; used for quality control in two main ways.
If you are running problem-solving you will come across the so called ISHIKA (or Fishbone) diagram. An ISHIKAWA is a chart that resembles a fish skeleton, with a spine and bones drawn slanting off the spine; used for quality control in two main ways:
As a cause-and-effect diagram, where the spine leads to an effect (head of the fish) and the “bones” are cause factors
As a subdivision of quality requirements, where the spine represents a quality objective and the bones describe subsidiary traits or measurements that are important but are not the end in themselves. (Sometimes referred to as a Reverse Fishbone)
The fishbone diagram is simple to use and allows a quick and effective root cause analysis and to understand what corrective actions can be taken to have fast success. It is used for brainstorming and often in conjunction with the 5 Why Methodology.
In a ISHIKAWA, the various causes are grouped into categories and the causes cascade from the main categories, flowing towards the effect, forming what resembles a fishbone appearance.
The first step is to brainstorm all possibilities that could cause the problem and then drill it down to the factors that are causing the effect. Once found it is the task to eliminate them. It enables the team to focus on why the problem occurs and not the history of symptoms of the problem. It also displays a real time snap shot of the collected inputs of a team as it is updated.
How to Conduct a Fishbone Diagram
Draw the box on the right of a flip chart, large brown paper or white board, and write the problem statement (effect) in the box. Be as clear and specific as you can about the problem.
Now draw the line going from left to right as the ‘spine’, connecting to the problem statement.
Draw the ‘fishbones’ emanating from the spine. These represent the main cause categories.
Now label each Fishbone category. There are two options here. You can use the generic cause categories of Environment, Machine, Man, Material Methodology, which is easier to use for a team that is relatively new to this method but, but you can also use the brainstorming in the group to define the major categories related to the specific problem.
Now brainstorm all the causes to the problem. You could use the approach of writing each cause on a sticky note, going around the group asking each person for one cause. Continue going through the rounds, getting more causes, until all ideas are on the board.
For each cause, agree in the group which category the issue should fall in. (An issue can be addressed in several categories) and continue this process until the group have run out of ideas and all potential causes are at least placed under one category.
Next, get each team member a marker or sticker dots to mark the top three causes they think have the highest effect on the issue.
Not always mentioned but for us very important – also differentiate between the factors in three sectors
Factor of non conformity (process, drawing, etc.)
Factor for non detection
Simple cause
Once completed, the facilitator adds up all the markings for each cause and selects the top three with the highest scores. These three issues will now form the basis of additional investigation in order to find the root cause. The team may then investigate these causes further and use problem-solving techniques like 5 Whys to eliminate their occurrences.
An example Fishbone Diagram
A typical use case in industry is that a production facility has a too high scrap rate. Manager comes in and says “solve it”. As mentioned above the cross functional team gathered all data and ideas during a brainstorming session and listed all possible causes into the main categories.
The next step would be to pick the top three causes and delve deeper to find the true root causes.
Example of an Ishikawa Diagram
Some hints:
Remember, as with any task-based activity, always close a problem solving session with actions, clearly assigned owners and due dates – “Who is doing what by when?” This is important, as it keeps the teams focused on the project. Do not end up with an excel LOP use the Workflow Board instead to steer and assign tasks. This is great way to have transparency on task tracking and assignment
Don’t assign huge tasks which require several weeks to fulfill. Cut the elephant in pieces. Set up a regular meeting twice or at least once a week.
Hold people accountable and summarize the session, including the actions and deliverables
Have regular reviews with the team in between, therefore use a stand up meeting to gather the team and check for status against the actions planned. (Workflow Board)
Make every tasks as clear and simple as possible, so everybody of the team understands what is expected.
Besides ISHIKAWA you can also use, as part of Visual Management, the so called KAIZEN Board. It is a great opportunity to tackle issues before they become big problems. Also here it is a must to run it with discipline and continuity. It will support you on systematically embed problem solving behavior and continuous improvement culture in you company.
If you want to go deeper in the Ishikawa problem solving I recommend the book from Mickael Réquillard.
In this book, you will discover what an ISHIKAWA diagram is, its different representations and use cases, how to create one and how to effectively exploit the information gathered.
Read more about the book here or get it straight from amazon.
Stay Connected
Ad
We want information fast and in a nutshell. We from OI recommend Blinkist* - because it’s simply the best.
* = Affiliate Link